Cerin SpA, a pioneering Italian cutting tool manufacturer is pushing what is possible, exploring exotic nickel alloys to set the future of tool technology
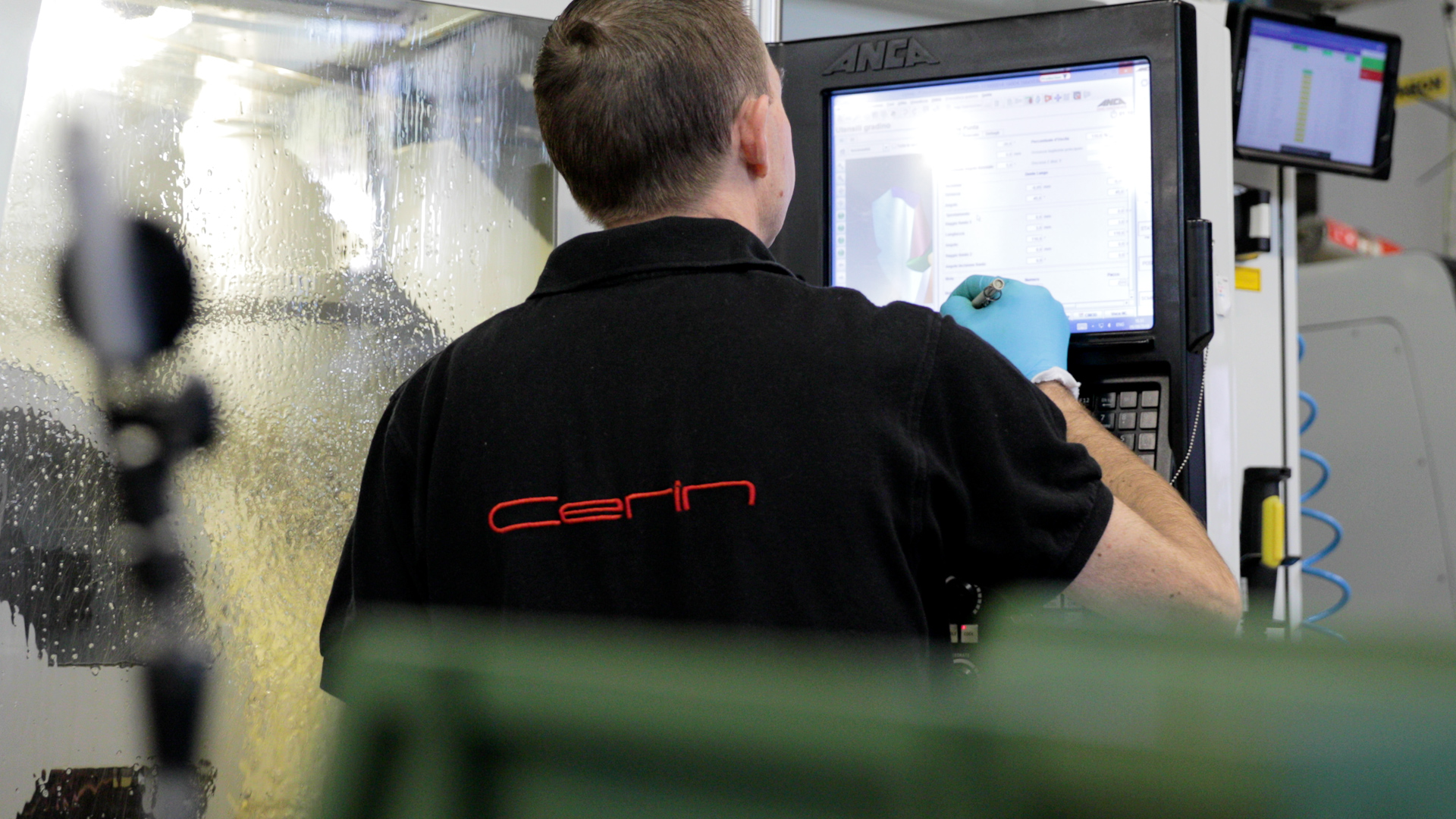
Cerin invested in ANCA technology to take on these challenges and succeed – achieving precision, repeatability, and stability in their grinding
Ivan Cuscov, Plant Director started at Cerin SpA ten years ago as a mechanical engineer and today is responsible for production. Ivan said, “Cerin was founded in 1971 by Mr Cerin and my father joined the company a few years later. We were one of the first Italian companies to work with solid carbide and today serve many industries, from aerospace to construction, shipbuilding, energy and automotive.”
“Half our sales are in Italy and the other half abroad, mainly exporting to Germany but also Russia and Japan, China, England. Our customers choose to work with us because we manufacture a good product. If you ask our customers to say something about CERIN, they will only say, ‘A Cerin tool is a good tool.’ And that’s what I think is what makes us successful.”
“From the beginning we never worked with high speed steel as we had a feeling that solid carbide was the technology of the future and so we tried to make the biggest step possible into the future. It was very challenging at the time as there was limited knowledge on how to use solid carbide. Many people in the industry didn’t know of diamond wheels and thought of diamond as a jewel and not a grinding material!”
“We were a pioneer with many challenges working in unknown territories but on reflection I would say that taking on this challenge was key to our success.”
Cerin continues to invest in their pioneering culture to stay ahead of technology change
“At Cerin we try our best to understand our customers production requirements. If the customer has a problem, we look at their machining process – how the machine works, how the workpiece is placed on the machine, and what are the critical issues, vibration and so on. We have even built a Development Centre to try new materials and new machine technology.”
“Currently we are looking into the exotic nickel alloys or otherwise called high temperature alloys – which are still niche materials, but we think it’s important to understand given the increasing requirement for energy efficient engine performance. For these applications, high performance requires higher thermal mechanical properties and that is driving tool technology.”
“These materials are particularly critical mainly for heat generation and elastic to plastic transition. Cutting those materials requires specific coating and sometimes a specific combination between solid carbide coatings and dedicated geometries.”
Tool makers must consider the entire development life cycle
“A good tool is the combination of elements. The right geometry and the combination between carbide and coating. Developing a new tool might require a few weeks to many months. The first technical work is designing and testing a basic tool of a certain length and diameter, which fulfills the initial targets. After that you need to organise the whole commercial offer, extend the tests to the rest of the product family, and of course create the stock availability.”
“Over the weekend we mainly produce standard tools and in some areas with unmanned shifts which helps us contain costs, increasing our capacity. Our operators create optimal production conditions, looking at correct machine and grinding wheel set ups. Our attention to detail when setting up processes mean we can guarantee quality.”
“Our quality control department is responsible for checking tools during and after production. We have the complete traceability of our production batches and at any time can retrieve design information, even look at the raw materials.”
ANCA technology offers precision, repeatability, and stability – all essential for lights out manufacturing
“In our machine centre we have a MX7, MX7 Linear, FX7 Linear, GX7, TX7 and even a TG7. At the moment we are mainly using ANCA machines for standard and cylindrical endmills and we keep the FX7 and one MX7 linear for mixed production of endmills and drills.”
“Precision, repeatability and stability are two advantages of using ANCA machines and over the years we have found ANCA machines to be thermally stable with a wide range of technology on offer. A stable grinding machine is very important for unmanned shifts to keep tolerances and tool dimensions under control. In facts repeatability means that we have the grinding process under control and can be confident with the quality of the end product we deliver to our customers.”
“iGrind is a very good software package mainly because of flexibility and because it allows you to do many different things easily. iGrind is great for cylindrical grinding to profile tools and especially with tool segments where you can split the tool operations as much as you want. We also use ANCA’s
ToolDraft in combination with AutoCAD.“
“We have been recently using iView with a camera for profile tools and it looks promising because it is a good way to control the tolerance of a complex tool all along the profile. If a profile is being controlled at a single point it is too difficult if you are trying to keep a whole profile within a certain tolerance to a few microns. For that you need a specific device and iView is very interesting.”
“Our operators are happy with the Wheel Probe which references the grinding wheel directly on the machine. The benefit using the probe is that you don’t need to waste any time with an external preset and can make your measurements directly on the machine. And you don’t need to mount and dismount the wheel before and after measuring because that of course might change the basic reference a little bit. So you’re going to measure the wheel in the same place where the wheel will work.”
ANCA website: www.anca.com
ANCA is a market leading manufacturer of CNC grinding machines. It was founded in 1974 in Melbourne, Australia where the company still has its global headquarters. ANCA has offices in the UK, Germany, China, Thailand, India, Japan, Brazil and the USA as well as a comprehensive network of representatives and agents worldwide. ANCA CNC grinders are used for manufacturing.
ANCA CNC grinders are used for manufacturing precision cutting tools and components across a diverse range of competitive industries including cutting tool manufacture, automotive, aerospace, electronics and medical.