Electrifying India’s Construction Equipment Sector: A Pathway to Sustainable Growth
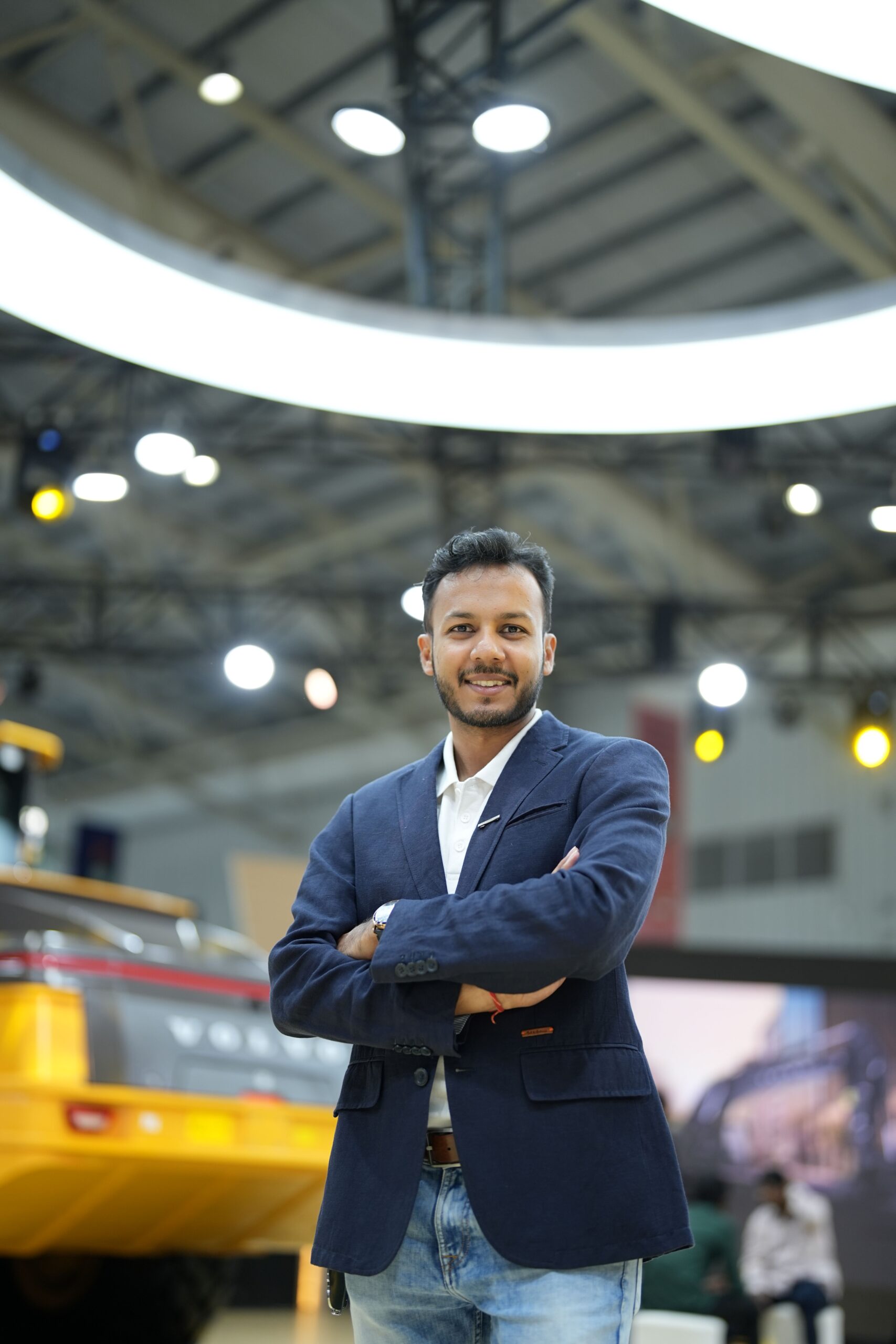
Leveraging Global Trends and Policy Imperatives to Propel Electrification in India’s Construction Equipment Industry
India holds the distinguished position of being the world’s third-largest market for construction equipment (CE), trailing closely behind China and the United States. Remarkably, projections suggest that by 2027, India will ascend to the second spot, surpassing the United States. This accolade encompasses a vast array of CE categories, spanning from pavers, compactors, and pneumatic rollers to earthmoving equipment such as cranes, forklifts, mining dump trucks, loaders, and backhoe loaders.
Traditionally, CE machinery has been synonymous with diesel consumption, devouring an impressive 50,000 liters per day in standard mining operations. The sheer scale of emissions generated underscores the urgency to transition towards cleaner energy sources. Despite the automotive sector’s strides in electrification, the Indian CE landscape remains predominantly reliant on diesel power. However, a paradigm shift is underway, with stakeholders increasingly recognizing the manifold benefits of electrification, including enhanced operational efficiency and a substantial reduction in operating costs, estimated at 40-60% compared to internal combustion engine equipment.
Internationally, both the European Union (EU) and China have emerged as vanguards in driving CE electrification, enacting a comprehensive suite of incentives and policy reforms. Notably, Norway has pioneered the provision of subsidies, effectively reducing the price disparity between electric and engine-powered machinery by a notable 40%. Concurrently, the Netherlands has allocated a substantial budget of €270 million (INR 2,432 crore) for the procurement or retrofitting of zero-emission construction machinery under the Clean and Emission-Free Construction Material Subsidy Scheme (SSEB).
Furthermore, regulatory imperatives in locales such as Oslo and China are catalyzing the adoption of zero-emission construction equipment, with the former mandating that public construction work be emissions-free by 2025, followed by general construction work by 2030. Shenzhen, as an exemplar, incentivizes electric forklifts through its “Shenzhen Blue” Sustainable Action Plan, offering generous subsidies of up to RMB 800 (~INR 9,363) per kilowatt-hour, with a maximum cap of RMB 40,000 (~INR 4,68,143) per forklift. The tangible outcome of such initiatives is palpable, with China achieving the sale of approximately 4,000 electric CE units in 2022 alone.
These global precedents serve as poignant reminders of the imperative for analogous incentives within India’s CE landscape. With the imminent rollout of FAME-III and discussions surrounding innovative vehicle form factors such as E-Tractors, the case for incentivizing the CE sector becomes increasingly compelling. Moreover, the allocation of INR 2,671 crore in the interim budget for 2024-25 underscores the government’s unwavering commitment to fostering initiatives like FAME.
In catalyzing the electrification of the CE industry, policymakers possess an array of levers at their disposal under the FAME scheme. These include incentivizing CE machinery and charging infrastructure, rationalizing GST rates to parity with other electric vehicles, waiving off-road tax and registration costs, and instituting grants to bolster R&D efforts for domestic and export markets. Additionally, government entities responsible for infrastructure tenders can play a pivotal role by mandating the incorporation of electric machines within projects.
The implementation of these strategic recommendations dovetails seamlessly with the government’s overarching objective of fortifying the EV ecosystem, as underscored in the interim budget. It is through such concerted measures that we can chart a course towards renewed support for the entire EV value chain, including vital assistance to the CE industry.
Authored By
Mr Yuvraj Sarda
Head – EMob Solutions
Volvo CE India