10 Reasons Why Manufacturers Need to Go Lean
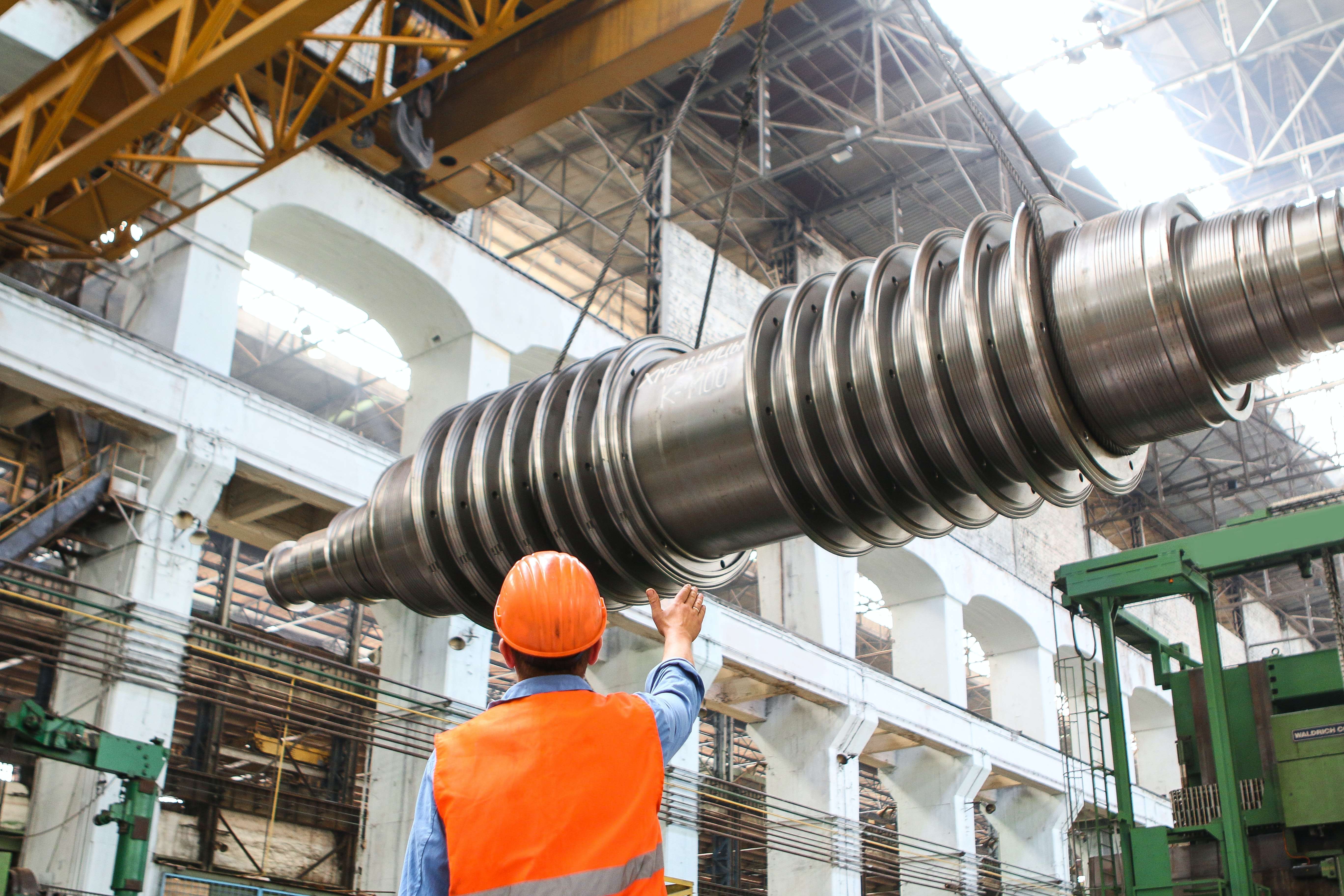
Lean manufacturing focuses on cutting down waste while maximizing productivity
Manufacturing is one of the largest industries in the world, generating trillions of dollars worldwide. In a sector as massive as this one, individual companies need to do everything they can to stay competitive. One of the most promising approaches to boosting a company’s value is lean manufacturing.
Lean manufacturing focuses on cutting down waste while maximizing productivity. No manufacturer would consider that a negative thing, but given all the work it takes, some may not want to pursue it. Going lean is a long and highly involved process, but it can revolutionize manufacturing.
Here’s why manufacturers, especially in today’s world, need to adopt a lean approach:
1. Boosted Efficiency
The first and most immediately evident advantage of lean manufacturing is that it improves efficiency. A central tenant to going lean is removing waste, and that includes inefficiencies within the workflow. By removing as many time-consuming tasks as possible, lean manufacturing makes workflows more efficient, which in turn boosts profits.
2. Minimized Production Costs
Some manufacturers look to maximize profit by raising the selling price of their products. Lean manufacturing takes a different approach, increasing profits by reducing the cost of production by eliminating waste. This approach is how Toyota became the world’s most valuable car manufacturer while selling reasonably priced cars.
3. Reduced Product Defects
Lean manufacturing also reduces the likelihood of defects, creating a better product and avoiding costly reworks. Product errors are one of the areas of waste that a lean approach aims to eliminate. Instead of producing more to make up for defects, a lean manufacturer restructures their workflow to stop these imperfections from happening in the first place.
4. Increased Customer Satisfaction
One of the results of a lean manufacturing strategy is the consistent delivery of timely, quality products. Maintaining a consistent level of quality will help manufacturers develop a more satisfied, appreciative customer base. That satisfaction will create loyal return customers who will convince more consumers to try the same products.
5. Improved Public Image
Building a loyal customer base will help create a more positive public perception for manufacturers. That will only increase as manufacturers continue to use fewer resources as a result of going lean. Given growing concerns over how many resources corporations consume, the public will appreciate it when a company is committed to using as little as possible.
6. Decreased Environmental Impact
All of that resource conservation also helps manufacturers become more environmentally sustainable. The manufacturing industry is notorious for its significant environmental footprint, which becomes increasingly severe as climate issues continue growing. Eco-friendliness is also profitable, as General Motors saves $2 million a year by water reuse alone.
7. Greater Flexibility
By minimizing waste and maximizing space, manufacturers make their operations more flexible, which is essential in a rapidly changing world. Traditional facilities often have substantial amounts of in-house inventory, which can be a problem if markets shift suddenly. Lean manufacturers don’t have this problem, so they can adjust with less disruption.
8. Built-In Safety Benefits
Lean manufacturing requires more attention from employees as they work on products — this is to avoid defects. This heightened engagement also improves safety within a facility. Studies show that highly engaged employees are involved in 70% fewer safety incidents than workers who aren’t as engaged.
9. Heightened Employee Morale
Wasted potential is another area of waste that lean manufacturing addresses, helping employees achieve their best. When workers feel under-utilized, it can harm their morale. Since lean manufacturing encourages employees to be more engaged and reach their full potential, workers’ spirits can improve.
10. Continuous Improvement
Lean manufacturing isn’t something that a facility achieves, but rather, it’s a culture of improvement. There will always be some way that processes can reduce waste and increase productivity. By adopting a lean approach, manufacturers engage in practices that will help them keep improving with time.
Lean Manufacturing Is Crucial in the Modern World
In the modern manufacturing world, competition is high while some resources are running low. Lean manufacturing helps companies deal with both, making more with less. By cutting out waste and boosting productivity, manufacturers can improve their value exponentially.
Emily covers topics in manufacturing and environmental technology. You can follow her blog, Conservation Folks, or her Twitter to get the latest updates.