A new dimension of highly productive complete machining
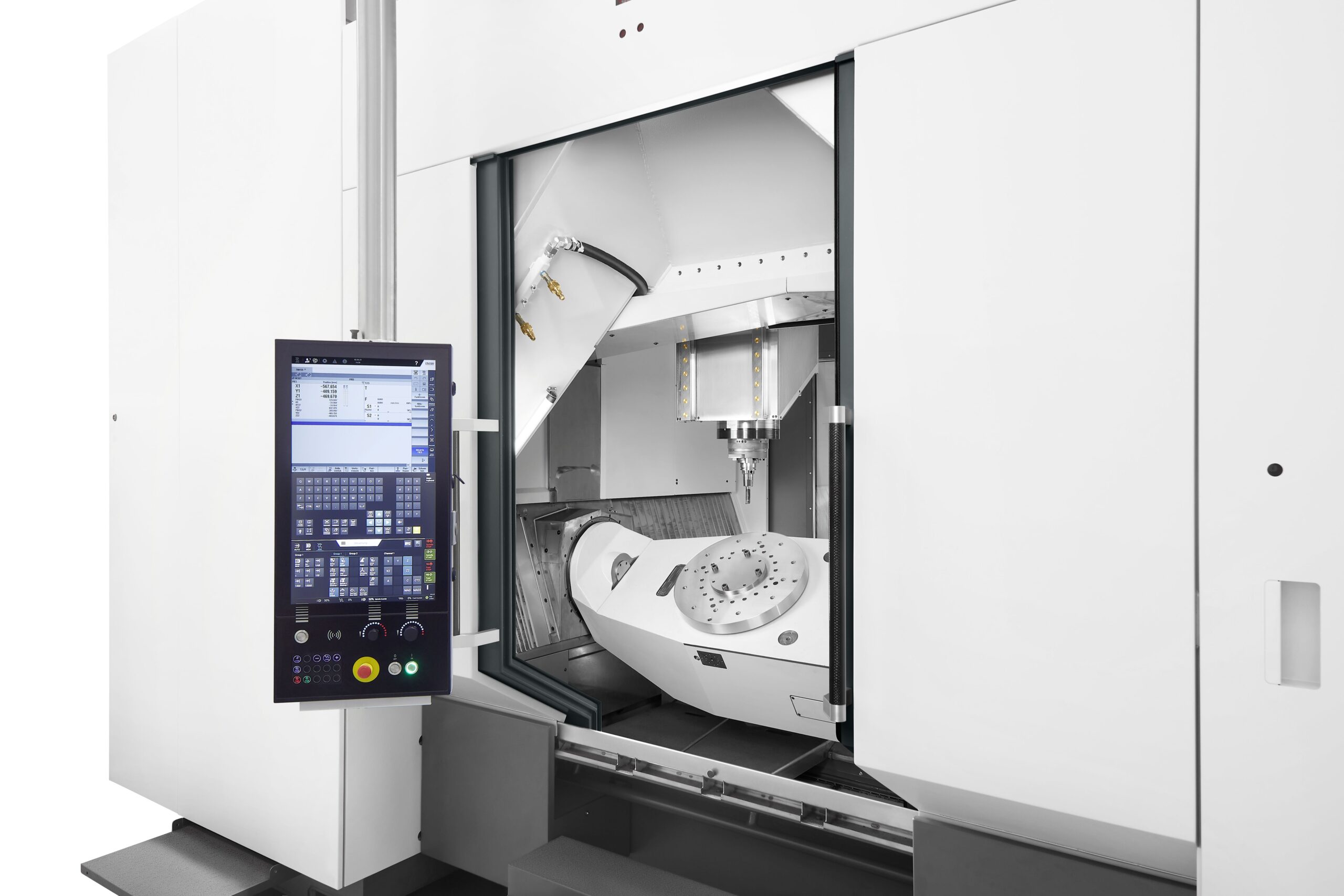
The new CHIRON DZ 28 and its spindle clearance of 1,200 mm.
The CHIRON DZ 25 P was already setting a high bar at the EMO 2019 with extremely productive machining of high-volume structural components for the automotive and aviation industry. And now it’s gone one stage bigger with the new CHIRON DZ 28 and its spindle clearance of 1,200 mm.
Changes in the manufacturing processes in the automotive industry and the altered market conditions in the aviation industry are putting new, bigger demands on machining technology. The industries are desperately calling out for machining processes that are both dynamic and precise for the highly productive complete machining of large and complex structural components. This requires machining centers that can be flexibly configured down to the last detail. The new 28 Series, with its spindle clearance of 1,200 mm, is the CHIRON Group’s resounding answer to the current market demands and it celebrated its world premiere at the OPEN HOUSE ONLINE 2021.
Maximum efficiency machining large and complex parts
There are two versions of the twin-spindle machining center available: The DZ 28 P five-axis with pallet changer for high quantities and short cycle times, and the DZ 28 S five axis for direct loading.
An unbeatable advantage, especially with large workpieces, is that operating and loading take place on separate sides. This means the machine operator has optimum access to the working area and a good view of the machining process. With this highly dynamic machining center, you also benefit from a compact layout, and its fully independent Z and X-direction spindles. It can also be automated via robot or gantry. The machining center is operated via TouchLine, the established operating system from the SmartLine portfolio. A large panel allows easy monitoring of the machine condition at all times. As with all of the CHIRON Group’s new series, the 28 Series is prepared for the integration of all SmartLine modules. For example, this includes Protect Line for preventive protection against machine crashes and Condition Line for automatic condition monitoring of relevant machine components.
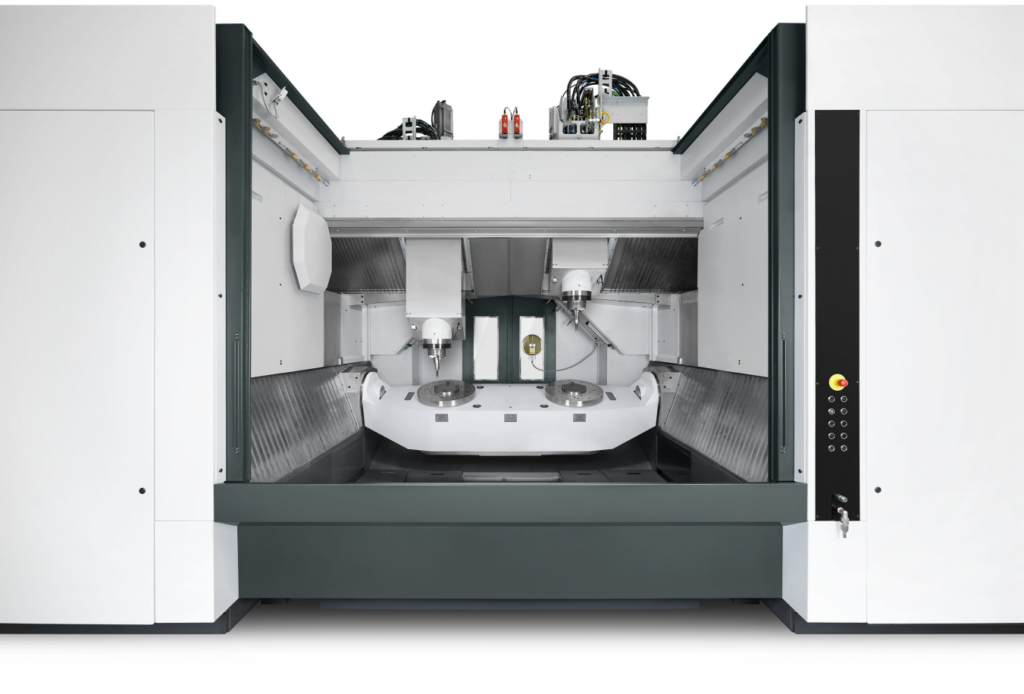
The future concept for e-mobility and aviation
With its spindle clearance of 1,200 mm, the DZ 28 is ideal for demanding five-axis machining in the automotive and aviation industries. It enables the highly productive and top-quality manufacture of side beams, battery cases, and housings for the power electronics, as well as blades, blisks, and impellers for engine and turbine building. High axis acceleration and rapid traversing ensure dynamic machining as never before seen with workpiece dimensions of this size. The portal construction, rigid machine bed, and active component cooling enable the required degree of precision on the workpiece. Another advantage is the tool magazine with space for up to 60 tools, making the machine easy to set up.
“With the 28 Series, we are addressing new customers and workpieces. Whereas previously, only single-spindle manufacturing could be used for components of this size, the new DZ 28 twin-spindle machines have considerably shorter cycle times – while also producing the best part quality.”
Kristoffer Siegmann
Head of Global Account Management Automotive at CHIRON Group
About the CHIRON Group
The CHIRON Group, headquartered in Tuttlingen, is a global company specializing in CNC vertical milling and mill-turn machining centers, as well as turnkey manufacturing solutions. The Group has a global presence, with production and development sites, sales and service subsidiaries, and sales agencies worldwide. Around two-thirds of machines and solutions that are sold are exported. Key customer sectors are the automotive, mechanical engineering, medicine, precision engineering, aerospace industries, and tool production.
The CHIRON Group is the proprietor of the brands CHIRON, STAMA, and FACTORY5, associated with new machines, as well as the retrofit brand CMS. The key feature of all the brands is precise, productive, and flexible machining. CHIRON has a reputation for optimum dynamics. STAMA focuses on stability and heavy machining. FACTORY5 machining centers are ideally suited for high-speed machining of micro technical components. CMS provides completely overhauled machines from the Group, including related services. With products and solutions for additive manufacturing, the CHIRON Group supplements its core competencies.