Formnext: TRUMPF presents new solutions for latest trends in 3D printing industry
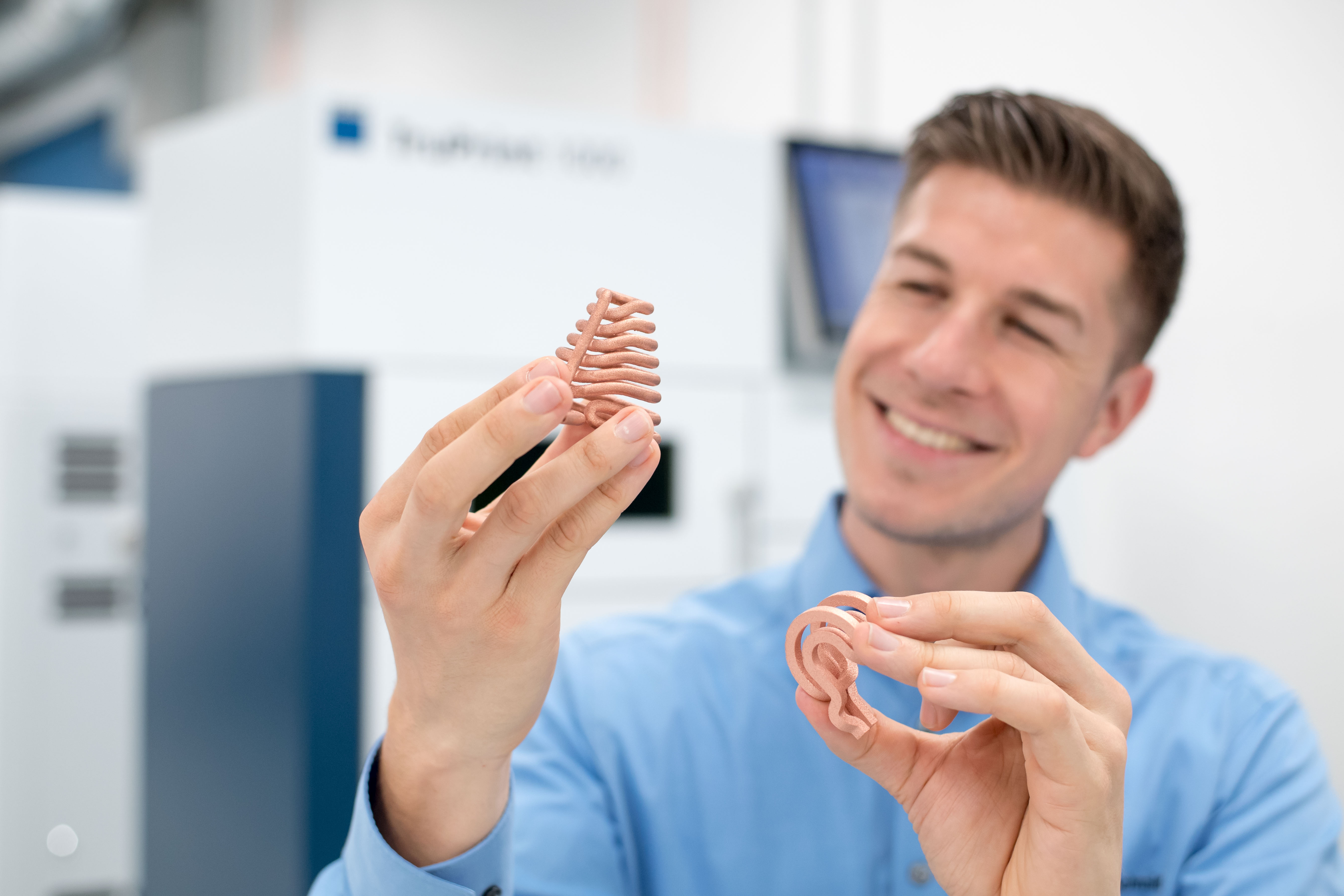
Green laser opens up new industrial applications with 3D printing of pure copper and precious metals
Ditzingen, November 10, 2020 – High-technology company TRUMPF is increasing automation and process speeds in its additive manufacturing technologies – and its “green laser” is fueling new applications by enabling 3D printing of pure copper and precious metals. At this year’s formnext Connect virtual trade fair, the 3D printing and laser specialists are showcasing new solutions for three key industry trends: speed, automation and new materials. As well as new products, these solutions also include successful new applications for fast-growing sectors.
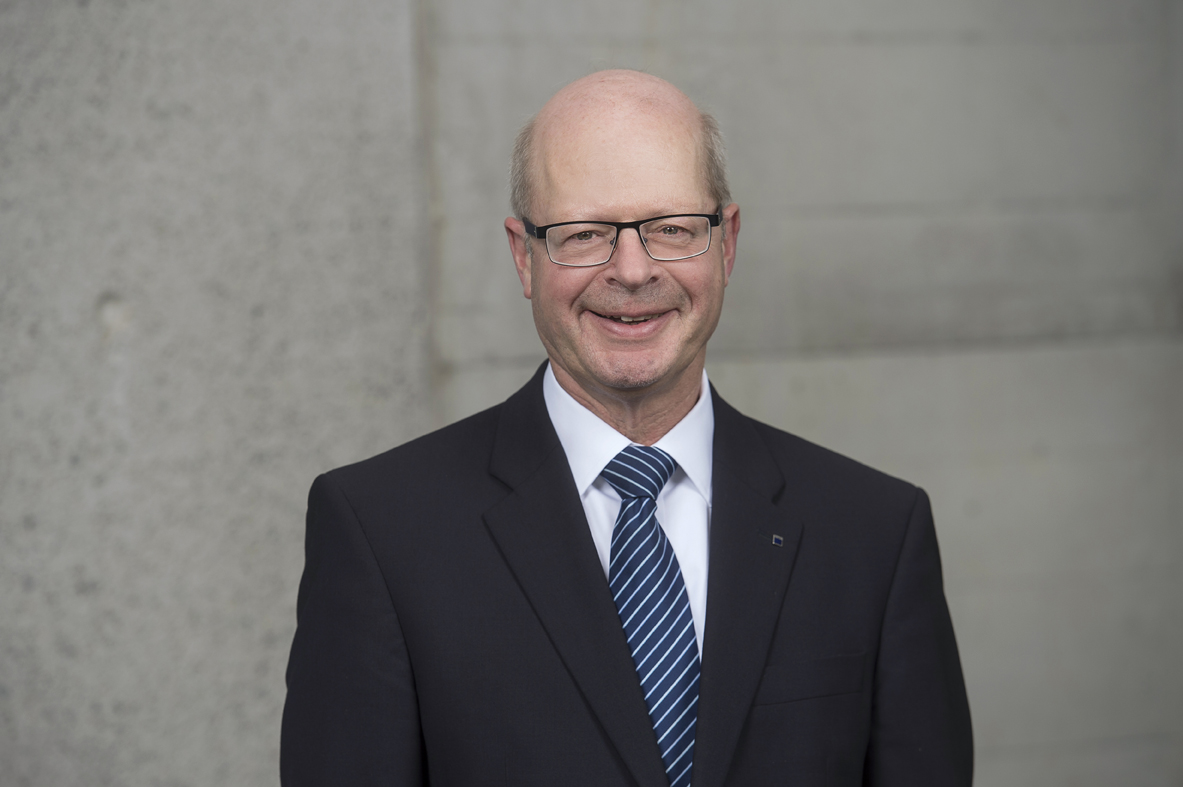
“Our TruPrint 1000 Green Edition with a green laser beam source has achieved huge success in industrial applications.”
“The additive technologies market remains very attractive for TRUMPF,” says Klaus Parey, managing director TRUMPF Additive Manufacturing. “Customers are particularly excited by our TruPrint 1000 machine with a green laser beam source, which is designed for industrial use. Short-wavelength green laser light is the best option for welding pure copper and precious metals.” TRUMPF has made major progress in its products and solutions for additive technologies over recent months, building up a broad portfolio of products that can handle a wide variety of materials.
Process speed: new nozzle doubles coating rate
Coatings to protect against wear and corrosion are often used on parts such as brake disks, hydraulic cylinders and gaskets. The metallic coatings are applied using laser metal deposition (LMD), which has proved to be an excellent choice over many years. LMD produces high-quality coatings that are almost completely crack-free and non-porous. Using the standard LMD method, the processing rate per unit area – in other words the speed at which the coating can be applied – typically lies between 10 and 50 square centimeters a minute. The high-speed Press Release page 2 of 4 variant of LMD, also known as EHLA, can currently reach speeds of between 250 and 500 square centimeters a minute in industrial settings. But now TRUMPF has developed a new nozzle technology that increases the coating speed to well over 600 square centimeters a minute, even reaching speeds as high as 1,000 square centimeters a minute in certain applications. The secret lies in using more powder, higher laser power and a nozzle designed specifically for industrial use. Applying a coating faster obviously means using more powder. But using more powder only works if it can be melted fast enough. That’s where the second ingredient in the mix comes in: higher laser powers of up to 8 kilowatts. Yet these high laser powers can only be used in tandem with a robust, properly cooled nozzle. And it’s exactly this combination that TRUMPF has brought together in its new nozzle technology, which enables significantly higher coating speeds than ever before – especially for rotationally symmetrical parts.
Automation: new depowdering station gets parts cleaner
To boost the productivity of additive manufacturing even further, TRUMPF is working hard to find ways of improving upstream and downstream work steps in the overall process chain. At formnext, the company will be showcasing a new depowdering station for the powder bed-based additive manufacturing process of laser metal fusion (LMF). This system unpacks and depowders 3D-printed metal parts, combining two process steps in one machine. Previously these steps had to be carried out manually by a machine operator using suction nozzles and brushes. But the new depowdering station makes these steps considerably simpler by introducing a degree of automation. The system turns the printed part upside down and, if necessary, starts to vibrate, until almost all the excess powder has been removed. This new depowdering process does a considerably better job of removing excess powder from the finished part. What’s more, it protects the machine operator from hazardous particles by carrying out powder removal in the process chamber while it is still flooded with inert gas.
Diverse materials: green light for copper, gold and platinum
At the formnext fair held two years ago, TRUMPF demonstrated for the first time how a disk laser in the green wavelength range can be used to print pure copper and precious metals. Conventional 3D printers that use infrared light can’t handle materials such as copper and gold, because their highly reflective surfaces prevent melting from taking place. But because green light has a much shorter wavelength than infrared, it opens the door to 3D printing of pure copper and precious metals. Since its launch, TRUMPF’s TruPrint 1000 Green Edition has carved out a solid position in the market and enjoyed tremendous success. Satisfied customers include toolcraft, which is using the machine to produce parts for various industries, and the company C. Hafner, which uses it to make watch cases out of red gold and platinum. TRUMPF’s “green printers” are also a popular tool at Fraunhofer IWS, where several institutes are putting the TruPrint 1000 Green Edition to use in various fields of research.
For More Information Visit – https://www.trumpf.com/en_IN/