Lightweight part production on the next level
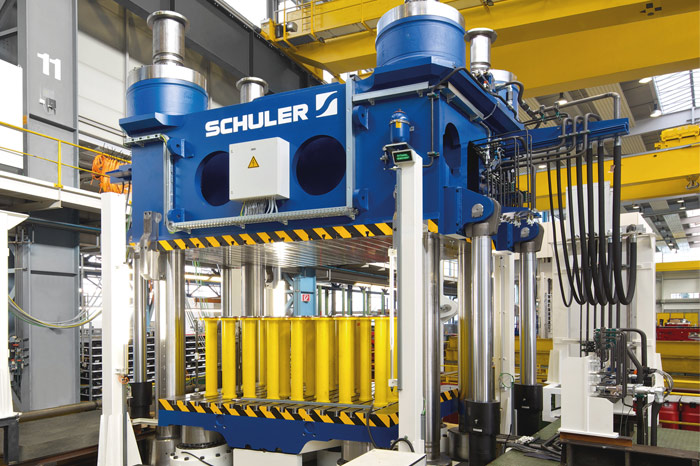
Lightweight part production on the next level
Schuler delivers 4,000 US ton hydraulic press to the Institute for Advanced Composites Manufacturing Innovation in Detroit, Michigan
Göppingen/Detroit, 09.05.2017 – 25 percent lower costs for carbon-fiber reinforced plastics (CRFP), 50 percent reduction in CFRP embodied energy, and 80 percent CRFP recyclability into useful products: These are the technical goals for the Institute for Advanced Composites Manufacturing Innovation (IACMI) in Knoxville, Tennessee, which is a part of the Manufacturing USA network. With a 4,000 US ton hydraulic compression press by Schuler, IACMI is expanding a research and development vehicle scale up facility in Detroit, Michigan. The facility is operated by Michigan State University on behalf of IACMI. IACMI Charter Member The Michigan Economic Development Corporation is also providing financial support for the equipment purchase and infrastructure improvements.
The technology focus areas of the non-profit institute are vehicle parts, wind turbine blades and compress gas storage. “All over the world, we need to enhance energy productivity and, at the same time, reduce life cycle energy consumption”, explains Ray Boeman, the associate director of vehicle technology and program manager responsible for the Detroit facility at IACMI – The Composites Institue. “The efficient and economic production of fiber reinforced plastics is a key opportunity here, and industry has identified a long term challenge – open-access to composite manufacturing equipment where technology can be developed and demonstrated on full-scale prototypes. With Schuler, we are bringing a key composite manufacturing capability online at the only facility of its kind in the US.”
“Our technology not only offers a dynamic force control for reduced energy consumption, but also a greatly reduced mold try-out and wear compensation which ensures a fast development process for the IACMI,” says Paul Nicholson, CEO of Schuler North America. “Furthermore, the congruent bending lines of slide and table compensate natural variations in process variables and materials.”
Congruent bending lines are a necessary precondition to manufacture thin parts within limited tolerances significantly below 0.01 inches – e.g. for lightweight construction. Schuler can also provide vast experience with processing other lightweight materials like aluminum and hot stamped high strength steels.
The upstroke short-stroke press has with a clamping surface of 142 x 94 inches will be ready for production at the end of May, the final acceptance is planned in June. The addition of the Schuler hydraulic press diversifies and increases IACMI’s unique equipment available to more than 150 members of the organization, with Schuler having become one of them only recently.
Internet
www.iacmi.org
Caption
Schuler delivers a 4,000 US ton hydraulic press to the Institute for Advanced Composites Manufacturing Innovation in Detroit.
The upstroke short-stroke press will be ready for production at the end of May, the final acceptance is planned in June.
About the Schuler Group – www.schulergroup.com
Schuler is the world market leader in metal forming technology. The company supplies presses, automation solutions, dies, process know-how, and services for the entire metalworking industry and lightweight automotive design. Customers include automobile manufacturers and suppliers as well as companies from the forging, household appliances, packaging, energy, and electronics industries. Schuler is the market leader in minting presses and supplies systems solutions for the aerospace, railway and large pipe industries. In 2016, Schuler achieved a turnover of 1,174 million Euros. Following the acquisition of die manufacturing company AWEBA and with a majority holding in Chinese press manufacturing company Yadon, Schuler employs around 6,600 members of staff in 40 countries. The Austrian ANDRITZ Group holds a majority share in Schuler.
About IACMI – The Composites Institute – www.iacmi.org
The Institute for Advanced Composites Manufacturing Innovation (IACMI), managed by the Collaborative Composite Solutions Corporation (CCS), is a partnership of industry, universities, national laboratories, and federal, state and local governments working together to benefit the nation’s energy and economic security by sharing existing resources and co-investing to accelerate development and commercial deployment of advanced composites. CCS is a not-for-profit organization established by The University of Tennessee Research Foundation. The national Manufacturing USA institute is supported by a $70 million commitment from the U.S. Department of Energy’s Advanced Manufacturing Office, and over $180 million committed from IACMI’s partners.