Dormer Pramet India – Vision 2023
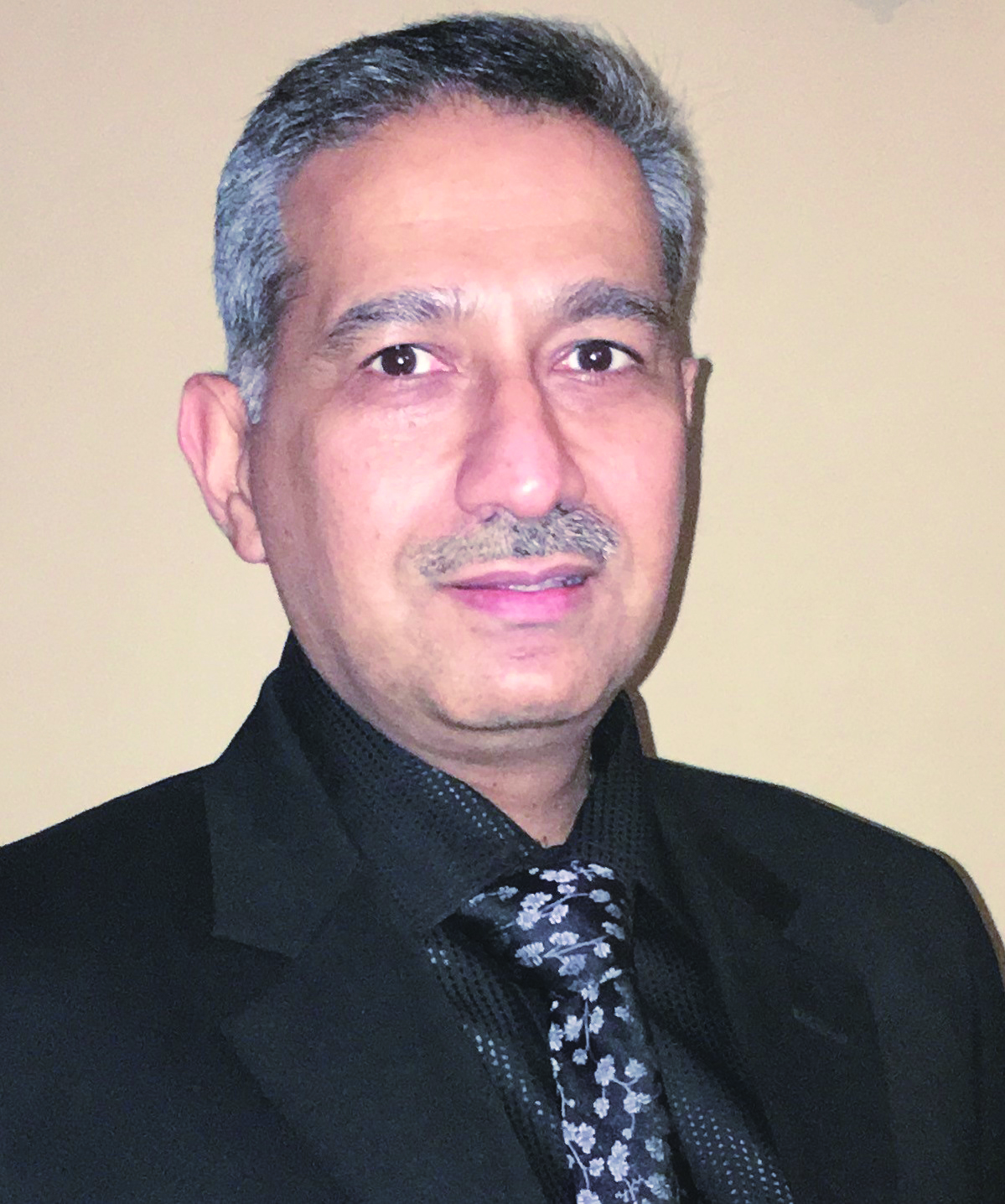
Gautam Ahuja, Managing Director of Dormer Pramet India shares with us his top predictions for the global manufacturing industry, the company’s growth statement, bestsellers and use cases.
Dormer Pramet is the result of a merger in 2014 between rotary tooling manufacturer Dormer and indexable specialist Pramet.
With 20 offices worldwide serving over 100 countries, production facilities in Europe and South America and a highly developed logistics network, the company offers truly global coverage.
The company aims to be the leading global supplier of metal cutting tools to the general engineering industry by 2020.
Top Predictions
The concept of Industry 4.0 is the most talked about topic in the manufacturing community today. Technology is making an impact on every step of the manufacturing process.
The most powerful levers manufacturers can pull will come in the form of robotics, Artificial Intelligence (AI) and the ‘Internet of Things’. Rich data and smart robotics will maximize a factory’s output, while minimizing cost and defects.
At Dormer Pramet we see Industry 4.0 as a big opportunity which can positively affect our production indicators and bring a competitive advantage.
Our path to “Smart factories” has been started at production sites in the Czech Republic, Brazil and India. Some important projects involving the use of robots and automation have already begun.
There is no single concept on how to implement Industry 4.0. It will be a learning process and our aim is not to spend huge amounts of money, but to be smart and use available tools with the highest impact.
In some cases, it can be just smart usage of Office 365 software by operators on the shop floor for better communications between shifts. In other areas, it will require investment, people training and more extended projects supported by external partners.
It will be an interesting and challenging journey to adopt new technologies in our production process. It is clear we can enrich our fantastic technical capabilities at both sites with deeper knowledge of digital. This will bring new opportunities and improvements.
Also, there is a strong trend towards digitalization of sales throughout the industrial B2B (Business to Business) market and more and more of our distributors are now moving their sales online.
At Dormer Pramet, we actively support distributors by providing important product data and media support documents (pictures and videos) to increase their business opportunities and help them sell our tools online. E-commerce is impacting on many areas of our industry and this activity forms an important part of our long-term strategy.
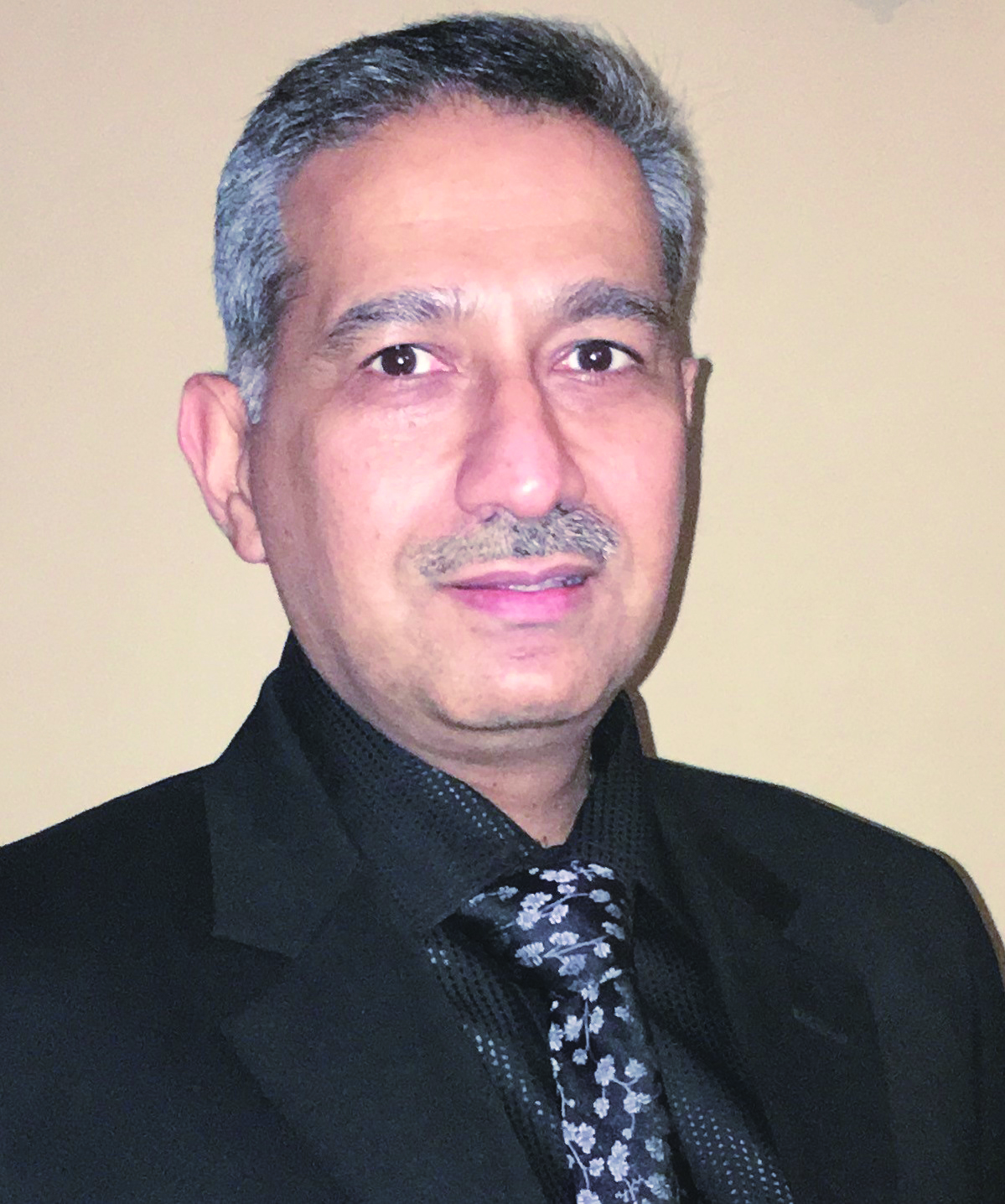
Managing Director
Dormer Pramet India
VISION 2023: GROWTH STATEMENT
Dormer Pramet is celebrating 10 years in India with continued sales growth. Gautam Ahuja, managing director of Dormer Pramet India, said: “Since being established in 2008, Dormer Pramet has developed to become one of the fastest growing cutting tool companies in the country, with an annual growth rate of 30% year on year. This is in line with our ‘Growth Vision’. Our Pramet and Dormer brands have built a good reputation within India and our team is working hard to develop this further with a wide range of customers in segments such as mold and die, railway, general engineering and heavy machining.”
BESTSELLERS
Force X: Dormer Pramet’s Force X family of solid carbide drills cover drilling depths from 3 – 8xD in almost all engineering materials.
All feature the unique Continuously Thinned Web (CTW) technology which provides a very strong web design, reducing thrust requirements during drilling. This has the dual benefit of improving both performance and tool life.
Force AD: The Force AD universal 90°milling cutter works with a broad program of inserts offering improved stability in a wide range of applications.
Combining solid performance with the ability to support ramping, helical interpolation and plunging operations in multiple materials, the Force AD assortment is ideally suited to general engineering and sub-contract environments.
Shark Line taps: Dormer Pramet’s range of taps for material specific applications – branded Shark Line – provide high performance and process security. All Shark Taps feature a colored ring that signifies the specific material type it is suited to. Manufactured from a powder metallurgy material, the taps offer improved toughness and tool life compared to High Speed Steels. Also, advanced geometry significantly reduces axial forces and torque, ensuring problem free threading.
BNGX high feed milling: Dormer Pramet’s versatile SBN10 cutters offer a highly cost effective option for machining a wide variety of materials and applications. Its unique pocket design can also carry inserts for shoulder and face milling, offering a complete package formold and die applications, from roughing to finishing.
These are supported by a new assortment of BNGX10 inserts for high feed roughing. The patented double-sided insert has four cutting edges and offers a smoother cut with an axial depth of up to 1mm.
Penta HF: Pramet’s high feed Penta HF cutter offers a highly versatile and simplified milling option for multiple applications. Designed primarily for high metal removal operations, the Penta HF is suitable for machining a wide variety of materials, including corrosion-resistant steels, difficult-to-machine steels and heat-treated steels.
The cutter features a 19° entering angle, enabling a maximum feed per tooth of 3mm. By supporting faster feed rates, machining time is reduced. In addition, a special surface finish promotes increased corrosion resistance, as well as reduced wear and friction resistance.
CASE STUDIES
Brunvoll AS
Brunvoll AS is a global manufacturer of seaworthy motion systems with headquarters in Molde, Norway. The company has supplied more than 8,000 complete side propeller systems mounted on more than 5,000 different cruise ships, supply boats and navy vessels.
Brunvoll produces 350 tunnel thrusters a year, with each available in a variety of sizes, between three to ten feet in diameter and a single engine power between 150-4500hp.
Machining of the propeller can be extremely challenging due to the fragile and brittle nature of the nickel-aluminium bronze alloy. This demands a highly accurate and dependable manufacturing processes and cutting tools.
The Dormer Red Shark tap is primarily designed for use with steel alloys. Its versatility allows for it to be used in different dimensions and at different torque levels, for example, when threading the propeller at the attachment to the rotor.
Red Shark increases tapping ability and service life, providing users with reliability and tool economy at high cutting speeds.
To ensure optimal productivity and safety, the unmanned machines are lowered to cutting speed of 82 feet/minute. The ideal cutting speed in the nickel-aluminium bronze was 115 foot/minute. In tests, Brunvoll successfully ran the Red Shark up to 164 foot/minute – exactly double the required rate.
Brunvoll were so confident of the tap’s reliability and performance, that most of the machining is now conducted unmanned and at night.
Besides the additional productivity of the Red Shark, it offers the flexibility to be used with more materials other than steel alloy.
Robert Nyblad GmbH
Robert Nyblad GmbH is a mechanical production specialist based in Papenburg, Germany, which provides components to the wind power industry. The company creates large component parts with a unit weight of up to 120-tonnes, as well as a revolution diameter of up to 6.9m.
Nyblad’s challenge involved a heavy duty casting application, machining a 20-tonnescast iron rotor shaft which forms the drivetrain in conjunction with the turbines and generator.
Edgar Sölbrandt, technical advisor at Dormer Pramet, provided support by suggestingthe robust Pramet insert CNMM with OR chip breaker and T9315 grade.
Edgar said: “Our insert CNMM 250924E-OR was originally designed for steel turning, but it is also suitable for the casting processing, due to its robustness. The combination of the T9315 grade with the OR chip breaker was ideal for stable machining in heavy cutting conditions.
“The challenge was to achieve identical cutting parameters and low noise. The T9315 proved to be so resistant that the noise level noticeably decreased. Also, the chip volume when roughing the shaft was enormous. The raw part initially weighed 20-tonnes; the finished rotor shaft weighed only 11-tonnes. A total of 9-tonnes worth of chips!
“We needed to be able to dispose of the chips safely from the work area, with up to one ton of waste per hour. Due to the dry machining process available with the Pramet insert, an open machine can be used and the working area offered enough space to cope with such a large chip evacuation.”
Helmer Schoolmann, head of mechanical manufacturing at Nyblad, added: “Even with the first tests of the Pramet insert, we instantly noticed more stable cutting conditions and high chip volume. We knew this was not a light machining operation, but we did not expect this high level of durability, especially after the initial tests we’d had with other manufacturers.”