Aluminum alloys help solve the weight dilemma
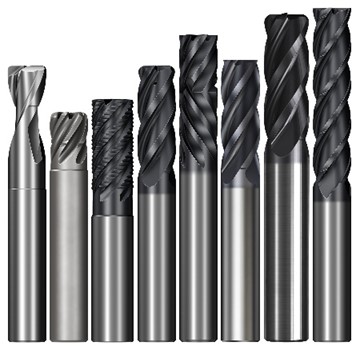
Sustainably improving aluminum machining in the automotive industry with the right tools
The automotive industry faces a dilemma — to save fuel, vehicles must become lighter. At the same time, new components and technologies make them progressively heavier. The solution — components from aluminum. Tool manufacturer Sandvik Coromant shows how special milling cutter designs can be part of the solution.
A ten percent reduction in vehicle weight can lead to fuel savings of six to eight percent. That is why manufacturers are increasingly turning to aluminum, one of the most important materials for lightweight construction. But aluminum alloys require complex machining with complex and cost-intensive processes and various tools. In addition to very time-consuming tool setups, inferior surface finishes, burr formation, and inconsistent tool wear are not uncommon. So how can automotive manufacturers achieve shorter lead times, better quality, and higher savings?
Two-in-one solution
For precise, trouble-free, and burr-free milling, Sandvik Coromant offers several patented milling cutter designs, including the M5C90 — the face milling tool was developed for roughing and finishing cylinder heads and blocks as well as solid aluminum parts with long milling operations. It is capable of performing the entire machining process, from roughing to finishing, in just one operation — in many cases with an axial depth of cut of up to four millimeters. This way, tool life can be increased fivefold in some cases while cycle time is reduced by 200 percent.
A key feature of the M5 cutter series is its step technology — the polycrystalline diamond (PCD) inserts are arranged in a spiral and staggered vertically to remove material from the workpiece both axially and radially. The last tooth offers a wiper geometry in order to achieve high-quality, flat surfaces. In addition, the fixed position of the wiper cutting edge eliminates the need for time-consuming setups. The M5 series includes also the M5Q90, a tangential milling concept for roughing, the highly stable M5R90 face and shoulder milling cutter, the M5F90, a combination milling cutter for roughing and finishing in smaller dimensions, and the M5B90 face milling cutter concept for fine finishing.
With the M610, the Swedish company also offers a milling cutter solution for the finishing of bimetals or material composites made of aluminum and gray cast iron. The concept, which delivers high feed rates without chipping, burr formation, or surface scratches, also requires no setup or adjustment of the inserts.
In addition, to insert solutions, solid carbide tools are available for both drilling, milling, and threading. The complete CoroMill® Plura range of solid carbide end mills includes tools for roughing to finishing and thread milling.
Because aluminum alloys help solve the weight dilemma in the automotive industry, Sandvik Coromant’s complete range of tools for aluminum machining enables companies to successfully meet the demanding requirements in this field.
Sandvik Coromant
Part of global industrial engineering group Sandvik, Sandvik Coromant is at the forefront of manufacturing tools, machining solutions, and knowledge that drive industry standards and innovations demanded by the metalworking industry now and into the next industrial era. Educational support, extensive R&D investment, and strong customer partnerships ensure the development of machining technologies that change, lead and drive the future of manufacturing. Sandvik Coromant owns over 3100 patents worldwide, employs over 7,900 staff, and is represented in 150 countries.
For more information visit www.sandvik.coromant.com