Increasing tool life with precision cooling
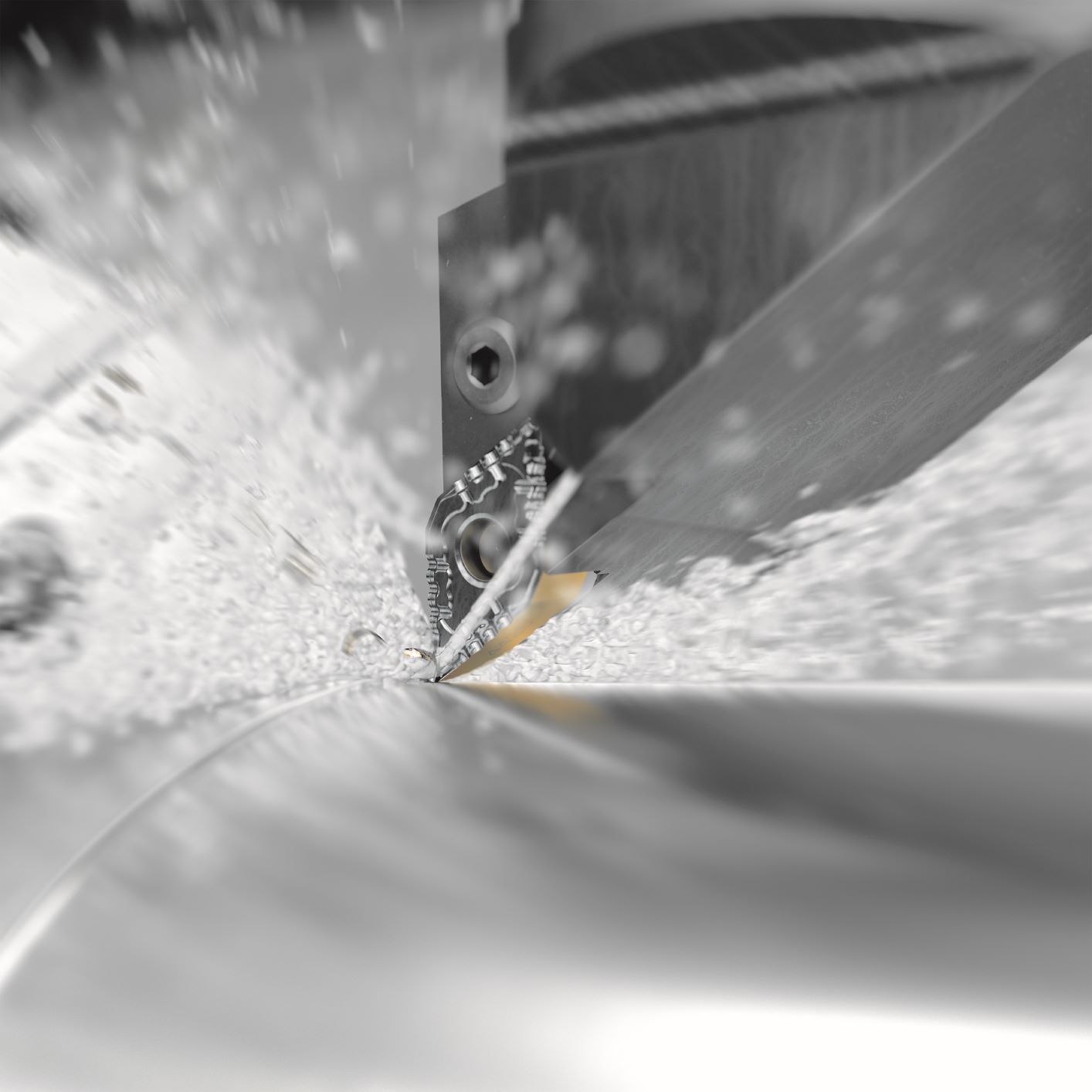
Sandvik Coromant upgrades long-standing tool family with precision coolant technology
Global leader in metal cutting, Sandvik Coromant has upgraded its Coromant Capto® tool holders for the T-Max® P carbide turning insert. The tool holders now include through-tool delivery of precision over and under coolant. Precision coolant is especially advantageous for machining ISO S, M and P workpiece materials and, with this addition, the new holders increase tool life and boost productivity.
Operations like steel turning create a high pressure environment for metal cutting tools. As such, turning tools that feature nozzles to deliver precision coolant to the cutting zone can control chip breaking and offer secure machining. In addition to regulating chip breaking, implementing coolant controls tool temperature for a long and predictable tool life, while also offering positive effects on surface quality.
Due to the benefits of using precision coolant, many of Sandvik Coromant’s tools for steel turning applications feature a degree of cooling technology. Now, one of Sandvik Coromant’s most widely-used group of turning tools is receiving the upgrade.
T-Max® P inserts are specifically designed for high-performance turning in modern production, while the Coromant Capto® is a modular, quick-change tooling concept, which offers a large variety of extension and reduction adaptors to support assembling of tools with different lengths and design characteristics. As part of a tooling offering that combines the modular Coromant Capto® interface with the T-Max P® clamping insert, the Coromant Capto tool holders for the T Max® P come in two designs: the T Max P® lever clamp for turning medium to large components and the T Max P® rigid clamp, designed to deliver maximum operational security.
The Coromant Capto tool holders for the T-Max P® benefit from precision over and under coolant, meaning coolant is delivered to both the rake and flank side of the tool. This feature is designed to reduce its operating temperature.
Because pre-directed precision over coolant can improve chip formation and increase the process window where no operator is needed, this method can be used to improve the efficiency of unmanned machining. This ensures the process can be carried out with greater reliability, which in turn can reduce operator costs.
Integrated under coolant also has the potential to improve tool life by up to 20%. The benefit of under coolant becomes even greater with increased heat generation, improving component costs and reducing tool cost per part.
“Many Sandvik Coromant products benefit from precision coolant,” explains Staffan Lundström, Product Manager at Sandvik Coromant. “We first began to recognize the benefits of implementing coolant around a decade ago, and have introduced it to new and existing products since. As part of this introduction, we offer a complete turning tool solution with both over and under precision coolant.
“The Coromant Capto® tool holders for the T Max P® encompasses Sandvik Coromant’s largest group of turning tools, providing tool holders for the most commonly used turning inserts. With this in mind, we knew it was vital that we introduce coolant to the range, to extend tool life and boost component quality when machining demanding materials.
“Past performance cases have demonstrated a significant increase in tool life once precision coolant is implemented. For example, one customer saw a 180% increase in productivity and a 263% increase in tool life when switching from a solution with flooded coolant, a more conventional form of cooling, to tools optimized with our precision coolant solution.
“With this area of our offering being such a machining staple, we expect many more customers to be able to enjoy these benefits.”
To learn more about the advantages of coolant, visit the Sandvik Coromant website. You can learn more about the T Max P® turning insert, and the Coromant Capto® tool holders, here.