Importance of Electrical safety in E mobility
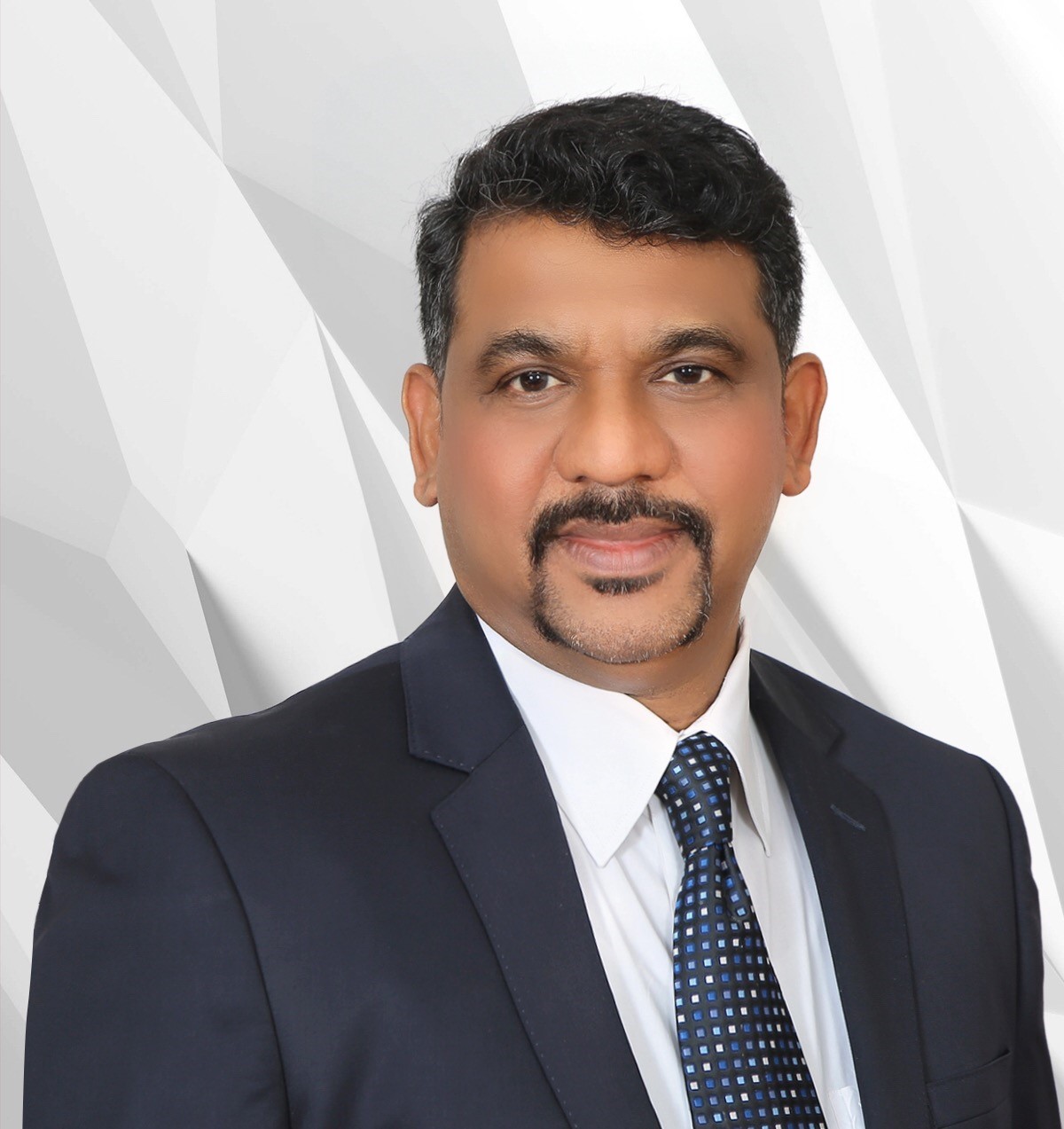
“Transforming Perspectives: The Evolution of Electrical Safety Monitoring Solutions in India”
In India electrical safety monitoring solution in electrical systems in general was always an option and add-on suiting the budget. It was not an integral part of electrical systems design and was at the mercy of mandatory regulations and legislations. It was and is in many instances considered as an additional cost and kept in abeyance. However, with exposure to global quality requirements, international industrial standard recommendations and with experience in real life electrical hazards and accidents there is a change in attitude and perception. Further complexity in design calls for inclusion of electrical safety monitoring solutions as an integral part of electrical systems design, installation and maintenance. eMobility ecosystem which includes eVehicles and charging infrastructure including storage batteries by its intrinsic electrical power use come under the purview of requirement of mandatory reliable electrical safety solution for asset and human safety.
Importance of electrical safety in e-mobility
Electrical safety is crucial in e-mobility because electric vehicles (EVs) are powered by high-voltage batteries and electric motors, which pose a potential electrical hazard to drivers, passengers, and maintenance personnel and loss of infrastructure property. Safety measures must be in place to prevent electric shock, fire, and other hazards associated with high-voltage systems. Also continuity of power supply is of utmost importance for ensuring availability of the system.
Electrical safety plays an important role in e-mobility:
• Battery safety: The high-voltage batteries used in EVs are potentially dangerous, and any damage or malfunction can cause a fire or explosion. Therefore, the battery must be designed, manufactured, and tested to ensure its safety. Additionally, proper installation, maintenance, and storage are necessary to prevent accidents.
• Charging safety: EV charging infrastructure requires proper installation design including grounding and protection from electrical faults. Safe charging stations must be installed in accordance with local regulations and international standards to avoid electric shock or fire.
• Vehicle safety: The high-voltage electrical system in an EV must be designed to prevent electric shock to occupants in the event of an accident. Further insulation faults and leakages may cause fires endangering the life of occupants and loss of asset. Safety features such as automatic disconnect of the battery in the event of a collision and monitoring of insulation of high-voltage components can help prevent accidents.
• Maintenance Safety: Maintenance personnel must be properly trained to handle high-voltage electrical systems, and safety protocols must be in place to prevent accidents during repairs or maintenance.
In summary, electrical safety is critical in e-mobility to ensure that EVs are safe for drivers, passengers, maintenance personnel, and the environment. Proper design, installation, and maintenance of high-voltage systems can help prevent accidents and ensure the safety of all stake holders.
e-Mobility Electrical Installation Design:
The electrical power system design with its ground/chassis referencing plays a crucial role in the inherent safety of EV and charging infrastructure. The type of ground referencing of electrical power source with respect to ground/chassis plays an important role in ensuring safety. There are 2 major types of grounding used in electrical installation. Grounded and Ungrounded. In grounded system the electrical power source reference pole is connected to ground/chassis. In an ungrounded system the electrical power source is not connected in any way to ground/chassis and totally floating and insulated from ground/chassis.
The use of ungrounded system is the cornerstone in the electrical design of e-Vehicle and charging infrastructure in eMobility ecosystem. Ungrounded electrical system if designed intelligently is inherently safe against electrical hazards namely electrical shock and fire. Further ungrounded system increases continuity and availability of electrical system. For encashing the benefit of ungrounded system the first insulation to ground fault should be monitored, detected and annunciate to user. For this function some form of high accuracy and sensitive online insulation leakage monitoring system should be deployed. IEC standards recommend the use of such insulation monitoring device for 24×7 monitoring of insulation in the eV and their chargers.
Which is the best insulation monitoring method in E vehicles?
There are several insulation monitoring methods used in electric vehicles (EVs) to ensure electrical safety. The best method for insulation monitoring in an EV depends on factors such as the type of vehicle, the electrical system, and the specific safety requirements.
Some commonly used insulation monitoring methods in EVs:
• Legacy cheap passive method – old passive method historically originated in telephone DC power distribution system and later spread into various electrical installations mostly DC supplies. It uses a voltage divider series resistance circuit connected across the 2 poles of power source with the midpoint connected to ground/chassis. The voltage unbalance between each pole with respect to ground is monitored for any insulation fault. However this passive method is not very accurate and sensitive to high resistance insulation faults for advance prediction and does not detect symmetrical faults. Further this passive measurement technology is susceptible to electrical noises and does not provide reliable and stable reading and causes spurious alarms. Not recommended by current IEC standards.
• Online insulation monitoring – online insulation monitoring continuously measures the insulation resistance of the electrical system and provides real-time information about the condition of the insulation. This active measurement method is more sophisticated and can detect high resistance faults earlier than passive insulation monitoring or any other method of Insulation monitoring. Further this Online insulation monitoring is commonly used in high-voltage systems where the consequences of insulation failure can be severe. Recommended by current IEC standards.
Is Online insulation monitoring better than passive insulation monitoring in e vehicles Online and passive insulation monitoring are two methods used in electric vehicles (EVs) to detect insulation faults and ensure electrical safety.
Passive insulation monitoring involves periodically measuring the insulation resistance in terms of unbalance voltage of the electrical system circuit with respect to ground and to detect any changes, which can indicate an insulation fault. However, in the case of symmetrical faults, this will not show any faults as the system is still balanced thereby leading to a potential hazard of electric shock, fire, and other associated hazards. This method is commonly used in low-voltage telephone electrical systems and pure AC/DC distribution system without any nonlinear loads and electrical noises and is relatively simple and inexpensive. Not reliable for predictive monitoring.
On the other hand, online insulation monitoring continuously measures the insulation resistance of the electrical system with respect to earth for both asymmetrical and symmetrical including high resistance faults and provides real-time information about the condition of the insulation. This is a widely used method in the European and US market considering the safety of man and machine.
Overall, the best method of insulation monitoring in EVs is online insulation monitoring as it takes care of all the electrical design and installation issues in modern nonlinear electrical systems with presence of high EMI/EMC noises. However, it is expensive compared to all others methods but worth its price considering human and asset safety. As per ARAI, the choice of method depends on the specific requirements of the vehicle’s electrical system and the level of electrical safety needed to be based on the voltage levels. However, in general with high voltage, it is desired to have online insulation monitoring taking into account human and asset safety.
What is the importance of Electrical safety in E mobility and its impact on man & machine?
Electrical safety is of utmost importance in E-mobility, as it directly impacts both man and machine. Here are a few reasons why:
• Protection of human life: Electric vehicles (EVs) and electric charging stations carry high-voltage electricity, which can be dangerous if not designed properly. In case of an electrical fault, this voltage can cause electric shock, burns, or even death. Proper safety measures need to be in place to prevent such accidents from happening.
• Protection of the vehicle: Electric vehicles and their components are sensitive to electrical faults, which can lead to damage to the vehicle’s battery, motor, or other electrical components. Proper safety measures ensure that these components are protected, preventing expensive repairs or replacements.
• Regulatory compliance: Many countries have specific safety standards that electric vehicles and charging stations must adhere to. Complying with these standards not only ensures safety but also helps manufacturers avoid legal liabilities and financial penalties.
• Public perception: Safety is a critical factor in building public trust in electric vehicles. Any accidents or incidents involving electric vehicles can damage the public perception of EVs and slow down their adoption.
Overall, electrical safety in E-mobility is crucial for protecting both human life and the vehicles themselves. By implementing proper safety measures, manufacturers can ensure the safety of their customers and build public trust in electric vehicles.
Benefits of using an Online insulation monitoring system
1. Early detection of insulation faults: Insulation faults can occur in the electrical components of E-vehicles, such as the battery or motor, and eV Chargers which can lead to unsafe conditions or component failure. Online insulation monitoring can detect these faults early on, allowing for timely repair or replacement before they cause further damage.
2. Improved safety: Insulation faults can create hazardous conditions for E-vehicle occupants and charger users and surrounding individuals. Early detection and resolution of these faults through online insulation monitoring can prevent accidents and increase overall safety.
3. Reduced maintenance costs: Insulation faults can cause costly repairs and replacements if left unaddressed. Online insulation monitoring can catch faults early on, reducing the need for extensive repairs or component replacements and lowering overall maintenance costs.
4. Increased vehicle efficiency: Insulation faults can cause electrical systems to operate less efficiently due to leakages, leading to reduced vehicle performance and range. Online insulation monitoring can identify and correct these faults, improving the efficiency of the vehicle and maximizing its range.
5. Fire safety: Insulation leakage and faults may initiate fire in case of short circuits endangering the life of occupants in eVehicles and protect against damage of eV. Similarly it will enhance fire safety of eVehicle chargers.
6. Data tracking and analysis: Online insulation monitoring systems can provide data on the insulation resistance and overall health of the electrical components of the vehicle. This data can be tracked and analysed over time, providing valuable insights into the performance and maintenance needs of the vehicle.
Overall, online insulation monitoring in E-vehicles and e-vehicle chargers can offer numerous benefits, including improved safety, reduced maintenance costs, and increased efficiency. By identifying insulation faults early on, E-vehicle owners can ensure their vehicles operate safely and efficiently over the long term.
Bender Solution in eMobility Space
E-Vehicle & PHEV Safety : Bender, Germany with its more than 80 years R&D in providing world class electric safety solutions has developed a card based Insulation Monitor IR155-3203/-3204 with special PWM signal communication technique to be installed in the EV DC system up to 1000VDC conforming to IEC standards and EMC qualified. Bender has also developed the insulation monitor iso165C with housing and CAN-Bus programming interface to be installed in EV for DC system up to 600 VDC and iso175C/P for DC system upto 1000 VDC conforming to IEC standards and automotive EMC qualified.
The above both models have insulation resistance measurement range of 0…50MΩ with adjustable response values about 100KΩ…1MΩ (IR155) respectively 30KΩ…2MΩ (iso165/iso175). All the above models are in conformance with IEC standards and EMC qualified suitable for working with 12VDC and 24VDC (IR155) respectively 12VDC (iso165) & upto 36VDC (iso175) supply voltage of the EV.
EV-Charging Supply System Safety: For AC Charging Residual Current Protective devices at least must be a RCD Type A having rated residual operating current trip level at AC 30mA.
Wherever a DC fault current is possible during charging of the EV, Residual Current Device Type B shall be used for disconnection in case of DC fault current exceeds 6mA. Alternatively, the more cost-effective combination of a RCD Type A and a special sensor for detecting a DC 6mA differential current can be used. Bender developed the Residual Current monitoring devices RCMB121 and RCMB104, which can be used for Mode-1, 2 and 3 EV Charging stations as the solution for DC residual fault current detection > 6mA. In addition the RCMB420EC can be used as a DIN-Rail solution for Mode-3 EV charging stations for DC residual fault current > 6mA.
In case of Mode-4 DC EV charging stations Insulation Monitoring Device isoCHA425+AGH-EV up to 1000VDC and measuring range 1KΩ…1MΩ meets the IEC 61851-23 requirements and conform to IEC 61557-8 for functionality.
Charge Controller CC613 and ICC1324 for AC Charging: Open Charge Point Protocol (OCPP) initially developed by Netherlands automotive association and similar to IEC 61850 TCP/IP protocol for distributed control of energy has now become a de-facto standard for communication between EV charging station and Central Management station worldwide. Bender with its early initiating effort has developed the Charge Controller CC613 which integrates safety functions for Mode 1, 2 & 3 charging stations and communication through OCPP-1.5 + 1.6 version (version 2.0 in preparation) to the Central Station’s backend. It also includes 4G modem for wireless communication.
The offer is about a highly integrated charge controller series consisting of DIN-Rail mounted CC612 and PCB based solutions called ICC1324. The charge controllers can manage the communication to the vehicle based on PLC communication according to ISO15118, PWM communication to the vehicle according to IEC 61851-22, can be updated over the air and provide a fully integrated RCMB functionality for the detection of DC 6mA differential current. Further all charge controller variants support an interoperable Dynamic Load Management to avoid imbalances at the local power supply.
Bender India is a subsidiary of Bender Group, Germany. Bender is a worldwide known technology expert and innovator of state of art Electrical Safety Solutions in terms of online condition monitoring of electrical power and distribution systems spanning various categories of industry and commercial establishments namely Power Generation & Distribution, e-Mobility, Oil & Gas, Mining, Shipping, Defense, Railways, Telecommunication, Process Industry, Hospitals &Medical Establishments, Core Manufacturing Industry covering Steel, Cement, etc.
List of references
Bender eMobility Solutions are provided in US, Europe, China and installed in Electric buses, Electric/Hybrid Cars in e.g. BMW, Mercedes, VDL Bus, JBM Auto Ltd., Vazirani Automotive, Maxwell Energy System (Ion Energy Labs), Force Motors, Spark Minda, Trinity Touch, Switch Mobility(Ashok Leyland), Propel, Pravaig, Sun mobility, Grinntech motors and many more
Referred to charging stations Bender eMobility solutions are used by e.g. KEBA, GARO, EBEE, EVA, EASYCHARGE ME, CP CONTECH, PHOENIX CONTACT, EFACEC, INNOGY, SM!GHT, CIRCONTROL, GnERGY, VATENFALL, E.ON and Ebee. India- ARAI, Ador Digatron, Belectriq Mobility (P2 Power), BEL, Supernova Engineers, Powerlogix Electro Systems, Joma India EV, Trinity Touch, goEgo, Axonify, Sun mobility, Amara raja, HBL, SFO technologies, Meras plugins, Ultrafast chargers
Bender Charge controllers support various backends like Allego, Fortum, Smatlab, NTT DATA, DRIIVZ, CHARGY, VIRTA, ChargeCloud, Be ENERGIZED and Bouygues Telecom. India- Mypowerexperts (TriSquare Switchgear), Charge dock, Jat holdings(Sri Lanka),
Further the Roaming Providers like HUBJECT and PlugSurfing are partners of the Bender technology
About the Authors
• Author Srinivas Rao G is an Instrumentation technology graduate, with over 25 years of experience as a professional in the fields of manufacturing, software, technology, and industry 4.0. Srinivas’s career trajectory, which began modestly with a German MNC but is still continuing to thrive today, has evolved from core manufacturing to technology and engineering to software. Worked with Raymond’s, Lafarge, and served for a long duration >16 years in ABB in a number of senior leadership roles , which include regional sales and marketing head (in India, Middle East, and Africa), regional operations head (South east Asia, South Asia, middle east & Africa) & later lead two businesses before he decided to take on new challenges and flourish and joined Bender India in 2022 as Jt. Managing Director with a goal to scale up the business and partner in India’s growth journey to make it a $5 trillion economy. He was just inducted into the Bender India board of directors to enable smooth operation and ramping up the company for greater success.
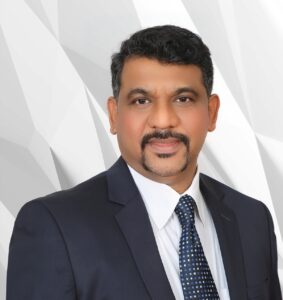
• Mr. P. K. Bhattacharyya is a post graduate electrical engineer with more than 33 years’ experience in electrical & electronic system application design. He began his professional career with Nuclear Power Corporation under Department of Atomic Energy and has 18 years’ experience in the application & design, testing, procurement, installation & commissioning of various electrical and electronic systems in the Indian Nuclear Power Plants. In 2008 he established Bender Germany’s subsidiary in India and since than expanded the Bender solution business sales in various core industries of Power Generation & Distribution, Oil & Gas, Steel, Cement, Chemical & Fertilizer, Mining, Navy & Shipping, Railways, Défense, Renewable Energy, eMobility and Hospitals and is the Director of Bender India Private Limited, Navi Mumbai. He has contributed many technical papers in international and national technical journals and technical application articles in various technical magazines.
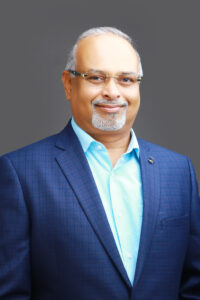
Experience the thrill of #Emobility, without the risk of electrical accidents. We understand that electric vehicles are crucial for a greener future and so have designed our products to help you get there! Discover the Bender range today and experience increased safety while enjoying the journey.