INITIATIVES TO SUPPORT CNC INDUSTRY TO WORK PROGRESSIVELY
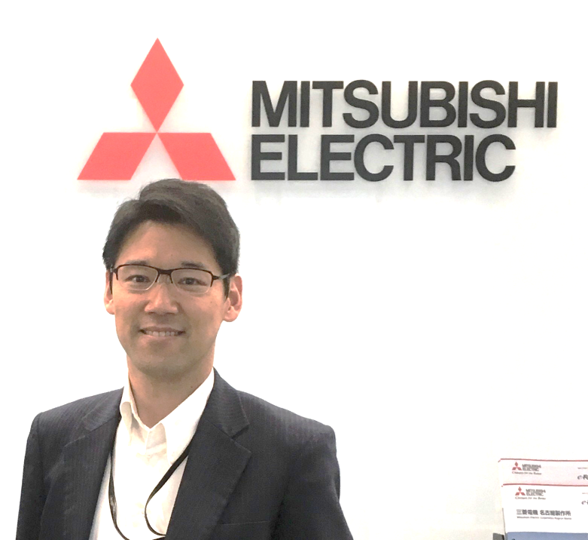
New Initiatives by Mitsubishi Electric that Support the Industry
The era of IoT has impacted revolution to a larger extends as a result of which, the world of automation has advanced like never before. The days of numerical controls being solely about servomechanisms are long gone. We are now living in the era of CNC (Computerized Numerical Control) systems. These control systems have aided in a variety of ways, starting from simple turning to complex machining. The controllers that operate these CNC systems are even more fascinating. Mitsubishi Electric India is always looking to partner with brands that are focused on global and future-oriented development. In order to keep up, the company developed a whole new set of controllers to bring advancement in the CNC system operations.
New Initiatives by Mitsubishi Electric that Support the Industry
The Extended Warranty Program
Mitsubishi Electric India has always prioritized product and service improvement, with a focus on delivering high-performance and cost-effective solutions. In a similar vein, the company has introduced a new Extended Warranty Contract (EWC) for specific Computerized Numerical Controllers in order to help the customers with better services
This ensures prompt responses, reliable technologies, and a user-friendly support system for clients all over India, resulting in better after-sales services.
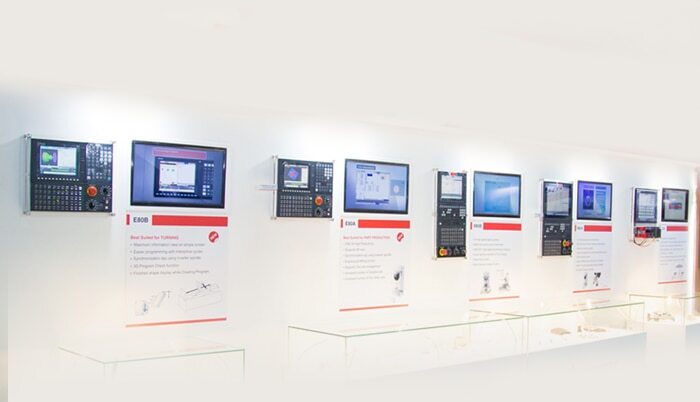
Benefits of the Extended Warranty Scheme
- Priority Response: With the EWC, you can rest assured that as soon as you call company’s service team to report a breakdown, service engineers will swing into action to find a solution for the problem caused.
- Low Operating Costs:The company guarantees that there will be minimal downtime and that the machine’s lifespan will be extended.
- Low EWC Price: The EWC is available in the market at an attractive price when compared to other leaders in the market.
- Lower Breakdown Time:The companyhas a set of highly trained and well-equipped engineers, and also keep track of all installed products and their service histories in their service management software to ensure that machines are repaired as quickly as possible.
- Free Inspection Visit: At the time of purchase of the EWC, Mitsubishi Electric India’s CNC will conduct a free machine evaluation. This benefits the customer because they can learn about the machine’s health and plan production / maintenance accordingly.
- No hidden costs: The contract covers engineers’ travel and lodging, as well as freight charges for shipments and part returns. There are no additional fees.
- CNC Service Support (Optional): Through a dedicated toll-free line, the company provide round-the-clock telephone support.
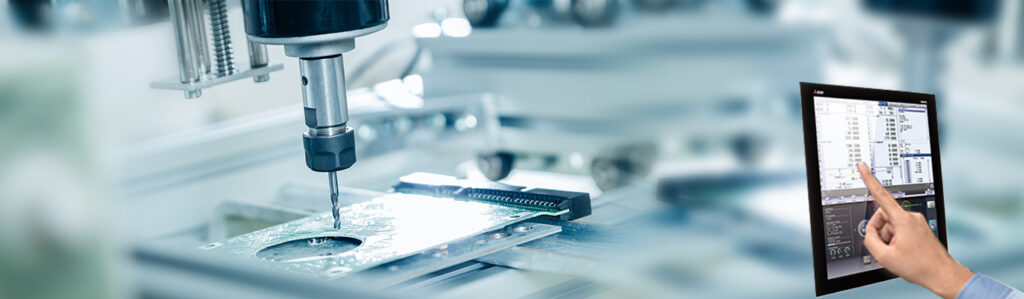
The following CNCs from Mitsubishi Electric India is covered by the extended warranty contract:
- ECONOMICAL: E70/E80 series with turning/grinding/gantry machines for cost-effective controllers.
- STANDARD: M60/M70/E70/M80/E80 series for standard controllers.
- CUSTOM: For Japanese and Taiwanese machine tool builders, Windows/customized controllers, including the C70/C80 series.
Importance of Preventive Maintenance Support (PM)
It’s critical to have a proper preventive maintenance plan in place to keep shop machines running smoothly. Routine inspections help the customers improve output efficiencies, increase uptime, and improved profit margins. With CNC machines and larger systems, this may be more difficult because individual components may break down or malfunction, which makes it necessary to keep a small stock of replacement parts on hand at the location.
When a machine is running continuously, the CNC’s parts may deteriorate due to the entry of dust, moisture, coolant, mist, and other contaminants. As a result, the parts may fail earlier than expected, or the machine may break down. In addition, any changes in the incoming voltage, cabinet temperature, or machine vibration can shorten the life of CNC parts. Customers can easily overcome such issues and ensure increased machine availability for their production procedures by using Mitsubishi Electric India’s regular preventive maintenance services. The following items are included in this preventative maintenance:
- Complete inspection of all CNC parts in the machine, including the power supply, temperature, and vibrations.
- Cleaning and replacement of any consumable parts, such as batteries and fans.
- The CNC’s entire data, including its hard disc, is backed up.
- Overhauling of the drives and motors at the Repair Centre (optional at actual cost).
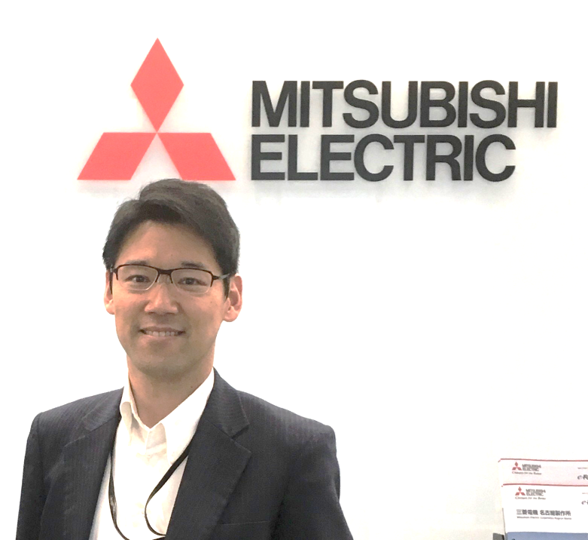
Mitsubishi Electric India Pvt. Ltd.
CNC SS24 Round the Clock Support
Mitsubishi Electric has a dedicated toll-free line that is available 24 hours a day and7 days a week. At the toll-free number and via email, the company’s CNC front engineers are available 24×7 to provide technical support. To ensure hassle-free operations for the registered customers, a dedicated toll-free number with password protection is provided.
Essential Features of this Round the Clock Support – CNC SS24
- Troubleshooting & Counselling
- Priority Service & Support
- Next Day Dispatch of Parts and Engineers
Mitsubishi Electric India has been taking steps to diversify service support in order to provide proactive support to manufacturers and the industry as a whole. The company established a CNC manufacturing facility in the country in 2013 in order to maintain responsive and faster product deliveries while ensuring robust production in the country. Then, in 2016, a CNC Technical Centre in Peenya, Bengaluru, was established to strengthen the services, sales, and manufacturing verticals. Mitsubishi Electric India supports India’s machine tool market by encouraging innovation and enhanced skill development activities in support of the government’s ‘Make in India’ initiative.
The company’s CNCs use precisely programmed commands to improve manufacturing accuracy and help enhance productivity in manufacturing. The rapid support and services offered by the company have been able to ramp up the manufacturing capacity and lesser delivery times which helped to shape the future of the Indian Manufacturing industry and step ahead towards advancement.
Working in order to make India Self-Sufficient
Mitsubishi Electric India Computerized Numerical Controllers (CNCs) aspires to be a trusted partner for businesses seeking global and long-term growth. It is also assisting India’s manufacturing industry with solutions that target specific growth segments for the country. This step is being taken to support the government’s ‘Make in India’ initiative among manufacturers across the country, as well as to ensure that AtmaNirbhar Bharat comes into practice with high-quality and reliable solutions.
Visit – https://mitsubishielectric.in/