DMG MORI Die & Mold Excellence Center
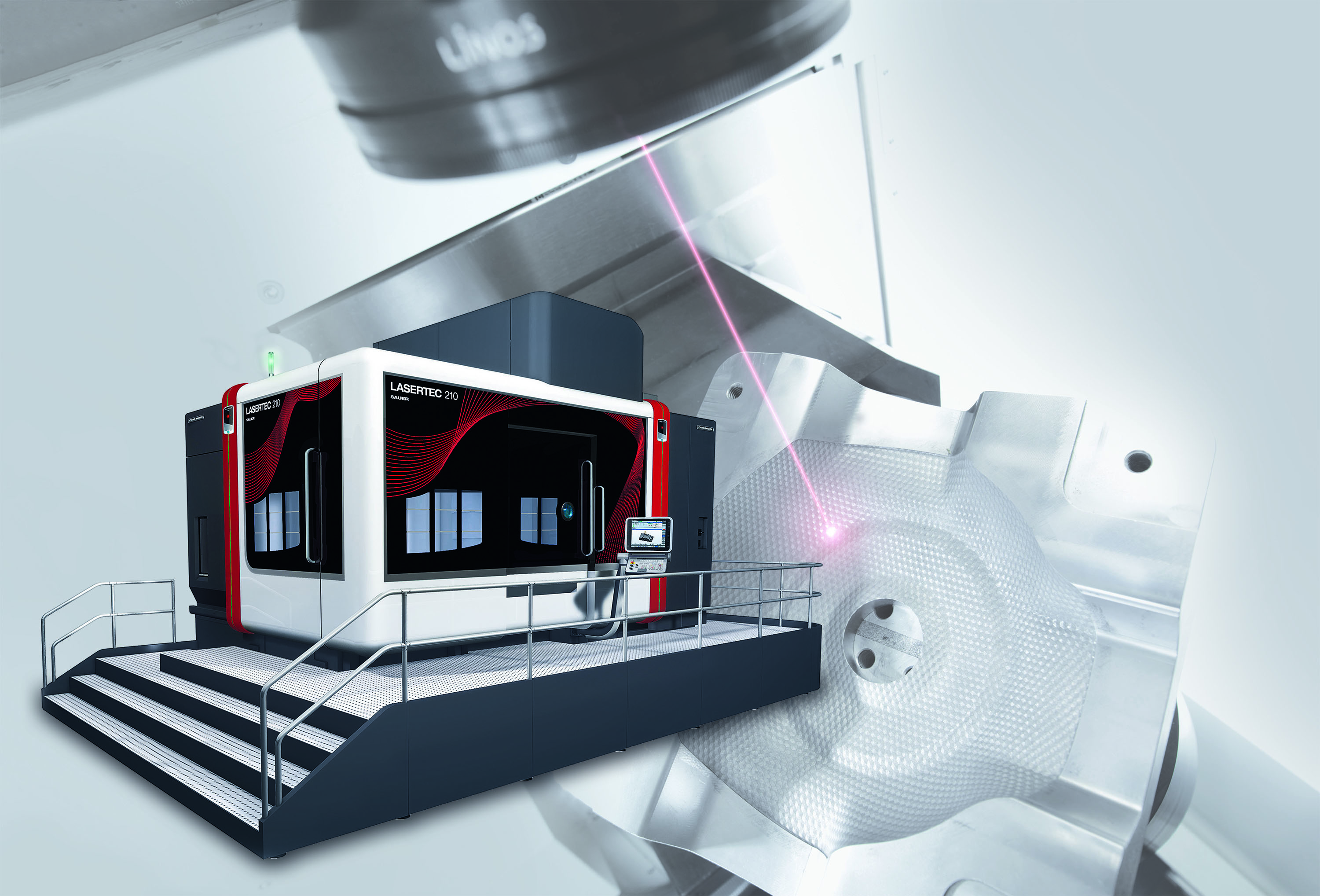
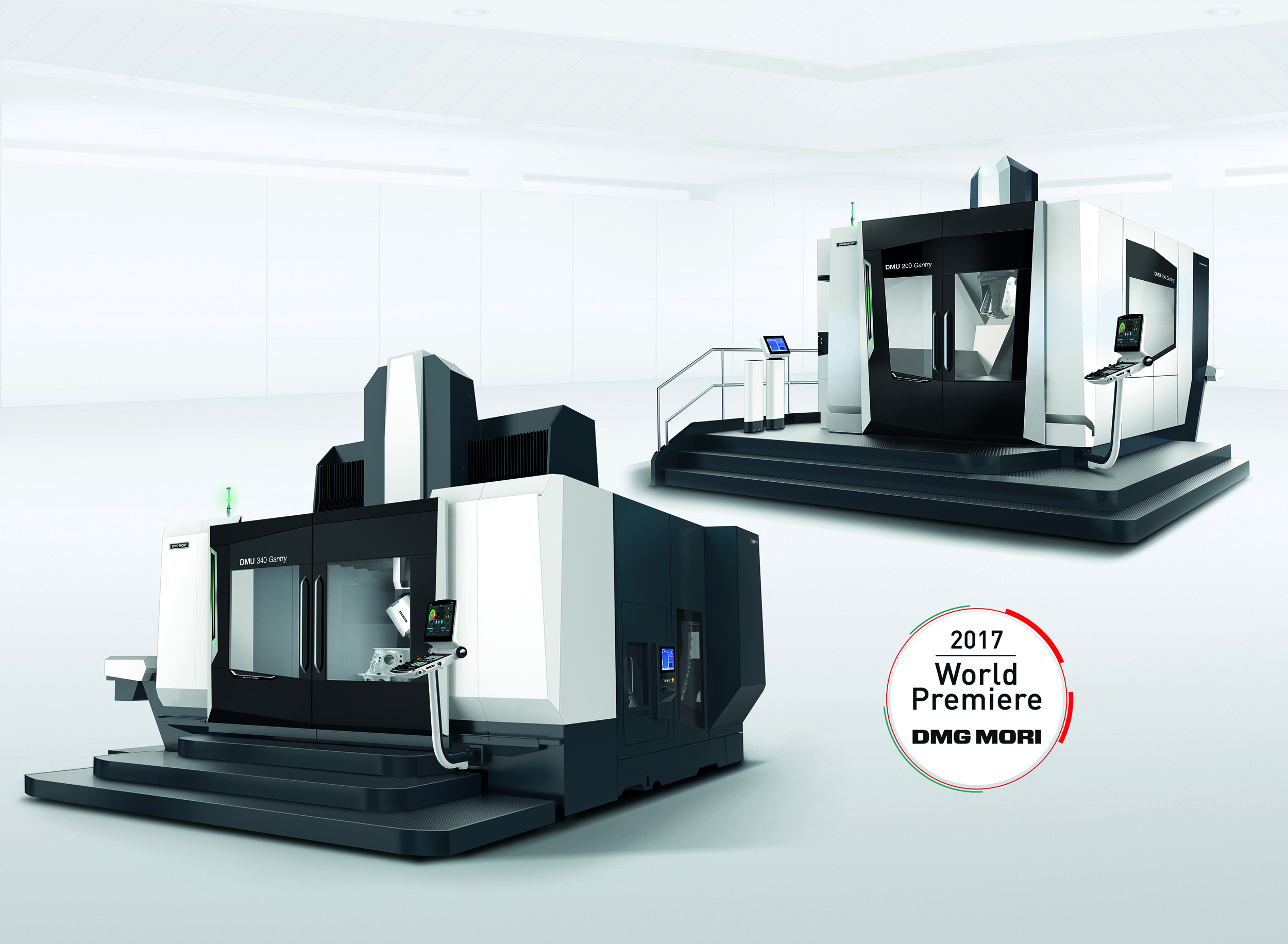
Picture: DMG MORI
Technology Excellence In Die & Mold
In the Die & Mold Excellence Center, DMG MORI has been bundling decades of experience in die and mold making with a forward-looking product portfolio and the design of individual manufacturing solutions with continuous process chains.
Maximum demands on accuracy and efficiency mean the die & mold sector has always been a driver of technology for DMG MORI. Five-axis simultaneous machining for demanding geometries, HSC technology for optimal surface qualities and intelligent automation solutions for maximum productivity are just three examples with which the machine tool manufacturer has been convincing users for more than 20 years.
With consistent further development of machining technologies and innovative software solutions for a digital future, DMG MORI implements productive manufacturing concepts for the challenges associated with die and mold making in the Die & Mold Excellence Center. The experts there work together with customers on cross-sector competitive manufacturing concepts both for small as well as large molds and dies. Highlights in the full-liner product portfolio are the powerful vertical machining centres from the DMC V and NVX series, the versatile 5-axis universal milling machines from the DMU monoBLOCK and DMU eVo linear series as well as the XXL machines including the DMU 340 Gantryas the world premiere at the upcoming EMO.Moreover, DMG MORI is setting new standards in surface structuring with the LASERTEC Shape technologies.
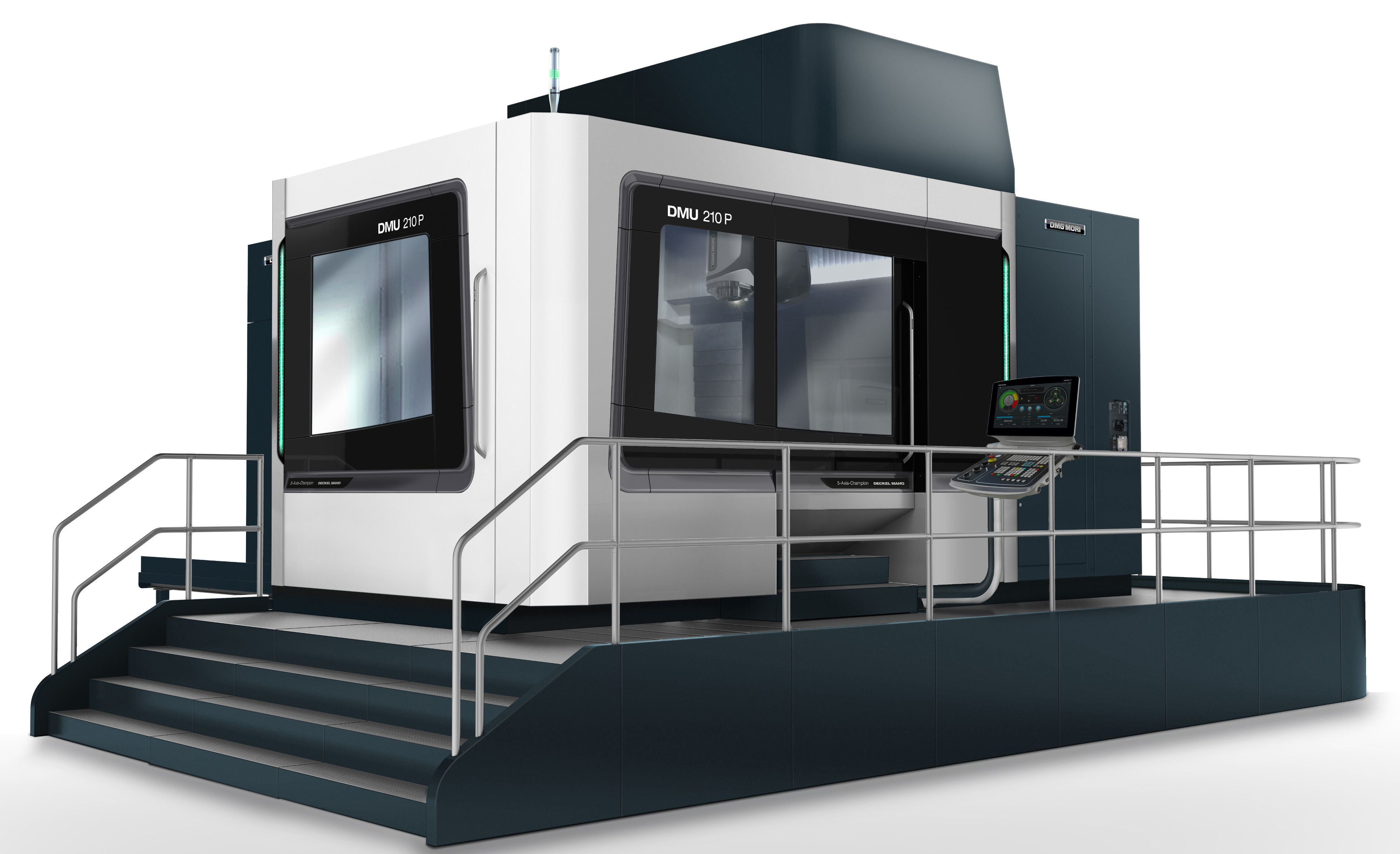
Picture: DMG MORI
DMG MORI Die & Mold Excellence Center
Die and mold making are among the core competences of DMG MORI. With far-reaching effects, as Markus Piber, Managing Director of DECKEL MAHO Pfronten GmbH, says: “Great importance has been placed on die and mold applications at DMG MORI for decades, which on the one hand has resulted in our enormous experience in this field and on the other has given and continues to give rise to path-breaking technologies.” The demands on precision, long-term accuracy and surface quality has transformed die and mold making into one of
the most challenging manufacturing areas. “These demands are met by high-precision and dynamic machining centres”, adds Markus Rehm, Managing Director of DECKEL MAHO Seebach GmbH.
DMG MORI concentrates their experience and skill in die and mold making in the DMG MORI Die & Mold Excellence Center. The developers there implement cross-sector and unique processes – from programming through milling strategies up to the selection of holders, dies and die clamping as well as automation solutions. Markus Piber comments on the work method: “We involve our customers in the projects at a very early stage to enable us to learn from one another and achieve optimal production solutions.”

Picture: DMG MORI
Full-liners in die and mold making
DMG MORI’s large product portfolio makes the machine tool manufacturer the right partner for every die and mold application. It starts with 3-axis machining on the powerful vertical machining centres from the DMC V series, which already set the standard with the speedMASTER® with its 20,000 rpm spindle, an innovative cooling concept and direct path measuring systems that achieves the precision demanded. The vertical machines from the NVX series expand on this with their excellent stability and damping with slideways in all axes. The speedMASTER® spindle with integrated cooling reaches a rotational speed of 15,000 rpm.
The 5-axis machining centres from DMG MORI master the most complex geometries. The range of products extends from the universal DMU monoBLOCK series with swivel rotary table, maximum automation options and up to 2,000-kg table loading capacity through the dynamic DMU eVo linear models with rapid traversing speeds of up to 80 m/min up to high-speed milling on the HSC 20 linear and their big sister machines. Speeds of up to 60.000 rpmhere guarantee the optimal surface quality that is demanded in die and mold making.
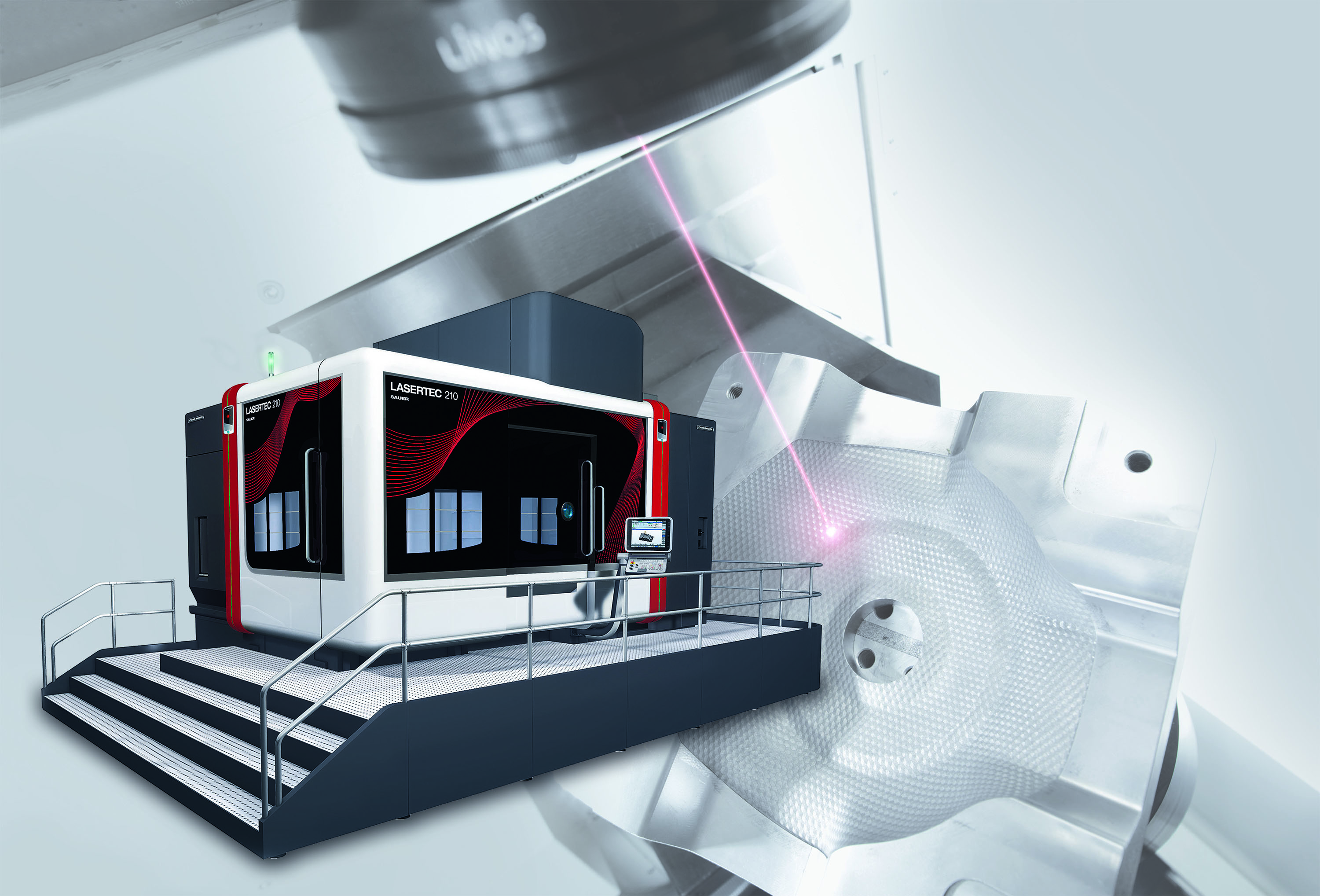
Picture: DMG MORI
“As a single-source provider, we provide services for the entire range of components used in the industry – from the smallest electrodes up to XXL components”, notes Markus Piber. This is why the successful DMU 600 G linear is primarily installed for large part machining in the area of die and mold making. With the DMU 340 Gantry, the XXL machines gain a little sister model just in time for the EMO, which effectively extends the product palette here to cover a whole range of different sizes of components.Its work area measures 3,400 x 2,800 x 1,250 mm with expansion options of up to 6,000 mm in the X-axis and 1,500 mm in the Z-axis. Thanks to the gantry design, the DMU 340 Gantry also offers a compact footprint. With the DMU 200 Gantry, DMG MORI will round off the Gantry series at the EMO. 5-axis machining with up to 30,000 rpm and optional ULTRASONIC or LASERTEC technology integration will also enable complex components up to a weight of 10,000 kg made of aluminium or composites to be economically machined. “Especially the ratio of the large working space of 2 x 2 m to the installation area of less than 24 m² has also impressed our customers”, explains Markus Rehm, Managing Director of DECKEL MAHO Seebach. The XXL portfolio also includes the DMU 600 P for workpieces up to 3,000 x 6,000 mm and 40,000 kg. But also the smaller DMU 210 P and DMU 340 P, in the 3-axis as well as the 5-axis models enjoy great popularity in the car industry for the production of fittings.
DMG MORI round off their range of products for die and mold applications with the machining centres from the DMU monoBLOCK and DMU duoBLOCK series. The DMU 125 monoBLOCK with space for workpieces up to 1,600 mm long and up to 6,000 kg in weight in the 3-axis variant is thus a popular model positioned between the smaller machining centres and the large gantry models. Markus Piber comments on DMG MORI’s advanced technologies: “We have set new standards in the mold-making sector with the innovative LASERTEC Shape technology.” The laser texturing of geometrically defined surfaces is more environmentally friendly than etching and offers enormous design freedom in addition to the highest repeat accuracy. “Also here we are able to accommodate all the relevant component sizes with the LASERTEC 45 Shape to LASERTEC 210 Shape range.”
The future of die and mold making
“The highly-accurate machines are naturally a decisive factor for competing on a global scale”, understands Markus Piber. Intelligent automation solutions and innovative technology cycles are also just as important: “And the Die & Mold Excellence Center allows us to complement the entire integrated production process.” Pallet changers, pallet rotary storage and linear pallet pools are the bread and butter of automation. But features to support the process are also in high demand like never before. This includes immediate tool measurement in the work area or DMG MORI technology cycles such as the Application Tuning Cycle (ATC). This adjusts the feed rate of the respective table load, reduces processing time and maximises the component quality.
DMG MORI paves the way into the digital future of die and mold making with CELOS. Aided by CELOS APPs, the integrated user interface installed in all new high-tech machines simplifies integrated management, documentation and visualization of order, process and machine data. In the area of die and molds, Markus Piber has a clear goal: “Our product and performance range offers the customer maximum flexibility and provides them with the capability to keep pace with the innovation speed of their customers.”
The right machine for every die and mold requirement:
- Innovative manufacturing concepts thanks to many years of experience in die and mold making
- An integrated machine portfolio for individual processing solutions in the automobile industry and the area of consumer goods
- Complete process chain for die and mold making
- Machine solutions for all component sizes
- HSC milling with up to 60,000 rpm for optimal surface quality
- Comprehensive XXL range up to 40,000 kg workpiece weight
- Maximum performance in 3-axis vertical machining
- 5-axis universal vertical machining with maximum stability, precision and dynamics
- LASERTEC Shape for laser texturing of geometrically defined surfaces