How to Protect Industrial Machinery Against Corrosion
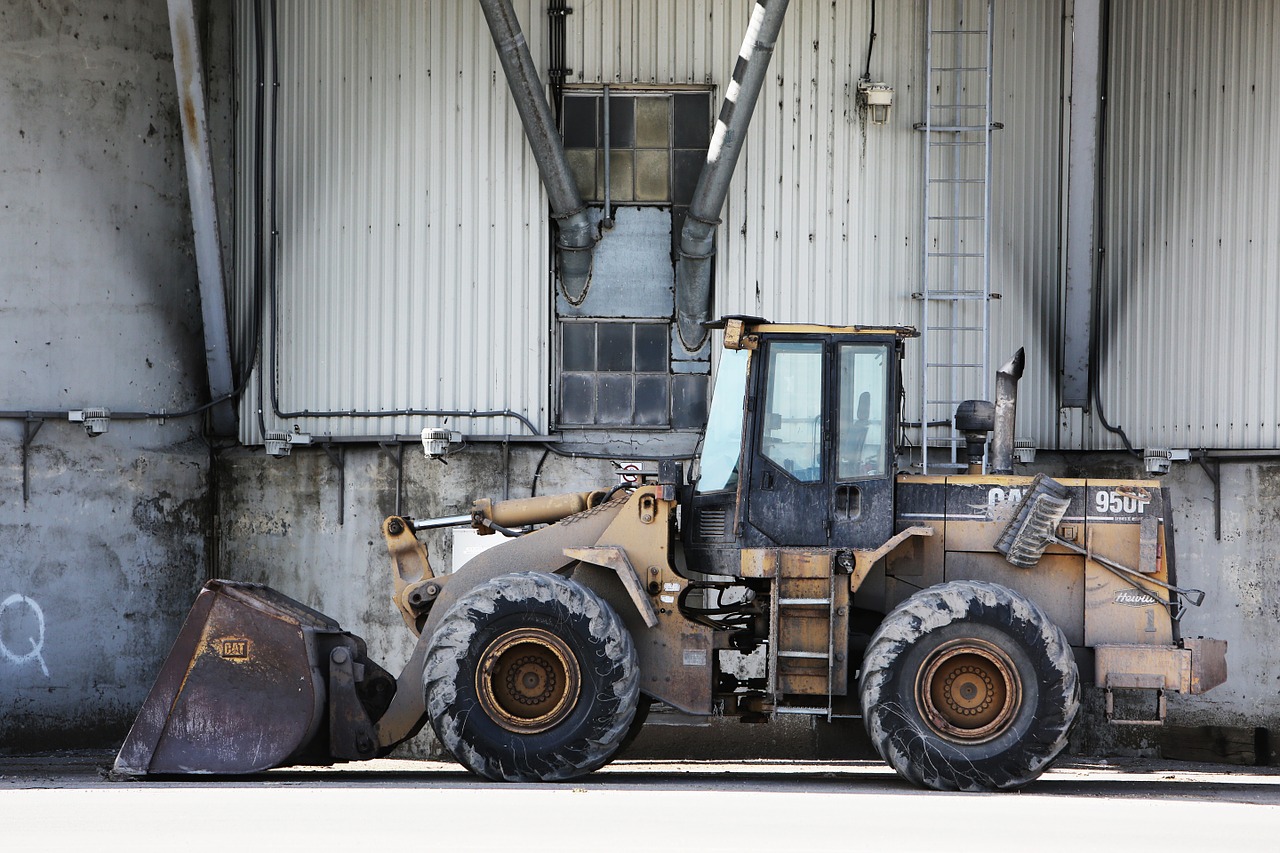
Corrosion Costs The Country
In 2002, the U.S. Federal Highway Administration (FHWA) conducted a study whose findings remain relevant today. After studying the problem, the FHWA concluded that corrosion costs the country around $276 billion every year. That’s 3.1% of the country’s GDP.
The problem has only worsened in the intervening years, especially from the FHWA’s perspective. The generally poor condition of American infrastructure is something of a perennial crisis, with corrosion, climate change and faltering tax revenue as the top-cited reasons.
Highways and other infrastructure are one facet of this expensive problem. Industrial machinery is another. The FHWA study identified petroleum refining, chemical production, agriculture, food processing, electronics, energy and pipelines as particularly susceptible to the effects — and expenses — of corrosion over time.
Corrosion-related costs were difficult to estimate for some of these industries. For others, the cost per year for corrosion mitigation and corrosion-related productivity shortfalls are eye-opening.
- Automotive manufacturing: $23.4 billion
- Food processing: $2.1 billion
- Petroleum refining: $1.8 billion
Industrial and consumer equipment needs proper protection from the inconvenient and expensive problem of corrosion. There’s a lot of money tied up in solving the symptoms of rust and corrosion. It’s money that could be much more useful elsewhere. But where to begin slowing down the actual causes behind it?
Care and Environment
Remaining mindful of the environment in which our industrial equipment operates can go a long way toward keeping corrosion at bay. The same thing is true of timely maintenance interventions.
If you want to keep the effects of harsh environments and inadequate equipment handling from speeding up corrosion in your equipment, here’s what you need to know.
1. Proactive and Predictive Maintenance
The Internet of Things (IoT) is a boon in pipeline and drilling operations, as well as any other industry where heading off corrosion is a top concern for productivity, throughput and consistent product quality. IoT sensors can detect early signs of corrosion — a major source of failure in pipelines worldwide.
Timely interventions for failing parts, before they break down or contaminate the product, can significantly impact the performance and expected lifetime of critical industrial machinery. That’s without accounting for the company’s reputational damage if corrosion compromises a production line.
2. Proper Storage
It’s hard to understate the value of proper and ongoing training in areas like equipment storage, handling and maintenance.
Early on, employees should familiarize themselves with the effects of corrosive elements like water and salty air. Moreover, each piece of equipment should have a known, intuitive and protected “home” out of the weather where workers can stow and and maintain it as needed after each use.
3. After-Use Care
Likewise, it’s impossible to exaggerate the importance of taking a few moments to care for equipment after it has gone through its paces for the day.
Wiping down industrial equipment after each use goes a long way. The accumulated moisture, chemicals, debris and other contaminants after typical jobs are often more than enough to kick-start the oxidation process that leads to rust and equipment failure.
Anti-Corrosion Coatings and Paints
Equipment manufacturers and owners have some options for applying coatings that slow down the oxidation process.
Although salty air and water may be the first culprits that come to mind when you think of corrosion, simple UV exposure is frequently enough to cause severe weathering and corrosion on industrial structures and equipment. Apart from the poor aesthetics, this wear and tear also takes potential years off the expected lifetime of critical equipment or work surfaces.
Here are some general recommendations for choosing a restorative and protective anti-corrosion coating or paint.
4. Properly Prepare the Surface
The first step in applying an anti-corrosion primer or coating is to prepare the surface.
Remove existing rust, contaminants, debris and calcified solids from the workpiece. You’ll want your primer or coating to adhere as closely to the workpiece as possible, to as smooth a surface as possible, so corrosion can’t set in again underneath the newly restored surface.
5. Choose a Primer or Coating Product
From there, protecting work surfaces, or the exterior of equipment housing or outbuildings, is a matter of choosing an appropriate primer. Epoxies are an excellent choice, but not necessarily for outdoor equipment, as they don’t age as well as other products. Thin-film urethanes are a better option for a wider range of applications, including outdoor tools and equipment.
Equipment Design
Sometimes, protecting an industrial building or piece of equipment takes more than a well-chosen paint or primer. It often involves incorporating anti-corrosion features into the very structure or engineering of the piece in question. Here’s a couple of options to consider.
6. Sacrificial Metals
One common way to stave off corrosion in submerged surfaces — like ship hulls and the interior of chemical or water holding tanks — is to incorporate blocks of sacrificial metals. The presence of zinc or magnesium attracts corrosion instead of steel, for example, and helps prolong the life of the vehicle or equipment.
7. Impressed Current
The proximate cause of corrosion is a current-conducting medium between a corrodible and a “protected” metal. Adding an impressed current can negate this effect by introducing an equal-strength, opposite-direction current. This principle applies most readily to pipelines and submerged tanks, and the engineering can be intensive.
8. Upscale Materials
OEMs have a decision to make when it comes to the build materials they select for their handheld or industrial tools. Purchasing agents and fleet managers have a choice when the time comes to buy, too.
Premium equipment is such, in part, because of the materials selected during design and assembly. For tools like pumps and similar assets that you don’t want to have to replace regularly, engineers recommend avoiding low-carbon steel and cast iron in the structure.
Manufacturers who build for longevity gravitate toward stainless steel by default over these lower-quality, more corrosion-prone choices. Buying budget equipment might make sense on day one, but it could have an unpleasant after-effect.
Preventing Corrosion in Industrial Equipment
With these fundamentals in mind, it’s possible to design and operate equipment in a way that keeps corrosion away for as long as possible. Rust and other elemental degradation are facts of life, but the appropriate precautions help stretch equipment and maintenance budgets further while keeping product quality high and downtime low.
Many of the techniques described here are ideal for maintaining the usefulness of legacy equipment and performing value-maintaining refurbishments for fleets, rather than replacing outright. These refurbished assets may continue to prove useful, or selling them could become a secondary revenue stream.
Ultimately, remaining mindful of corrosion opens doors to profitability and continued productivity.
Author
Martin Banks is the founder and Editor-in-Chief of Modded. He covers the world of tech, gear, and more.