Back In Action: An MCMT Special
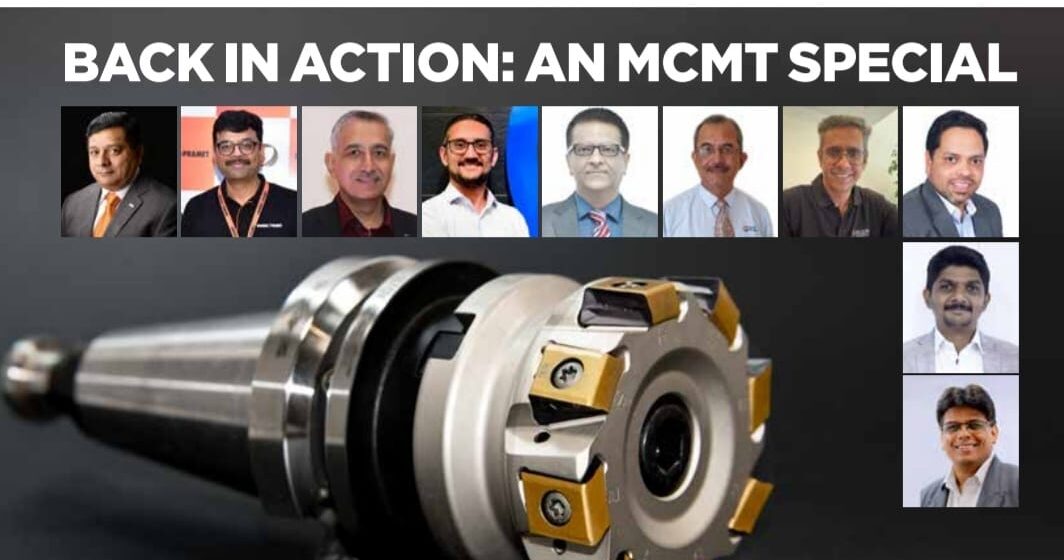
India’s metal-cutting machine tools sector is one of the biggest markets for the global USD 76-B MCMT industry. Local and international players have their hands full catching up with the post-pandemic pent-up demand – a trend reflected in the mega-buzz around IMTEX 2023. In this issue, we feature actionable insights from industry leaders on top growth opportunities and their offerings for this year’s biggest industry event
The global Metal Cutting Machine Tools (MCMT) market size was valued at USD 76 billion in 2022, projected to grow at a CAGR of 4.8 percent in the next five years, according to a recent Fortune Business Insights report. India is among the world’s biggest metal-cutting machine tools markets, with sectors like automotive, general engineering, energy, and aerospace being the major demand drivers. The industry faced one of its biggest challenges in recent history, with more than two years of uncertain growth, affected by global demand headwinds. In recent months, the sector has started to witness a level of activity and demand close to the pre-pandemic levels and that excitement is being seen around this year’s IMTEX, which is drawing exhibitors and visitors from India and overseas in large numbers. Our current issue focuses on the operations and growth plans of companies that are participating in the exhibition. Industry thought leaders who shared insights with us included Gautam K. Ahuja, the CEO & Managing Director of Gühring India; Rajesh Ghashi, Managing Director, CHIRON INDIA Machine Tools Pvt. Ltd; Dhiruj Sarda, Director, East Coast Magnets Private Limited; Sharad Kulkarni, Managing Director, Dormer Pramet India; Manoj K Sundaram, Head Business Development, Carl Zeiss India; Arun Upanal, Director, Upanal – CNC Pvt Ltd; Tridib Majumder, Managing Director, Quaker Houghton India, and Vineet Seth, Managing Director, Mastercam India. Presenting, their views on the sector, the challenges, demand drivers, and the offerings and the product launches that they plan to showcase at IMTEX 2023.
Q1. Can you share your company’s top MCMT (metal-cutting machine tools) offerings in terms of sales and demand?
Gautam K. Ahuja, the CEO & Managing Director of Gühring India: Our SuperLine range of tools offers the customer the optimum price-performance ratio. These tools can be used on any material and are economically priced.
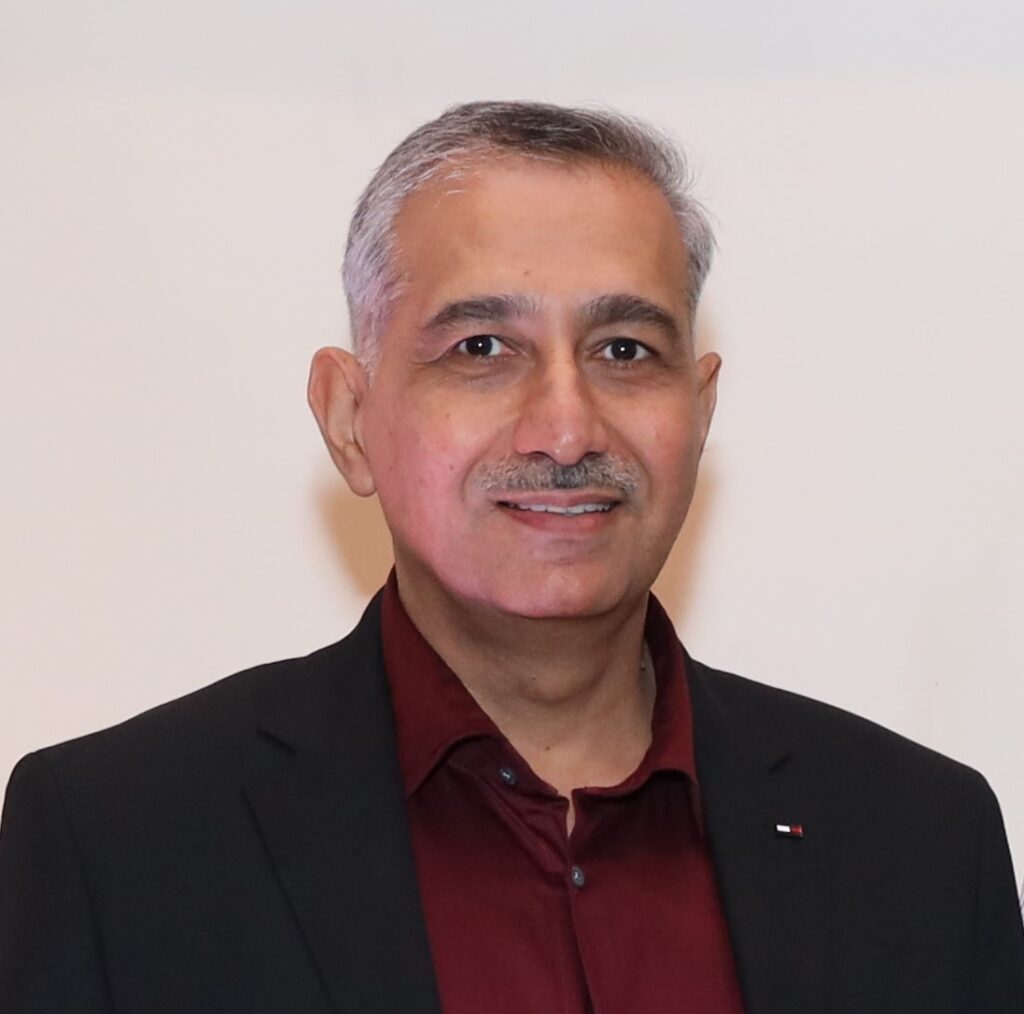
The high-performance range of tools like our RF 100 Diver, and HR 500 high feed reamers offer the customers multiple advantages of faster machining, better quality, increased tool life, and productivity.
Rajesh Ghashi, Managing Director, CHIRON INDIA Machine Tools Pvt. Ltd: The CHIRON Group is the proprietor of the CHIRON, STAMA, and FACTORY5 brands for new machines, as well as the automation brand GREIDENWEIS, CMS for refurbishment, and HSTEC for motor spindles and fixtures. CHIRON machining centers are renowned for their highly dynamic design and their precision.
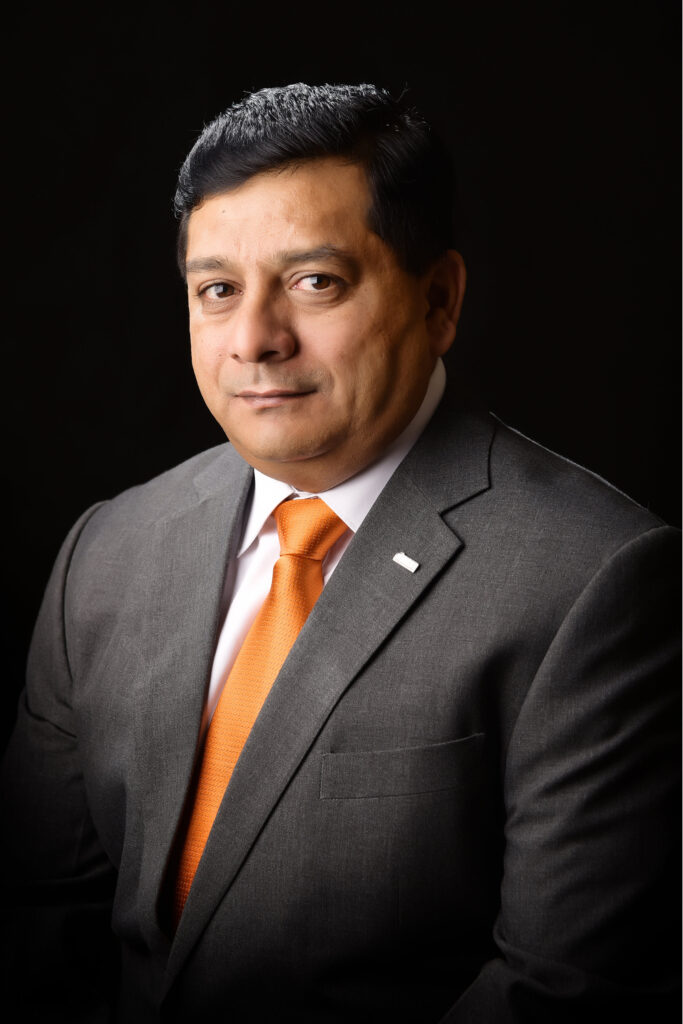
The focus of STAMA is on stability and complete machining, while FACTORY5 expert area is high-speed machining of micro-technical components. GREIDENWEIS is a system partner for custom, end-to-end automation solutions, and CMS provides completely refurbished machines from the Group. HSTEC specializes in the development, manufacture, and repair of high-speed motor spindles and fixtures. The final core area of expertise in the CHIRON Group is in additive manufacturing products and solutions.
Dhiruj Sarda, Director, East Coast Magnets Private Limited: The demand for our magnetic work holding solutions – magnetic chucks is the highest. We have our own patented technologies which are incorporated in the magnetic chucks for machining applications. With the increase in demand for process optimization and reduction of idle spindle time during machining, efficient work holding is where we come in.
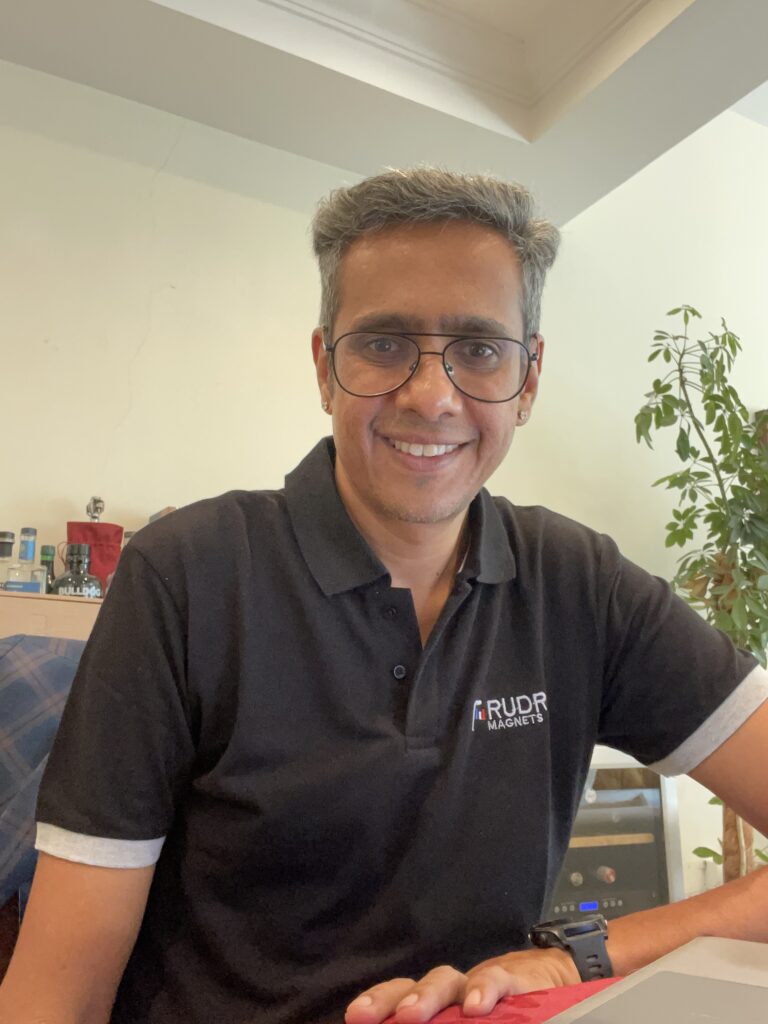
For component machining, replacing conventional clamping methods such as mechanical, hydraulic, or pneumatic with our magnetic chucks, the number of components being machined is increased thereby increasing productivity and better utilization of the machine space. We see an increased requirement for smart clamping solutions and with our patented magnetic field detection technology we are in the right place to provide such solutions.
Rizwan Khan, Sales Manager – India, SupplyPoint: We are offering a dynamic solution to the Metal Cutting industry, at SupplyPoint we offer a range of solutions for “Store Automation” that includes bulk stock with Asset management for important spares as well, “Intelligent Vending Machines” for point of use on the shop floors to have better control on consumables. We have also seen increasing demand for “Traceability and accountability” to identify the stock, location, and possession of items on the shop floor; SupplyPoint has patented technology of Progressive drawers for the same.
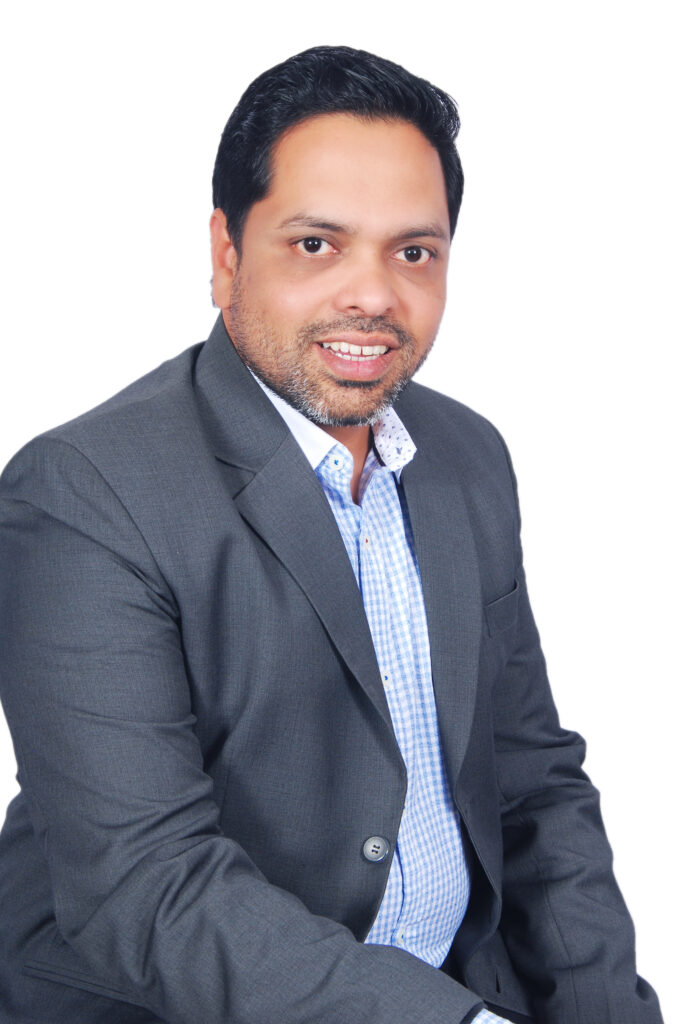
Manoj K Sundaram, Head Business Development, Carl Zeiss India: The market for Electric Vehicles in India has taken off, with annual sales of passenger cars, and two- and three-wheelers growing in multiples, as per recent market reports. The Zeiss Group’s quality and metrology solutions for the various stages of NEV (New Energy Vehicles), especially electric vehicles are globally well known. Can you give us a deeper view of your company’s solutions for the EV industry, particularly for aspects like battery safety, electric motor design, power electronics, and transmission?
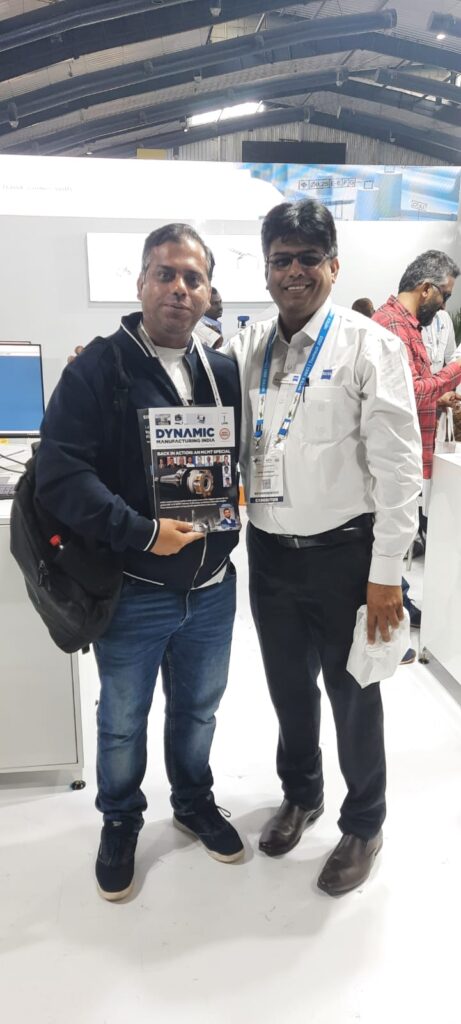
Quality control: Carl Zeiss’s metrology equipment can be used to measure and analyze the precision and integrity of various components used in electric vehicles, such as battery cells, Welded BIW, Electric motors, Transmission parts, and Electronics.
Research and development: We have fundamental tools for use in the research and development of advanced battery chemistries and advanced materials used in EV components. As an example, the performance of batteries changes over their lifetime, and it’s critical to understand these longitudinal aging effects. Under a microscope, one can observe that charging and discharging creates chemical and structural changes that alter the electrode materials. Repeated swelling and contracting of the battery leads to crack propagation, void evolution, loss of mechanical stability and electrical connectivity, and thus capacity fading or failure of the cell. ZEISS electron microscopy allows for microscale electrical property mapping, which makes it possible to create a “conductivity map” of the active battery materials.
Transmission parts which include Housings, Gears, and Shafts in E vehicles need an inspection in production processes. High engine speeds of up to 20,000 rpm mean that the gearwheels in the transmission must meet very small geometric tolerances. These speeds are also demanding for the shape and position tolerances of the rotor and gear shafts, especially where the bearings and gears are located. Having the electric motor and gearbox in the same housing requires a very complex, yet lightweight design, which involves precise machining steps on the casted housing. The slightest deviations in the shape, size, position, or surface texture of these components can impact the functionality and safety of the powertrain. The e-motor is virtually silent compared to combustion engines. Therefore it’s important to reduce any other noise created by shape, location, and size deviations in the components (shaft, bearing, gear), as well as surface irregularities. Roughness and waviness parameters also play an important role. ZEISS roughness and topography sensors collect all the data – on ZEISS coordinate measurement machines and standalone high-precision systems.
Moving to E motors involves the precise production and assembly of the hairpins and stator, as well as the manufacture of the stacks in the stator and rotor. An important change is that current-carrying conductors in the stator are no longer wound from many thin wires, but bent from solid copper wires, plugged together, and welded. While this bending action is fully automated, it poses quality assurance challenges to measuring the pin shape and isolation lacquer thickness due to the flexible structure of the pins. Eventually, these hairpins need to fit into the exact grooves punched or cut into the stator stack sheets. Such high-precision assemblies require down-to-the-micrometer accuracy – and this is where ZEISS excels. The design of a hairpin is not simply defined by a CAD model but developed in many loops through the configuration of the bending parameters. It’s necessary to scan and produce CAD models to evaluate finished hairpins in relation to a master pin. Fringe projection and laser triangulation of high-resolution point clouds of the hairpins. ZEISS Reverse Engineering software can quickly turn these into high-quality CAD models
Tridib Majumder, Managing Director, Quaker Houghton India: Our metalworking product line includes among others water-soluble oils and neat cutting oils, these are the largest group of products in our portfolio as well as demand from customers. There are a number of factors that drive this demand: the quality of our products, and our customer intimacy model that includes excellent technical and after-sales service, another big enabler are recommendations and approvals by various Machine Tool Builders ( MTBs ). We have a large number of such endorsements from MTBs, this is the testimony of the trust and confidence in our products by customers as well as the MTBs.
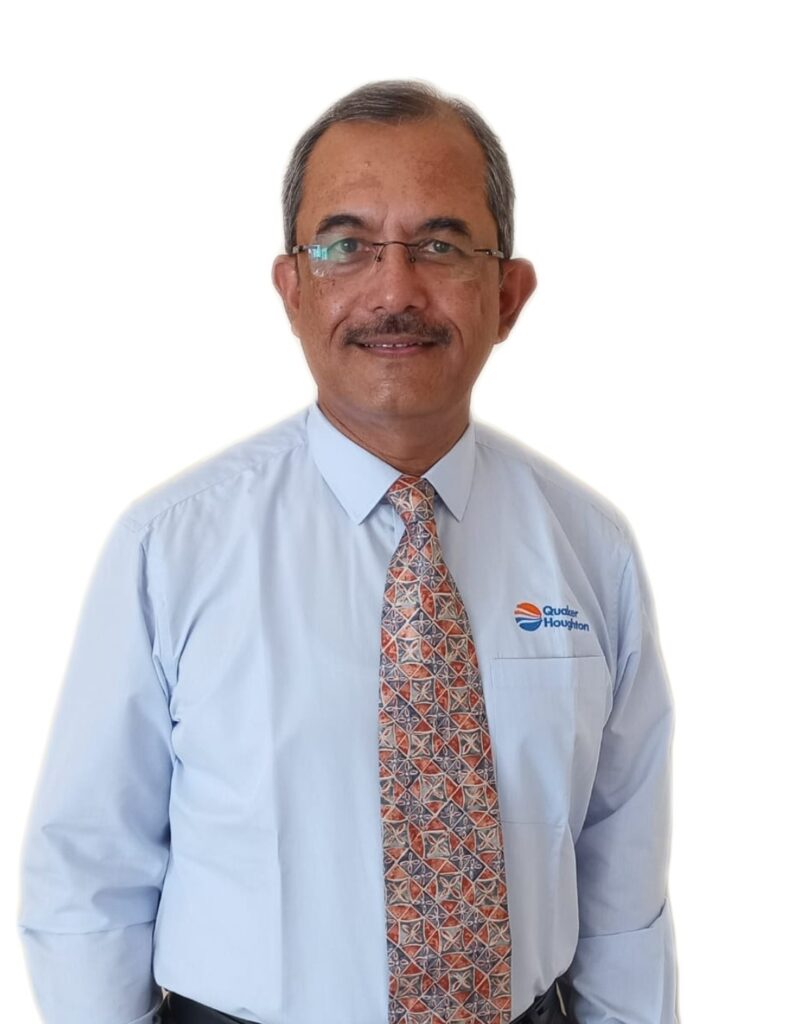
We offer the complete solution to our customers and we proudly say, “ if it’s made of metal, if it’s rolled, cut, drawn or cast, Quaker Houghton is there with a solution, optimising processes, reducing costs, advancing safety and sustainability and driving progress”.
Our other product offerings in Metalworking such as Rust Preventives, Cleaners, Forging Fluids, Fire Resisting Hydraulic Fluids, Die Casting Fluids, and Heat Treatment support our customers with all their process fluid requirements.
“We take our customers’ challenges as our own, bringing the right combination of science, engineering, and business savvy so they can meet the future fully confident that their operations will run more efficiently, even more effectively whatever comes next”.
Sharad Kulkarni, Managing Director, Dormer Pramet India: Dormer Pramet’s purpose is “we care for manufacturing” and the brand promise is being simply reliable. In line with the same, we have got very strong products in the area of indexable inserts, solid carbide round tools, and HSS products. Many of these products have achieved leadership in the mid-market product categories globally and in India. Overall, our objective is to make sure that we improve the competitiveness of the manufacturing industry through these solutions.
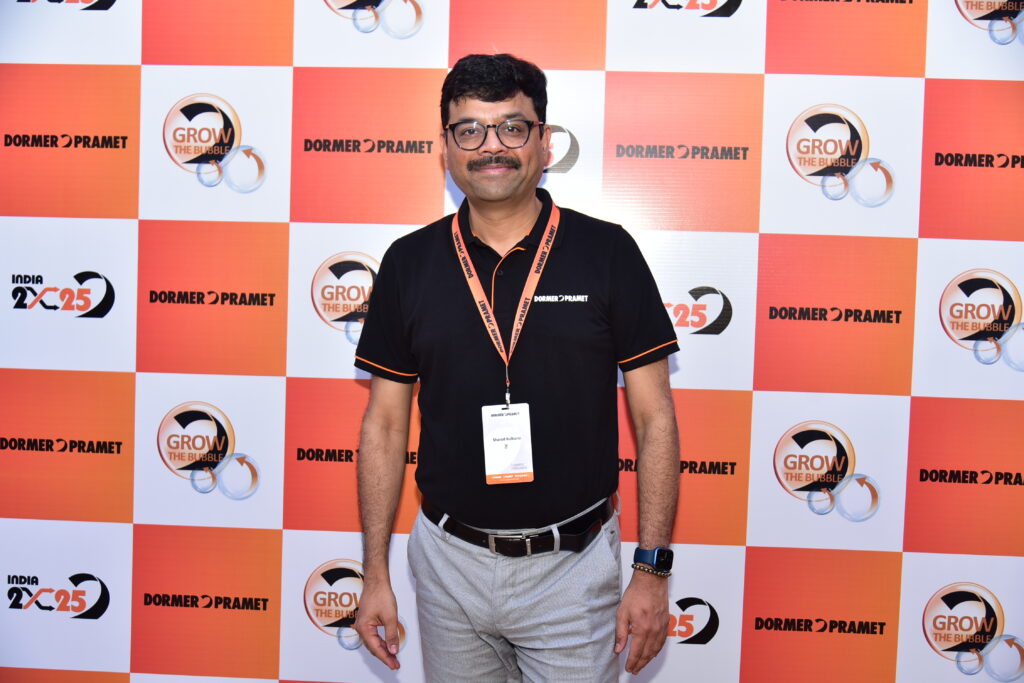
Arun Upanal, Director, Upanal – CNC Pvt Ltd: Manufacturing is the backbone of any industry and we supply machinery with lathe test technologies available in the market which help our manufacturing industry to cater to the market demands in producing a final quality product at par to global standards for better living of the end consumers.
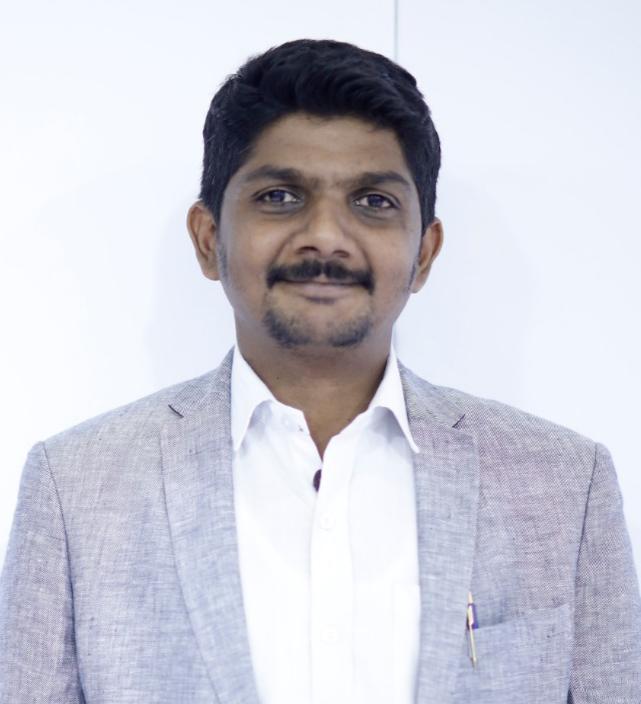
Q2: Which are the top three metal-cutting technologies for which you see the biggest demand and growth currently and going forward? Can you briefly share with us the reasons?
Rajesh Ghashi, CHIRON INDIA Machine Tools Pvt. Ltd: The demand for CNC Turning Machines, Machining Centres, and Grinding machines will continue to drive the demand and growth of the industry as these are some core requirements. Now with newer technologies, we see a good opportunity, demand, and growth for additive manufacturing. This technology has been rapidly adopted in various applications like quick product development, MRO services, aerospace components manufacturing, etc.
Dhiruj Sarda, East Coast Magnets Private Limited: Material removal per se should not be looked at the conventional divide of turning/milling/drilling/ grinding, etc. – the world is fast moving to a combination of all such operations.
The demand for components to be made faster and more energy efficient is where the industry is moving. Definitely, we feel the demand and growth will be more towards machines that are more versatile and more independent from operator involvement. It can be any kind of machine but the need shall be for it to be more responsive and dynamic in nature.
The need for EMD/VMC/ HMC/ Turning machine/Turnmill/ Millturn, etc. shall all be there as the demand for manufacturing is growing in India and other parts of the world. The trend to have manufacturing outside of China is definitely helping to push demand for machine tools in the rest of the world. The advantage now is that instead of just going for basic machines which are still going to be needed the requirement for more advanced machines with the same number of axis also increases. This is good for accessory manufacturers like us as we get the opportunity to further enhance the operational and utilization capability of the machines.
Vineet Seth, Managing Director, Mastercam India: CNC Turning, CNC Milling and CNC Turn-Mill are the top areas of metal cutting growth, seen in recent times. The uptake in multi-tasking machines also seems to be growing rapidly in the past few years, notwithstanding the gap from COVID. Maximum utilization per sqft of real estate, to avoid frequent loading & unloading as well as to reduce the number of fixtures and setup are the main reasons manufacturers are looking towards multitasking machines. The availability of trained personnel and the advancements in machine tools are also contributing factors towards this growth.
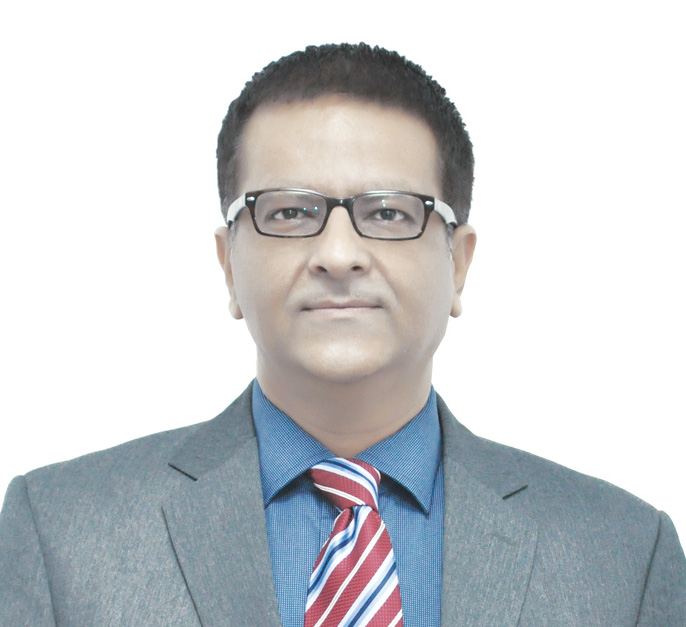
In some industrialized areas, Multi-Axis machining is also growing at a fast pace, considering that these regions are predominantly focused on Aerospace and Medical manufacturing.
Gautam K. Ahuja, Gühring India: Milling will be an operation which will be focussed as it is a critical operation for material removal for any type of industry like Die & Mould, Aerospace, EV / Automotive.
Machining strategies, adaptive self-correcting technologies will be increasingly used in machining.
Sharad Kulkarni, Dormer Pramet: As the manufacturing industry becomes more competitive, non-value activities in the process become the focus and efforts are made to eliminate them. Examples like avoiding multiple set-ups, eliminating of non-cutting time, online quality measurements and reducing maintenance help to improve productivity and in turn competitiveness. In combination with high-performance cutting tools, there is a good possibility of improving manufacturing economics. These ideas cut across different application areas like turning, milling, EDM, gear cutting, etc.
Arun Upanal, Upanal – CNC Pvt Ltd: Metal cutting technologies has shaped itself with decades of experience and continuous innovation and advanced technology. At present we see good demand in the fields of automation, 5-axis machines and Industry 4.0 technologies. Yes, 5-axis machines are gaining interest in the market like aerospace sectors, as many big players are looking at India as a manufacturing hub for Aerospace and the capabilities, we have showcased in the past decade are drawing more investments and opportunities for Indian companies to supply most critical components with advanced machining facilities.
Q3: Which are the top customer segments that are the biggest drivers of sales and demand currently? Can you share with us the top demand trends you see in the market?
Rajesh Ghashi, Managing Director, CHIRON INDIA Machine Tools Pvt. Ltd: Automotive industry remains the main driver of the machine tool industry however we are seeing a good demand coming now from medical and precision component manufacturing. Aerospace industry is also showing a greater demand.
Vineet Seth, Mastercam India: Automotive, Aerospace and Medical machining are the biggest customer segments for us, with the Oil & Gas companies in India and the Middle-East being close followers. A combination of Turning and Milling applications are in top demand across these domains. While the Die-Mould market is shrinking in terms of growth rate, it still continues to drive advanced manufacturing across our region.
Dhiruj Sarda, East Coast Magnets Private Limited: For our work holding products the biggest demand is coming from the Die and Mold industry, followed by the railway component manufacturers and then by the heavy engineering companies.
With an increase in demand for dies in India, there is an astronomical investment in machines for the same. We see that customers do not hesitate to invest in bigger machines with more features and also invest in better work-holding technologies. The “Make in India” initiative has been the biggest influence on the increase in Domestic Die and Mold Industry. Sometimes stating the obvious that if we help our domestic industry it will become more efficient in time is helping all of us.
The massive investment by the Government in the Railways and Defence sector has trickled down the benefit for us as now more and more companies want to use their machine tools more efficiently without additional manpower and hence our smart work holding technology products are helping them achieve the same.
Renewable Energy is another sector specially the Wind power generation industry where we see a lot of demand for our lifting products. Globally we see a massive investment and expansion in this space.
PEB manufacturing is also another industry which is witnessing a lot of investments due to the increase in demand for warehousing requirements and improvement of logistics industry.
Manoj K Sundaram, Carl Zeiss India: India’s machine tools industry, including the metal cutting and forming sectors, form the backbone of the country’s manufacturing sector. Please share with us your solutions for the sector, such as industrial quality excellence solutions and individual OEM solutions.
Almost all our offering of measurement solutions follows the processes just beyond Metal cutting and Forming machines. Metal cutting shapes the component in a precise way and creates the necessary dimensions which are then ensured by our superior equipment for Dimensional accuracy with Uncertainty and Traceability to meet international standards. This forms the basis of the interchangeability of parts in Global manufacturing. We conform Geometrical parameters on part sizes of few meters using our Large Format CMM’s to analyze sub-micron layers of coating failures in Aerospace parts. Generally we deliver High precision CMM’s like PRISMO, CONTURA, MMZ SF&G equipment comprising of SURFCOM, RONDCOM and Contour and Microscopes like AxioImager, Axiovert to suit the metal cutting industry requirements.
Metal forming solutions refer to the various processes used to shape and form metal into the desired shape or form. These processes include stamping, rolling, forging, and casting, among others. In the automotive industry, metal forming solutions are used to create a wide range of parts and components, such as Body panels, BIW Chasis parts, Dashboard plastic Tools. The prime difference in Cutting and Forming is that the latter has a continuous variation in the shape of the component which demands higher data collection and processing techniques. Hence Laser or Blue Structured light techniques are used in Manual or Automated fashion to collect the shape variation and comparison with CAD model for deviation. The deviation information is then processed for correcting the manufacturing process. Generally we deliver Scanners like ATOS Q , T scan Hawk for Reverse Engineering , Dimensioning and warpage measurements and Automated inspection solutions with multiple sensors for BIW measurements in Car industry.
Tridib Majumder, Quaker Houghton India: For Quaker Houghton, both Metals and Metalworking are important segments and are drivers of our customers’ demand and sales, growth in infrastructure across the country is boosting demand for steel produced by our customers. Quaker Houghton supplies its products in large quantity to the Steel industry and we benefit from this increased demand, initiatives of Atmanirbhar Bharat or Make in India by our respected Prime Minister and the PLI scheme introduced by GOI is driving growth in manufacturing sectors such as automotive and auto component along with other sectors. Demand from automotive customers is growing post the pandemic and is envisaged to touch of pre-pandemic levels of 2018-19.
At the same time, growth in the manufacturing of electronic gadgets in India has opened a new avenue for Indian Industry.
Gautam K. Ahuja, Gühring India: Currently automotive component manufacturing holds the top place in customer segments. Aerospace, defence components manufacturing, micromachining and EV components manufacturing will be the future trends in manufacturing.
Rizwan Khan, Sales Manager – India, SupplyPoint: We have seen a growth in Automotive components manufacturing with Tier-1 and Tier-2 suppliers to OEMs. Also, we see a good growth from non-automotive manufacturing companies from Pumps, Aerospace and Die & Mould in Toy manufacturing. The Indian toys market size reached US$ 1.5 Billion in 2022. Looking forward, an IMARC Group report expects the market to reach US$ 3.0 Billion by 2028, exhibiting a growth rate (CAGR) of 12.2% during 2023-2028.
Sharad Kulkarni, Dormer Pramet India: Automotive components driven by the production of both in traditional IC engine and electric vehicles continue to lead the cutting tool demand picture in India. In addition to this, high demand in the consumer goods industry leads to high demand in the Die & Mould segment. Other segments like defense, railways, and capital goods industry also are contributing in a good way to the overall demand.
Arun Upanal, Upanal – CNC Pvt Ltd: When it comes to demand, metal cutting applications find space in every piece of business. In today’s scenario, we see more opportunities in Plastic Die & moulds as the import of moulds has reduced drastically post covid and our small and medium-scale industries have supported steeply to provide solutions domestically just in time and this has enhanced their businesses with good orders running till date. Also, the Aerospace, Defence, and Automotive sectors have grown in size which has kept the ball rolling.
Q4: Which technologies, in your view, will be the biggest growth drivers for the global and therefore the Indian metal-cutting machine tools industry?
Rajesh Ghashi, CHIRON INDIA Machine Tools Pvt. Ltd: The future trends in machine tool that we can now expect that Industry 4.0 is now widely used, you would see new advanced hardware and software that would include smart features & networks, automated and IoT-ready machines, Artificial Intelligence and more advanced CNC software.
We can see more powerful networks coming into use with wide-range coverage even over Wi-Fi to transmit data faster. This increased reach in wired and wireless networks will make automation much simpler. The industry will continue to build smarter machines which would mean connectivity to much smarter devices. Smart machines and robotics will handle more of the industrial work especially where human intervention would be seen as more dangerous to deploy. The use of AI will also help to program the machines will increase in real-time situations. The CNC Software would also see more robust and advanced CAM software would allow programmers to see and simulate real-time processes in a more precise manner. The machine tools of the future will be smarter, easy to network and less prone to errors and automation would be more efficient. This would allow workers to control the machines remotely more easily and increase the overall productivity
Vineet Seth, Mastercam India: We expect Multitasking machining and Multi-axis machining to be the biggest growth drivers for metal cutting and Robotic applications as well as Hybrid (Additive-Subtractive) manufacturing on the sunrise technology fronts. There is a great appreciation of Industry 4.0 and 5.0 practices which are forecast to grow exponentially in the next 5-10 years.
Dhiruj Sarda, East Coast Magnets Private Limited: Any technology which directly or indirectly takes the manufacturing process towards being energy efficient shall be the biggest growth driver. Industry 4.0 technologies such as automation and sensor technology all are tools that make the process more efficient and in the end more energy efficient. The stress on energy efficiency is because that represents the optimum utilisation of resources.
Our product development and patents are driven to be adaptive incorporating sensing technology.
Rizwan Khan, SupplyPoint: We have been talking about seamless solution where entire inventory is system driven without any interference from operators/supervisors that enables shop floors with 100% traceability, accountability, accessibility and control on distribution of consumables. SupplyPoint has been offering Industry 4.0 Intelligent Inventory management and vending machines. With our proven technology more 65000+ of units installed across the globe and being the masters and innovators, we believe Industry 4.0 shall be the driving element to grow Metal-Cutting Machine tool industry.
Gautam K. Ahuja, Gühring India: While additive manufacturing is beneficial for product development and prototype manufacturing, the focus will be on automation and smart technology for mass manufacturing set-ups.
Tridib Majumder, Quaker Houghton India: We believe the future lies in Digitisation through Data-Driven Solutions, Sensor technology for monitoring, controlling and optimizing performance. Our objective is to keep our customers highly competitive in an ever-changing world, our industry-specific application expertise in fluids, combined with the use of QH EQUIPMENT and advanced hardware and software technology are enabling our customers in digital transformation and smart manufacturing. Our goal is to bring differentiated value to our customers so they can operate safely, sustainably and at the lowest total cost of ownership.
- With QH FLUID INTELLIGENCE we intend to measure all process parameters accurately and reliably with differentiated sensors.
- Control fluid performance using our extensive knowledge and QH FLUIDTREND cloud platform to capture and analyze real-time data
- Optimize fluid and machine performance by delivering predictive and preventive insights that increase tool life , decrease downtime, and reduce cost per machined part.
Arun Upanal, Upanal – CNC Pvt Ltd: The lack of skilled labour and inconsistency of manpower retention in the industries, has led to the increased requirement for automation which includes robotics and Industry 4.0. With the incubation of robotics and Industry 4.0, manufacturers will have an initial burden of Investment but the scaling to the demand of the buyer and the quality of the product will be able to help in filling the gaps of inefficiency and profits can be seen more evidently within the same cycle of return of Investment which is running at present.
Sharad Kulkarni, Dormer Pramet India: Main technologies which are influencing global demands are:
- Automation in form of the introduction of robotic elements in the manufacturing process
- Digitalisation – CAD /CAM, IOT , AR/ VR
- Multi-axis machining leading to better quality, fewer set-ups, and improved productivity
- Hybrid manufacturing process – a combination of additive manufacturing followed by traditional machining process.
- Complex work-piece materials
These technologies are improving output, cutting down costs along with improvement in end-product quality thus enabling to create more demand.
Q5: India’s Metal Cutting Machine Tools (MCMT) companies face a number of challenges such as dependence on the cyclical growth of industries such as auto and construction, intense competition, and complex distribution networks, etc. Can you share with us some of the biggest challenges you face currently?
Rajesh Ghashi, CHIRON INDIA Machine Tools Pvt. Ltd: The major challenge right now is to set right the supply chain as this has been disrupted since the onset of Covid. The bigger challenge is getting the electrical/electronic parts on time. However, our strategies are in place to address the supply chain issues, and focus on our future product developments, sustainable manufacturing, etc.
Rizwan Khan, Sales Manager – India, SupplyPoint: We look at India as a great economy in a positively transformational phase where along with Large manufacturing companies; MSMEs are also seeking a system-driven solution without any interruption from People. Any decision maker in a company needs zero manipulated reports from the shop floor, this is the biggest challenge in the industry and with SupplyPoint we enable our customers to have seamless reporting systems right from the vending machines installed that are integrated to their ERP/SAP. Having a seamless reporting system without any human intervention is the need today.
Talking about the challenges in Supply Chain, each supplier needs a local base or warehouse to have continuous supply to their customers. Having the right order at right to fulfill the demand on site is perceived to be improving day by day perhaps still needs more perfection in driving the supply chain. We have been working with Industrial giants supplying thousands of consumables, MRO items without any delay where our systems on the shop floors are directly sending order requirements to the suppliers as well. SupplyPoint solutions are capable to address this challenge by allowing its users to maintain the Minimum stock level /Critical stock levels to trigger requirements with lead times to the suppliers. However, the transition and adaptation of this technology is a current challenge that we face today.
Vineet Seth, Mastercam India: Our challenge has always been the hesitation of small companies to shift away from manual programming, as well as reluctance to stay away from rampant piracy. CNC Machines are becoming mainstream, having nearly replaced conventional lathes and mills for most metal-cutting operations.
Arun Upanal, Upanal – CNC Pvt. Ltd: Indian machine tools companies are the last to enjoy the profits. For the machines being used for precision applications, most of the critical raw materials like CNC, LM guideways, ball screws, and bearings have to be imported due to a lack of local source of supply. Any fluctuations in the international market will impact the buying cycle of Indian machine tools and we have limited supply chain network to find better deals. Of course, we have strong competition from import players but our execution timeline with all these difficulties has boosted our sales.
Dhiruj Sarda, East Coast Magnets Private Limited: Any industry today faces the same challenges as faced by the machine tools industry. We are the face of it when the downturn comes we are the first ones to be put on the backburner and when the upswing comes we are the last to get the advantage. Having said that, in our opinion, it is a boon as it forces us to be innovative to improve, our products and services. It keeps us on our toes and pushes us to be agile and adaptive to the environment.
The biggest challenge we face in the domestic market is the lack of trust in domestic products.
We feel that customers prefer to buy outdated technology just because it’s “IMPORTED”. More than anything this is the challenge we face in the domestic market. The cycle of demand will always be there but until we trust and give the opportunity to Indian Companies how will we all grow?
The change in customer mindset is not in our hands but what we can do is we have to make efforts, we have to work double hard to provide better technology and better service for lesser value realization than IMPORTED products.
Sharad Kulkarni, Dormer Pramet India: One of the main challenge the industry has faced in the last decade was a lack of private CAPEX in a big way. This was due to factors such as macro-economic issues, problems with the banking sector, etc. This did not allow the Indian industry to scale up very quickly. But now with government supporting manufacturing industry in form of PLI, we should see return of private investment in a big way.
The second issue is the lack of well-trained manpower which reduces the productivity and leads to a decline in competitiveness.
The Indian manufacturing industry is still very much dependant on low-cost labour as a means to reduce its manufacturing costs. The time has come for the industry to look at other areas of improving competitiveness like embracing new technologies. This will not only lead to catering to the local demand, but also will lead to a boost in exports.
An improvement in the above factors will reduce dependence on cyclical industries and will help India emerge as a preferred destination for manufacturing.
Gautam K. Ahuja, Gühring India: Increase in raw materials costs and logistics costs pose a herculean challenge to manufacturers to satisfy the customers as well as to achieve business sustainability in the price-competitive market.
Tridib Majumder, Quaker Houghton India: Apart from the mentioned challenges, as a specialty chemical manufacturer we have to deal with a complex manufacturing process where more than 20-25 different additives and chemicals are blended at the right proportion, supply of raw material from various sources has been a challenge in the last 18 -24 months. Each Industry segment has specific requirements and our offerings are tailored to the customer processes and needs. The current geopolitical situation has thrown up various challenges creating bottlenecks in the supply and distribution of raw materials and sometimes with finished products.
In order to address these challenges,Quaker Houghton has upgraded our state-of-the-art plant at Dahej in Gujarat. The site has incorporated unique features in its design, such as high-efficiency induction motors to reduce energy , water condensation recovery systems and wastewater treatment technology that supports Quaker Houghton ‘s environmental goals. Our R&D team has also come up with localized solutions to surmount these challenges
Q6: Can you share with us the strategies you are following for growth and profitability?
Gautam K. Ahuja, Gühring India:A stronger marketing and distribution strategy, optimizing the processes to achieve more efficiency, and an increased focus on customer support and awareness are the three main pillars of our strategy.
Rajesh Ghashi, CHIRON INDIA Machine Tools Pvt. Ltd: Grow profitably, acquire market shares, boost global business: The CHIRON Group will be pursuing ambitious objectives over the next few years. To help achieve them, the company is setting itself apart from the competition with its product range. The company’s commitment to sustainability, an important topic for the future, gives customers and potential customers even more reasons to choose the CHIRON Group. The company has already achieved its first major success in this area: From the end of the year, production at the German sites will be carbon-neutral. The CHIRON Group documents the measures it has taken and success it has enjoyed so far in its first sustainability report „SUSTAINABILITY by Performance and Precision“.
Dhiruj Sarda, East Coast Magnets Private Limited: When the business was started by our Great Grand Father in 1958 the purpose of the same was to be an import substitute for the products being imported.
Our strategy for growth in the domestic market has not changed for the past 60 years – it is to provide better quality products manufactured and designed in India for our customers.
Innovation and development of product design have been our core focus. From 2000 onwards with the new millennium we shifted gears towards developing our own technology, patenting, and promoting the same.
Providing bespoke solutions to customers and being flexible with design and product and giving the right solution has been our focus.
Our biggest strength has been the option of giving what the customer wants rather than shove down the throat what we have in “standard” design.
For us the standard design is what the customer wants.
Vineet Seth, Mastercam India: We have always been customer centric in our approach and this reflects in every individual in our organization. We have a sales to technical resource ratio of around 1:4 and we have regional offices within 6-8 hours of response from mainstream industrialised locations in the region. Additionally, we also have a very talented reseller ecosystem, who believe in the same philosophy as us. Furthermore, offering world class solutions and services at affordable costs to micro and small industries, are our strengths.
Rizwan Khan, Sales Manager – India, SupplyPoint: We are focussed with our Customer support and after sales that in itself helps us to get customer reference from the existing installations. SupplyPoint has been installing machines across India in with quick and swift responses in support. While provide Industry 4.0 solutions we are also equipped with software remote support 24X7 to our customers.
We have a strong distributor network in India that covers 18 different states across the country and we are looking forward to penetrate the regions with customer support. We believe in customer referencing that has helped us to add number of machines in West and Northern part of the country. Same is being replicated within the Southern parts as well.
Sharad Kulkarni, Dormer Pramet India: Our strategy comprises the following tenets:
- Building a strong and reactive distribution network helps us to deliver value to end-customer and helps in customer base expansion.
- Introduction of new products at right price points help the end customer reduce their costs significantly and in-turn helps grow our won sales and profitability. We also try to make it simple for our customer to select the products and use it. This in turn brings in efficiency and helps to cut down their time.
- With a very wide range of high-performance products, we try to cater to all metal cutting needs of the customer. This simplifies their procurement process and reduces the in-direct costs
- By increasing our training efforts on the metal cutting technologies, we help customer to improve their competency and which in turn reduces their costs.
This leads to higher growth and profitability for us.
Arun Upanal, Upanal – CNC Pvt. Ltd: India has got enough talent pool to grow for the global standards and presently lot of research and developments are under trails to showcase our best product building capability and reliable solutions for the society to get better lifestyles. Today in the buyer’s market customers are smart to choose their requirement and we as manufacturers need to understand the pulse of the buyer and work effectively to cater proper solution at right time, right product, right service, right information and right price.
Tridib Majumder, Quaker Houghton India: Backed by Quaker Houghton’s expertise and solutions, more than 15000 global customers were able to produce essential goods such as steel, aluminium products for end markets like transportation, energy , and packaging.
Quaker Houghton believes in Profitability through Sustainable Growth that will create social, environmental and economic progress. We aim to deliver solutions that result in a better, safer world and make a positive difference in the lives and organizations we touch. Our sustainability goals focus on areas where we believe we can have the greatest impact. Our goals are aligned to the United Nations Sustainability Development Goals.
Our Journey has just begun, we will continue to invest in Sustainability to improve our operations, reduce our carbon footprint, enhance workplace health and safety, and support our colleagues and the communities where we live and work.
The future at Quaker Houghton is bright, and together, we are committed to delivering sustainable value for our customers and communities.
Q7: Can you share with us an overview of your company’s product offerings to be highlighted or launched at IMTEX 2023.
Gautam K. Ahuja, Gühring India: We will be showcasing our latest products in Drilling, Milling, Reaming, Threading Grooving, Micro machining. Our Tool Management systems, PCD tools and EV machining solutions will be the added attraction. Our focus will be on discussing & providing quality machining solutions to Customers to improve their productivity.
Rajesh Ghashi, CHIRON INDIA Machine Tools Pvt. Ltd: At IMTEX 2023 we will introduce a new revolution in the dynamic and highly precise world of machining tiny medical instruments, delicate jewelry, and the most intricate watch parts – the MICRO 5 five-axis machining center from CHIRON Group SE which is extremely compact and can be set up very quickly almost anywhere, in the production hall or right at the workstation. The “5” in the name stands for the ideal 5:1 ratio of machine size to the workpiece, for five times lower weight, and for maximum efficiency. Energy consumption is 50 times lower in comparison to conventional systems.
Vineet Seth, Mastercam India: We will be demonstrating live the newest features released in Version 2023. Similarly, we will also do a curtain raiser on a few of our upcoming cool features in version 2024. The Mastercam range includes 2.5 to Multi-axis Milling, Turning and Turn Milling, Mill-Turn, WireEDM and Modeling for manufacturing. Certain special add-on modules like Blade Expert and Port Expert will also be available for demonstration at our booth. The use of Dynamic MotionTM Technology for efficient roughing and accelerated Finishing will also be on display.
In addition to the above, Mastercam 2024, is due to be released in June of 2023 and to that effect, we will be raising the curtain on some fantastic and upcoming features, which are now released to our beta users across the world.
We will also be running a number of live demonstrations with our Machine Tool Partners at IMTEX. Please follow our social media pages to stay tuned to each of these projects and find details regarding the booth location to see them live during the show.
Dhiruj Sarda, East Coast Magnets Private Limited: At IMTEX 2023 we shall be introducing our new range of magnetic chucks based on our patented designs.
These chucks are made to be more accurate while at the same time, they are more energy efficient in production as well as usage thereby trying to make a small step in reducing the carbon footprint of our organisation.
SAFEBAT – is our new range of lifting magnet with wide range of proprietary sensing technology for safer usage of magnets
SAFEFLUX – technology in magnetic chucks shall be displayed to give real-time feedback of the magnetic field in the chuck as well as the clamping force.
MAGNASLOT – A new magnetic chuck for the Die-Mold industry with better demagnetisation of components after exposure to magnets shall be introduced. This makes machining of pre-hardened components with magnets very easy.
Rizwan Khan, SupplyPoint: We are coming up with State of art display at IMTEX 2023 with complete solutions on Store Automation, Tool Vending and traceability we shall be doing live demonstrations for the visitors as well, witness the patented technology of Progressive drawers that can manage a single piece (Insert) with 100% accountability.
Stand details: Hall 3A, Stand no. C102.
Arun Upanal, Upanal – CNC Pvt Ltd: IMTEX 2023 will be a bounce-back event for the metal cutting industry as the last IMTEX was in 2019 and after 4 years we had limited resources to reach our customers due to the pandemic and its aftereffects. But now everybody has regained the spirit to serve their customer with the latest technologies and we are going to display our new series of VMC’s, 5-axis VMC machine, multi-tasking machines, compact turning centres, high-end HMC machines and automation solutions for all these machines and Industry 4.0 technology.
Tridib Majumder, Quaker Houghton India: We welcome you at IMTEX 2023 at Quaker Houghton booth no B121 in Hall-5 to understand more about our offerings to achieve your sustainability goals.
Passionate About Precision
Marposs, a leader in Measurement, Inspection and Testing solutions is participating at IMTEX 2023. Luca Matteucci, Managing Director – MARPOSS India Pvt. Ltd shared with us his organization’s vision, and the solutions Marposs will be showcasing at IMTEX 2023 at HALL 3A/BOOTH B101.
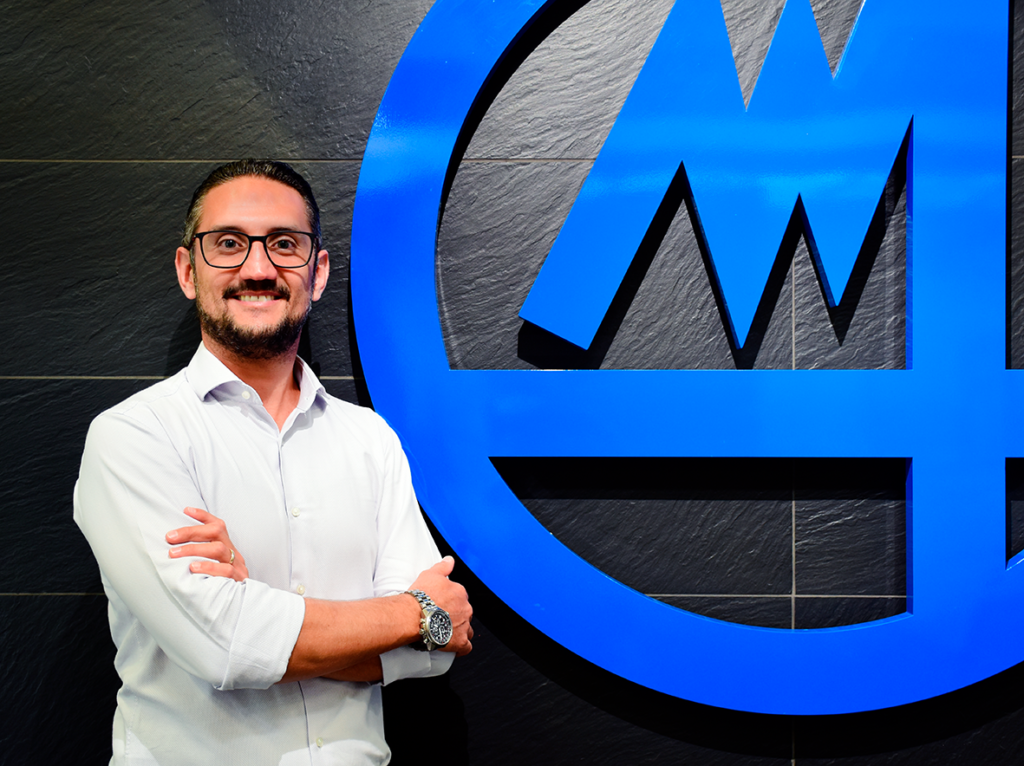
Marposs: Organization’s Vision
Marposs celebrates this year its 70th birthday spent in providing customers with top quality metrology solutions for metalworking production and is looking for a future transformation into a global provider of Inspection, Testing and Control solutions for any type of industrial process.
Machine vision solutions supported by AI to check hairpin or complete assembled stators, EOL tests for Batteries and Fuel Cells, Leak Tests solutions for battery packs and housings as well as cooling plates are just few of the newly developed solutions dedicated to those Customers investing in the new sustainable mobility.
Specifically, in the field of Machine Tool, besides striving to keep our traditional measuring solutions for Grinders, Lathes, and Machining Centers machines on the edge of quality, we have invested in providing solutions for quality control during the Roll-to-Roll process for anode/cathode films, as well as high precision wheel balancers to fit gear grinders in order to guarantee extremely smooth surfaces on gears for noise reduction. Our TTV thermal camera is designed thought to optimize the HPDC process and increase the quality production of Aluminium/Light alloys parts, which are so important to reduce weight and consumption; our Machine Monitoring Solutions are able to keep under control all machine parameters to optimise machining process, increase tool life and reduce energy consumption for a low-impact production.
Marposs solutions are widely used on silicon wafer machining lines for Semiconductor production as well as in several EOL solutions for measurement and leak test of Consumer Electronic components.
In the Biomedical segment, we can offer a variety of solutions for several quality control issues in the sector of disposables, dental implants, and orthopedic joints. Vials as well as glass containers of virtually any dimension can be checked easily and precisely with our flexible Visiquick measuring system.
Organization’s Contribution to Industry Growth
Since its foundation 70 years ago, Marposs core competence has been focused on improving the quality of the manufacturing process. Our first revolutionary product, whose success allowed the company to grow rapidly both in volumes and in international coverage, was an In-Process measuring system for grinding machines. Until that time the only possible way to get the right dimension of a precise part on a grinder was to stop the process, which was to manually measure the part with a caliper, a highly unsafe act. The number of times this was necessary depended on the ability and experience of the operator. With the Marposs system, the part diameter was constantly under control and the measuring result was used to stop the machine when the right dimension was reached. The result was reduced machining time and higher production rates, consistent part quality, and higher safety for the operator.
The Marposs solution soon became a “must-have” option on each grinding machine and Marposs is an indispensable partner for all grinding machine makers. This long-term partnership has allowed Marposs to absorb the knowledge of the process requests for improvement, leading to the development of a complete range of solutions and a product portfolio that is nowadays an absolute worldwide reference.
Marposs then decided to apply its expertise in process control to other types of machine tools and other machining processes, investing in R&D resources as well as in M&A operation to be able to develop a bunch of solutions, such as:
- Grinding wheel balancers keep under continuous control the correct rotation of the wheel thus allowing the best grinding surface roughness on the part and increasing the life of the machine structure and of the wheel itself. In the current evolution of the automotive towards electromobility, the noise reduction, after the elimination of the traditional combustion engine, is focused on gears; no gear grinder can achieve a perfect gear without a wheel balancer on it.
- Post-process measuring stations after turning or grinding operations: several key parameters of a part are measured after machining, and the results are stored and elaborated to adjust the machine in case of a trend in the process.
- Probing solutions to set up machine coordinates and enable precise and controlled machining cycles, as well as part measurement during and after the cycle of the workpiece still fitted onto the machine (lathe or machining center or milling machine).
AT IMTEX 2023
Do Visit HALL 3A / BOOTH B101 to know more about our latest product & technology at Imtex 2022
ZEISS India’s Medical Technology Solutions
Q. Medical manufacturing is a growing field and ZEISS is known to have good solutions in the space of Metal implants and Plastic parts used in Devices of the Healthcare industry. Give us a view of your company’s main solutions for this area, and some of the recent innovations in this field that could help the healthcare manufacturing sector in India
Manoj K Sundaram, Carl Zeiss India: Medical technology is an area that Zeiss is known to have historically contributed to, with transformative solutions in mission-critical processes like surgery and diagnostics, for example. Please give us a view of your company’s main solutions for this area, and some of the recent innovations in this field that could help the healthcare sector in India.
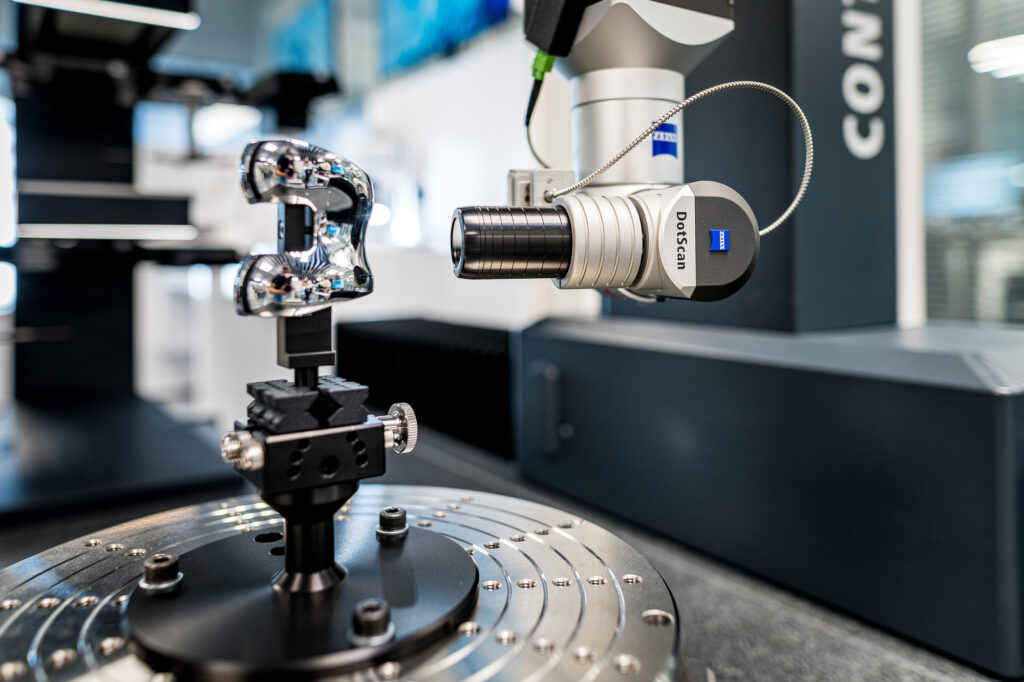
ZEISS understands the medical industry regulations, their requirements and the challenges faced by manufacturers and their quality departments. Our connected quality intelligence portfolio offers tailored hardware and software solutions that support industry standards and work as a coherent system to give the manufacturers the certainty they need to gain the productivity they desire.
Dental, Shoulder and Spinal Implants have precision shape with freeform profiles, Bone plates have Multi axis measurements of shallow bores, Hip Implants have multiple parts and material with narrow band of tolerances. The above challenges can be addressed by us in unique ways combining technology, data collection and traceability to stringent medical regulations.
Medical plastics deliver a pharmaceutical compound to its target site. Therefore, they’re vital to human health in everyday life and must guarantee functionality and achieve their desired therapeutic effect. In ensuring proper production and complying with a variety of industry norms, you must perform quality control on large volumes, process small features and non-standard geometries, and correctly handle plastics that may be transparent, sensitive, or prone to bending.
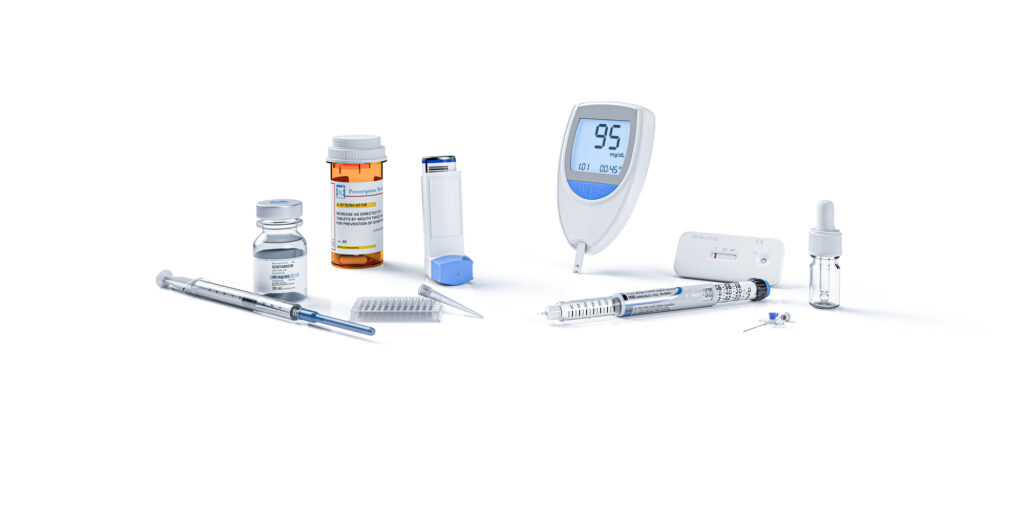
The challenges can be ensuring high volume production of Basic Plastic housings like Aerosol covers or multiple plastic pieces in a assembly with micro freeform shapes and tight tolerances like in Insulin pens, syringes. Self-infusion pumps and devices with electronics have thin walled structures and transparent plastics and the molds and inter-fitment accuracy are critical.
Solutions start at Granulate analysis of plastic raw material used in production. It moves to material friendly measurement using Optical or X ray technology is a mandate. Particle contamination is a key topic in medical industry and analysis of critical particles detected in the component is an important part of workflow.
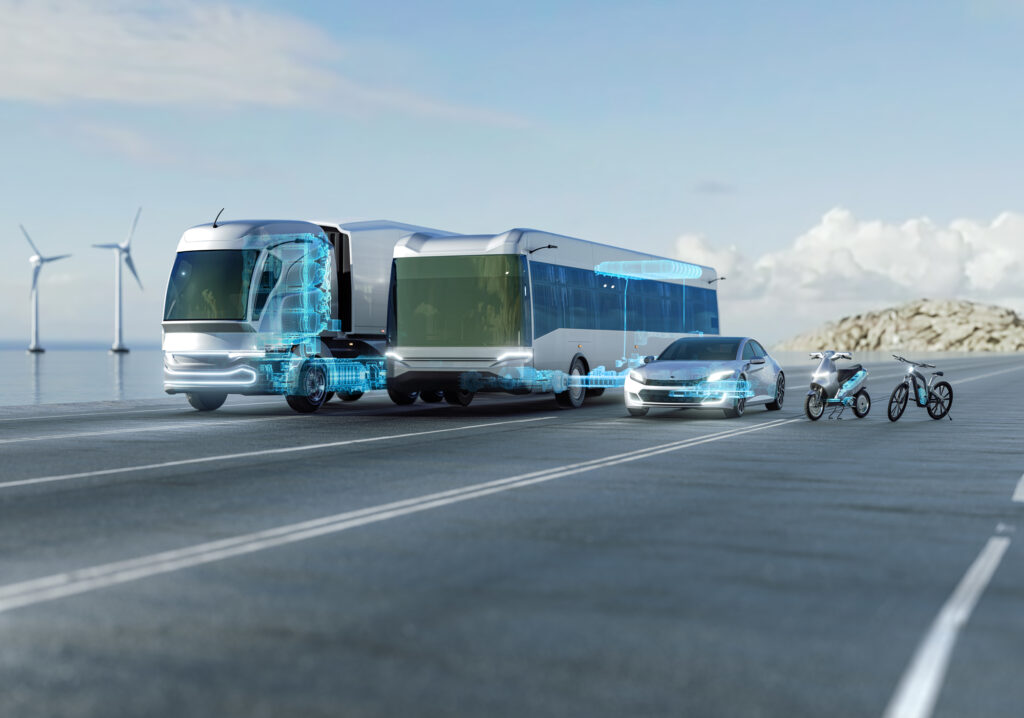
For more information, please get in touch with us at info.metrology.in@zeiss.com
LMW at IMTEX 2023
At IMTEX 2023, LMW Machine Tool Division will be launching and displaying some of its latest machines in turning, milling and turnmill centers. Its latest turning centers are poised to have higher speeds thereby reducing the cycle time considerably for higher productivity. It comes with thermal stability for effective chip and coolant management. This machine is best for small components and high volume production. LMW’s new generation turning center machine is compact and high speed and also come up with a larger dia turning center to address the automobile sector.
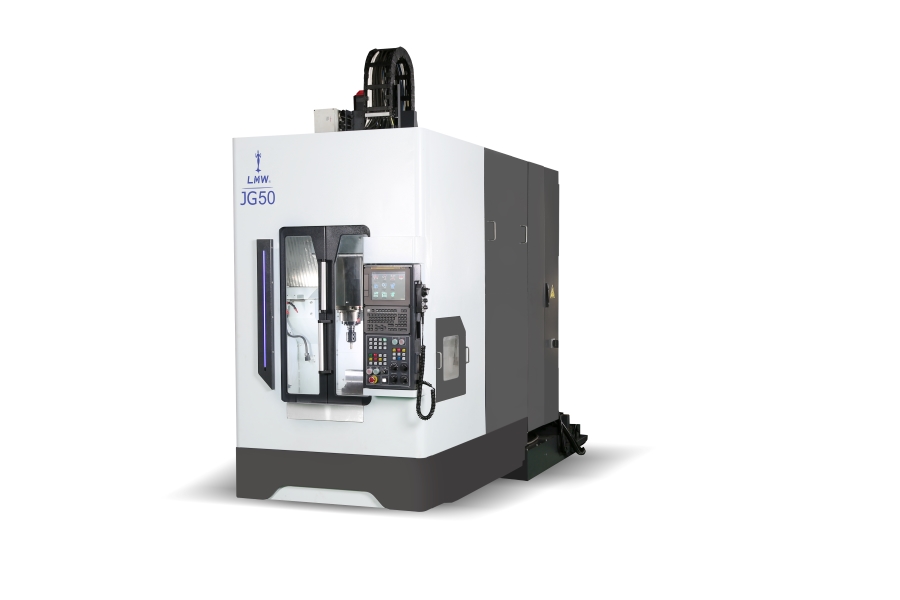
LMW’s new range of vertical machining center from the popular J series has a pallet changer which is a major requirement from many high-volume production customers. Adding on to that, its new VMC has BT50 tooling for heavy duty machining to meet the requirements of large components (Castings & Forgings). The company is also displaying a larger size VMC to meet the needs of die machining in foundry industry, equipped with the state-of-art CNC. The company is introducing a new generation precision machine in HMC to address the industries like Agri & Earthmovers, Valves.
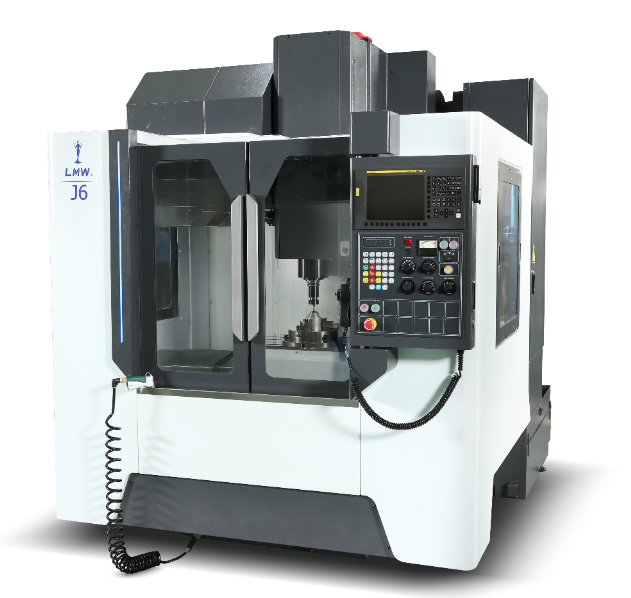
The new turnmill center is a technology machine with 4-axis, has capability of gear hobbing and robotic automation, also look out for the brand’s new JV series of drill tap centers, machines that are designed for high speed machining for materials such as Aluminum and special aluminum alloys. The machine be suited for machining of components for electronic segment, such as mobile case, laptop, tablets, etc. LMW’s high speed machine for high volume production has spindle speed upto 24000 rpm, 48 m/min rapids and acceleration upto 1G. In addition, all the machines are IOT ready.
LMW: A Legacy of Innovation and World-class Excellence
Lakshmi Machine Works Limited, founded in 1962, is leading textile machine manufacturers in India and one among the three in the world to produce entire range of textile spinning machineries. The value driven machine tool division of LMW started its journey in the year 1988 to produce finest range of CNC machines. The company has collaborated with Japan’s Mori Seiki company limited to manufacture turning center and machining center. Later, they have associated with Mikron Switzerland in 1995 to produce high precision universal milling machines for tool room application.
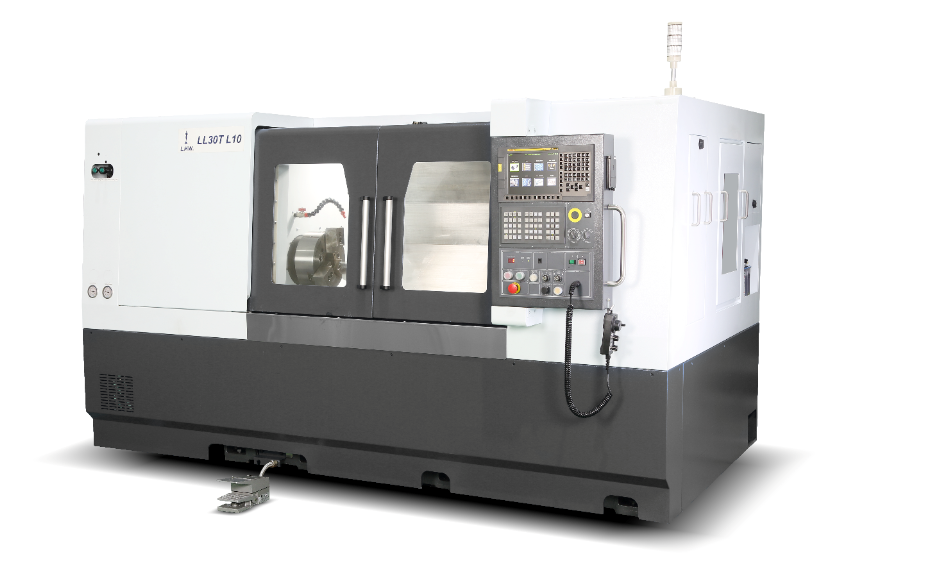
From 1996, LMW Machine Tool Division developed their own capability to design and manufacture world class CNC turning and machining centers. The high precision mother machines coupled with skilled people produce high quality products. They have made substantial investments on manufacturing facilities, which brings technological competence that address the global market. A dedicated spindle assembly make spindles upto 24000 rpm. They make different spindles like, belt driven, direct driven and built-in motor spindle. These spindles undergo spindle run testing, spindle dynamic balancing. All the assembly lines are dust-free and temperature controlled to ensure maximum accuracy.
Quality is embedded in the DNA of LMW. It is reflected in every element of the production procedures and services. They incorporate cutting-edge technologies for testing and validation. The laser calibration of linear and rotary axis, and spindle check inspection are followed to ensure precision and high-quality products. The company focuses on major demanding factors in the market 1) Accuracy & long lasting repeatability 2) Reliability 3) Reduction in cycle time 4) Low cost per component 5) High productivity. To sum it up, The company termed as precision, performance & productivity as the vital steps towards delivering excellence and LMW believes in delivering prosperity to its customers through LMW’s products and solutions.
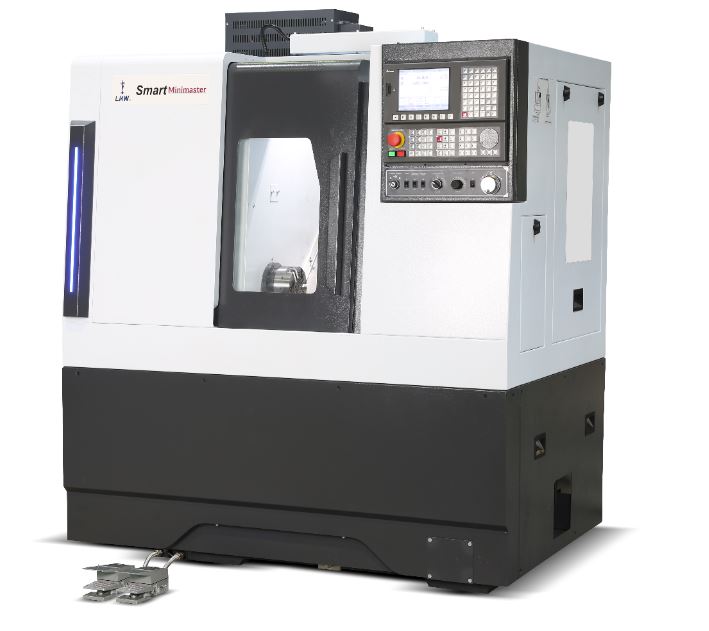
The company currently has 55 models and 88 variants of machines in Turning center, Machining center and Turnmill centers. The company has a strong R & D which focusing on the innovation based on the market requirements. The machines must be easily customizable for different industry needs. They have introduced products which are very compact, cost effective and high speed which will address the needs of small component manufacturers where volumes are very high like the bearing industry. They also have products that are planned for the global market, which means the machines are state-of-art, high feed rates with rapids upto 60 m/min and spindle speeds upto 24000 rpm. The machines also have accelerations of 1G. This means the non cut time is reduced to a very great level resulting in faster and higher production. In addition, all their machines are IOT ready. LMW has a strong application team for providing solutions to their esteemed customers.
On the operations side, they have introduced new customer portal for online sales of spare parts (e-commerce) and mobile Apps for customer connect. The entire service operation is digital or simply paperless. In the last 3 years LMW has given a great focus to digitalization.
The company has established a pan India network of sales and services that cater to every industrial city in India. Machine tool division provides integrated solutions for various industrial needs in Automobile, Aerospace, Die & Mould, Defence, Pumps & Valves, Railways, Medical Equipment, Forging, General Engineering, etc. LMW also provides automation solutions such as simple loaders, Gantry systems, and Robots that are tailored to meet the customer requirements.
LMW- A Legacy of Innovation and World-class Excellence
Over 60 years of Engineering experience and 35 years in machine tool manufacturing.
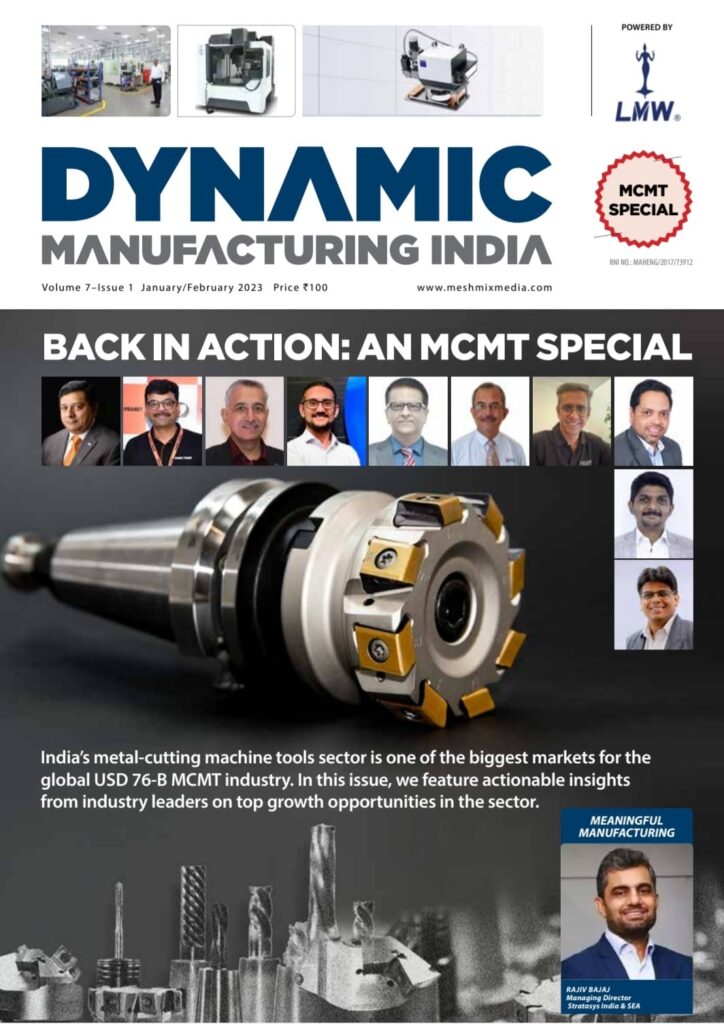
Do Read DMI Jan_Feb 2023 edition – https://www.machineinsider.com/dynamic-manufacturing-india-metal-cutting-machine-tool-special/