Pioneering Precision
Rajesh Nath, Managing Director, VDMA India, shares insights on the transformative technologies, sustainable practices, and workforce evolution shaping the future of the metal-cutting industry.
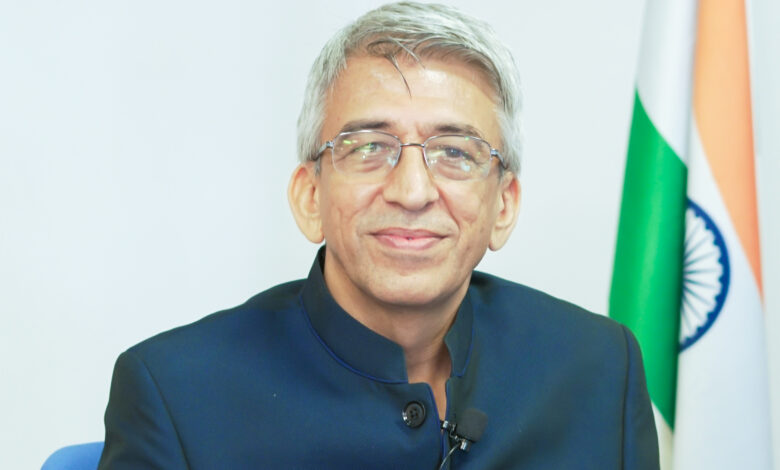
1 ) What recent advancements in metal-cutting technology have had the most transformative impact on efficiency and precision?
Recent advancements in metal-cutting technology have significantly boosted efficiency and precision. The evolution of multi-axis CNC machining, particularly 5-axis systems, allows for more complex cuts in fewer setups, enhancing both accuracy and speed. Additive manufacturing (3D printing) is also playing a crucial role by enabling the creation of intricate geometries that are difficult with traditional methods, while reducing material waste. Laser cutting technology has advanced with higher-powered lasers, offering ultra-precise cuts with minimal thermal distortion and improved energy efficiency. Additionally, automation and AI-driven process optimization are improving consistency by using real-time data to adjust cutting parameters dynamically. New tool materials and coatings, such as advanced ceramics and diamond-like carbon coatings, extend tool life and reduce wear. These innovations collectively improve productivity, reduce operational costs, and enhance the precision required for modern manufacturing needs.
2 ) How is the industry adapting to sustainable manufacturing practices, and what specific initiatives are helping to reduce environmental impact?
The metal-cutting industry is increasingly adopting sustainable manufacturing practices to reduce its environmental impact. Key initiatives include the use of energy-efficient technologies, such as hybrid machines and low-power CNC systems, which minimize electricity consumption. Manufacturers are also focusing on waste reduction through techniques like dry machining and minimum quantity lubrication (MQL), which reduce the need for cutting fluids and improve efficiency. Recycling and reusing materials, such as reclaiming scrap metal, further lowers waste. Sustainable tooling materials are gaining traction, with innovations in coatings and tool life extension reducing the frequency of tool replacements. Additionally, digitalization and smart manufacturing help optimize production processes, minimizing waste and energy use. By integrating these practices, the industry is not only cutting costs but also contributing to a more sustainable, eco-friendly manufacturing environment. These efforts are essential in meeting global sustainability goals while remaining competitive.
3 ) With digitalization reshaping manufacturing, what new skills are essential for today’s workforce, and how is the industry addressing the skills gap?
As digitalization reshapes the manufacturing landscape, the workforce must develop new skills to keep pace with advanced technologies. Key skills include data analytics, machine learning, and programming for managing and interpreting data from connected systems. Proficiency in operating smart machines and robotics is also crucial, as automation and AI-driven processes become more prevalent. Additionally, knowledge of additive manufacturing and digital twin technologies is essential for understanding virtual modeling and simulation.
To address the skills gap, the industry is investing in training and development programs, including partnerships with technical colleges and universities. Companies are offering on-the-job training to upskill existing workers and apprenticeships to bring in younger talent. Many organizations are also turning to online courses and virtual learning platforms to provide flexible, accessible education. These efforts ensure the workforce is equipped to handle the evolving demands of modern manufacturing.
4 ) What trends are driving the current demand for metal-cutting solutions, and how do you foresee the industry adapting to these trends?
The demand for metal-cutting solutions is being driven by several key trends. Industry 4.0 and the rise of digitalization are leading to increased automation and the integration of smart manufacturing systems, which require highly precise and efficient metal-cutting technologies. The growing demand for lightweight materials in sectors like aerospace and automotive, driven by the need for fuel efficiency and performance, is pushing for advanced metal-cutting solutions that can handle complex alloys and composites. Additionally, the shift towards sustainability is encouraging the adoption of energy-efficient, waste-reducing technologies.
To adapt, the industry is embracing multi-axis CNC machines, advanced cutting tools, and AI-driven process optimization to meet the increasing demand for precision and efficiency. The focus on sustainable practices will drive further innovation in eco-friendly cutting methods and the recycling of materials, helping manufacturers meet both performance and environmental goals.
5) What do you view as the most significant challenges facing the metal-cutting industry today, and what steps is your organization taking to stay competitive?
The metal-cutting industry faces several significant challenges today, including rising material costs, supply chain disruptions, and the rapid pace of technological change. As manufacturers increasingly rely on high-performance materials and advanced cutting tools, fluctuating raw material prices can affect cost stability. Additionally, the need for constant technological upgrades can be resource-intensive, requiring significant investment in both equipment and workforce training.
To stay competitive, our organization is focusing on continuous innovation and digital transformation. We are investing in AI and machine learning to optimize production processes, ensuring higher precision and reduced downtime. We’re also committed to sustainability, adopting energy-efficient machines and reducing waste through better material utilization. Furthermore, we are enhancing our workforce’s capabilities by offering training programs and partnerships with universities to bridge the skills gap. By embracing these strategies, we are better positioned to tackle challenges and meet evolving market demands.
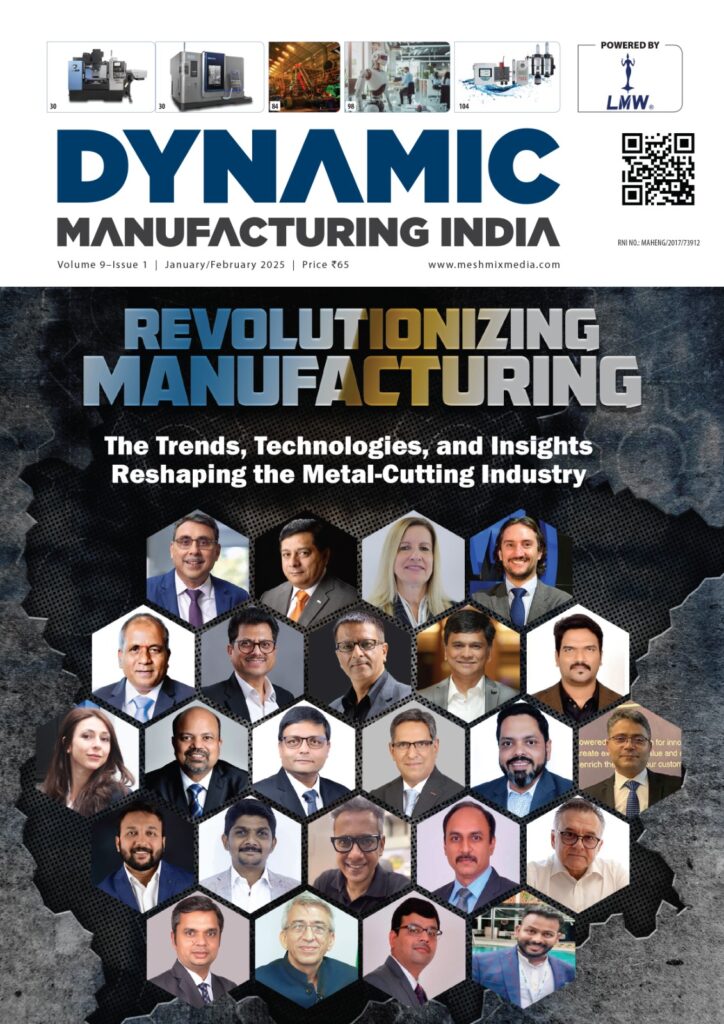
E copy of Magazine – https://www.machineinsider.com/dynamic-manufacturing-india-jan-feb-2025-edition/