Hiring for the factory of the future
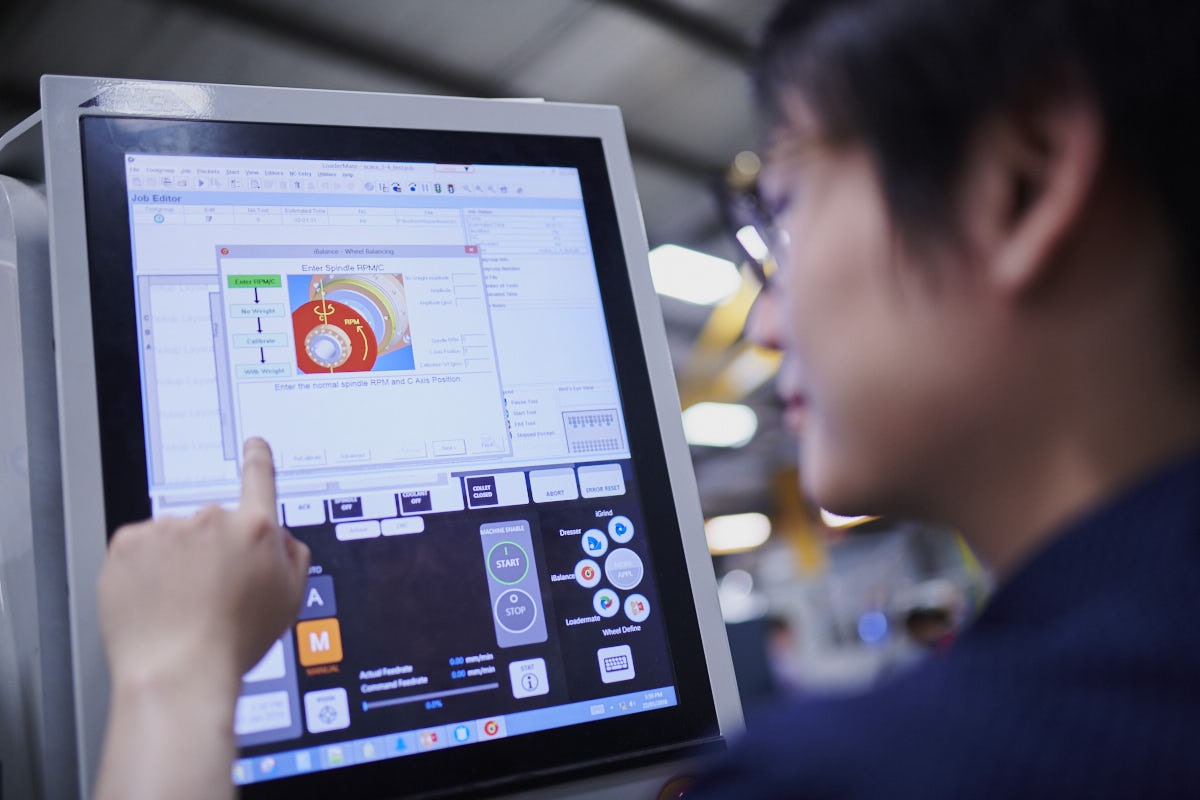
Hiring for the factory of the future
Written by Simon Richardson ANCA Product Manager
In the factory of the future, technology will of course be key. Factories will integrate networked machines, sensors and advanced robotics IT systems into existing processes. They will thrive on data, real-time figures and unprecedented access to information to be more efficient, less wasteful and better connected.
As your operations are transformed, you will need a workforce that knows how to take your business into the future time and time again. This means rethinking how your hire, and how you upskill existing staff. This doesn’t have to mean starting from scratch. You may be well on your way to a great future workforce already.
The skills you need are changing
You may already be using technology to move forward. As factories shift to a future focus, they are adapting what’s already available – like the cloud, robotics and in-process measurement. This brings with it new skill requirements.
Knowing how to use these tools to their full potential means having a team of critical thinkers. The FoF will require a workforce that’s computer savvy and driven by problem solving. Staff will need to be analytical, knowing how to use data to continuously improve.
Teams should incorporate good software development skills and programmable logic controls experience. You will need people who can network machines and those who are able to capitalise on the immense value of automation. With the speed of the tooling industry increasing, they will need to become their own innovation hub, constantly looking for opportunities to grow and improve through technology.
How to hire for the factory of the future
People working in factories of the future will need to be more fluid. They will have to think cross-functionally and collaborate to make the most of their complementary skills. Much like a software programming team, these workforces will need an agile mindset, be open to new approaches and ready to adapt to work better, harder, smarter.
Finding and hiring these people will mean understanding what’s involved in their different roles. You will likely find you need to fill a mix of existing and new positions, some of which you might not have come across before.
Look for staff with a STEM – science, technology, engineering and mathematics – background – they are more and more likely to be university graduates. But their education should only be a starting point. Look for applicants who demonstrate lateral thinking and problem-solving skills, signals that they can put their technical background into practical use.
Existing roles are evolving. Machinist skills such as operation monitoring, systems evaluation and quality control analysis can be applied to new systems. Tool and die makers can use their technology design and operations analysis background to build better processes and create new tools. New roles will also appear: robotics engineers, automation engineers, and roles that combine elements of both.
Positions will also be created for people to bring new ideas into the business. Factories may start hiring senior IT staff such as a CTO or CIO. These tech leaders will become champions of innovation – sourcing, internally promoting and working to implement the very best for the factory.
In such a new field, having their authority on hand to assist with interviews can be a game-changer. Senior tech staff will have the right knowledge to spot candidates who can apply their expertise to your business. You may also be able to leverage specialised recruitment agencies that can make sure you’re only interviewing people who can bring the right combination of technical nous and creativity.
When you’ve got the right team – nurture it
In the factory of the future the focus is shifting from working the production line to building a better one. Automation and robotics have changed the way the factory floor looks, and those changes will keep coming.
Just as with technology, setting yourself up with the right people doesn’t have to mean starting all over again. As long as you have clarity around where you’re going and how, you will give yourself the best chance to identify potential in your existing workforce.
Factor in training. Most businesses will need a training officer, not only to train staff on the existing production methods but to bring them on board with new operations.
Support your people to work together. A collaborative, agile approach should apply across the whole business, from learning how to use existing equipment to working together to implement new products. A team of champions will work side-by-side to make sure every element of operation is adding value and working to its full capability.
Engage your staff. Use your trainers and tech champions to communicate the vision and future of the factory. Motivate them to feel excited about the future by offering clarity and direction.
With competition increasing, the most important thing in the factory of the future is to retain skilled people. The next generation is demonstrating more of these diverse, flexible skills, but increasing demand means there is a global skills shortage. Finding and keeping good staff will make your workforce more efficient and save on hiring and training costs.
Giving staff members opportunities to try out new tasks, upskill in their existing roles, undertake further education and create ownership of the factory’s direction will all help to strengthen their loyalty to the business.
Give your team the tools to perform
Having the best brains in the business won’t mean anything without the best tools. A team with great problem-solving skills can work together with machine manufacturers to create custom systems for the best output. The combination of analytical minds and high-level engineering means a flexible, adaptable system with endless potential.
Supported by internal champions, new products can be implemented with enthusiasm and real buy-in from your workforce. That means continuous improvement with a loyal team as your factory moves ever further into the future.