Made of Sterner Stuff
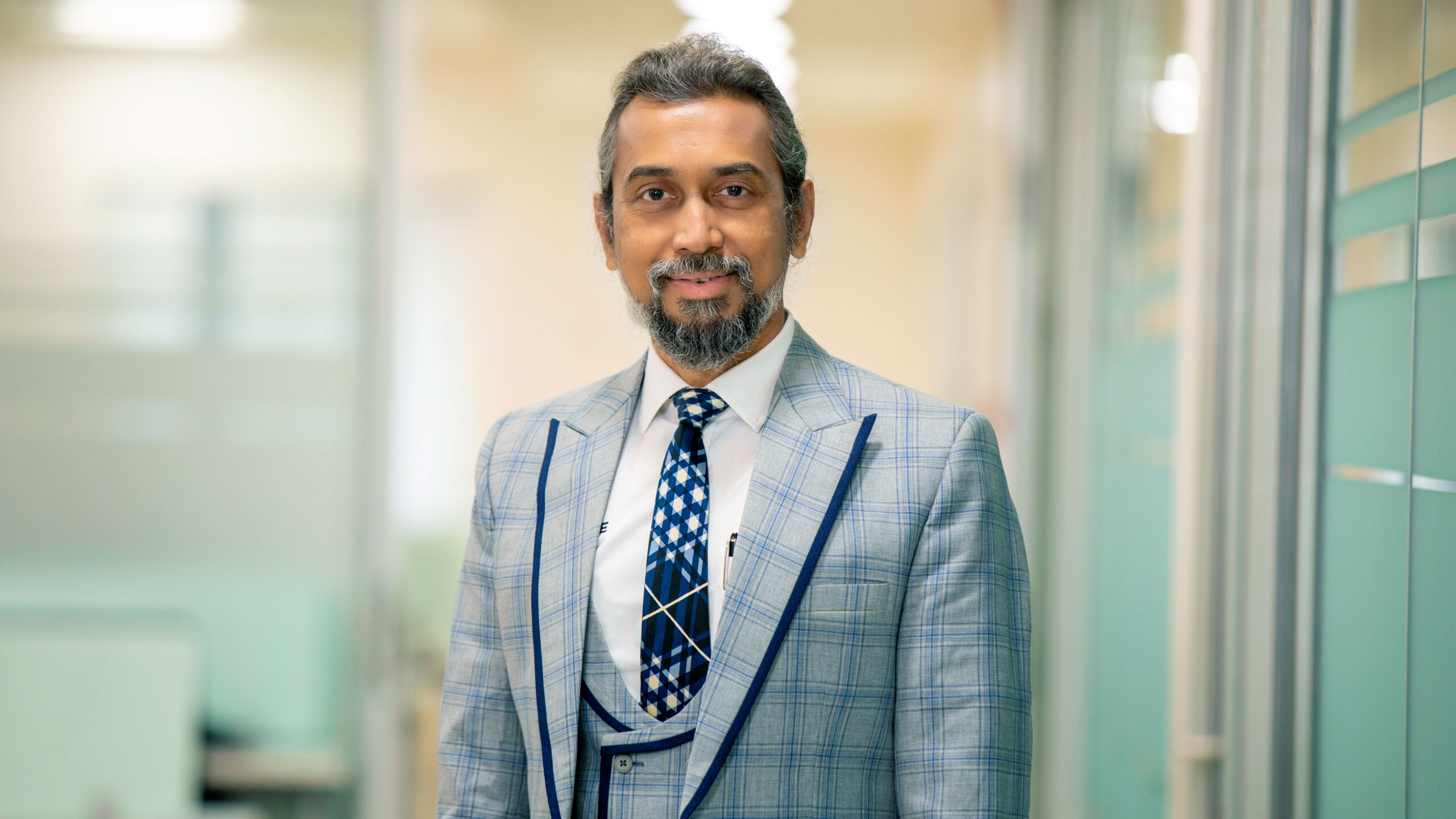
Prashant Sardeshmukh, Managing Director, MMC Hardmetal India Pvt. Ltd shares how the company kept its morale up during the pandemic, tuned up with latest technological advancements, strengthened the grey areas and ironed out various systems.
MMC Hardmetal India Pvt.Ltd (MMCI) is a fully owned subsidiary of Mitsubishi Materials Corporation, Japan. The company offers a wide range of Metal Working Products, Services & Solutions, for various applications in Automotive, Energy, Die &
Mold, Oil & Gas, Medical and Aerospace industry, etc. MMCI also offers complete technical support and know-how for projects and productivity improvement solutions.
The company has its headquarters at Bengaluru and regional offices at Pune, Gurgaon, Chennai, and Ahmedabad. The company is in operation since 2006 primarily covering the Indian market. Prior to launching full-scale Indian operations, activities for the Indian market were handled from Singapore, since 1998. Over the years, it has expanded operations beyond shores to cover overseas markets viz. Gulf Region, Iran, Sri Lanka & Bangladesh, etc.
Being part of a globally acclaimed Mitsubishi business tradition, MMCI is fortunate to inherit excellent quality culture. The company has established a very effective and efficient Sales Network through its regional offices and distributors across the country. MMCI is a team of talented professionals, with excellent engineering backgrounds and experience. This young, energetic, and dynamic team is committed to proving its excellence in the competitive environment.
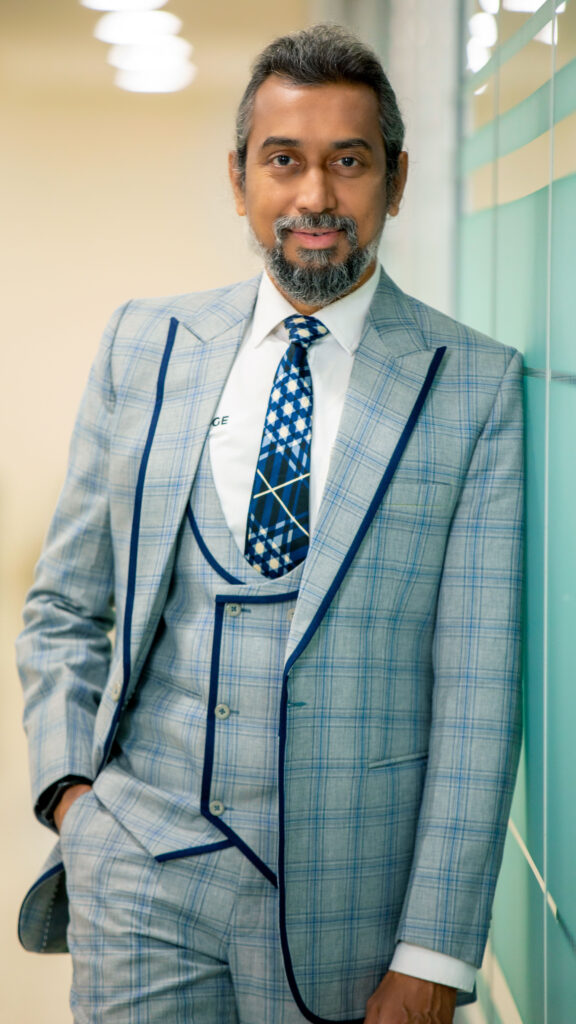
In recent times, MMCI established a high-end manufacturing plant at Aurangabad to manufacture special/customized tools. The products manufactured at this plant are at par with Japanese quality standards. Approximately, 1/3rd of these products are exported to Japan and other advanced countries.
Shortly, MMCI has launched its highly advanced Technical Centre in Pune to train its employees, Business Partners, and Customers. This will help the company to have more integrated relationships with its customers and it will also expand the outreach. The Technical Centre provides a strategic advantage to initiate Research & Development activities and give effective engineering solutions to the customers. MMCI has also set up a Regrinding Centre at Pune for the regrinding of Solid Carbide Tools. Prashant Sardeshmukh, Managing Director, MMC Hardmetal India Pvt Ltd spoke about the company’s performance strategy during the pandemic, the latest demand trends, and new solutions in interaction with Aradhita Srivastava. Excerpts.
The last two years have been particularly tough for the global metalworking industry with lockdown restrictions and wild demand fluctuations. How has your company coped and performed in India?
It was an unprecedented situation for everybody. The threat of the pandemic and impact of lockdown was so intense, that everyone was at sea.
After the initial period of perplexity, we were able to assess the challenge. It was important to remain connected and keep the morale of the team. The momentum was lost due to frequent shutdowns and interruptions in the supply chain operations.
We focused our efforts on remaining in touch across all business centers and with our business partners too. With digital support, we established dialogue amongst ourselves, had regular meetings and reviews. Our teams at various sales centers used this adversity to tune up with the latest technological advancements, strengthened the grey areas, and ironed out various systems.
We initiated regular interactions with our distributors and customers as well. Besides, we conducted a host of online technical training sessions for our customers. It helped us to understand their problems and wherever possible we offered them remote support. All these measures kept us agile and nimble. Therefore, when the situation improved, we could get on track quickly.
What are the bestselling metalworking products and solutions that you provide to the automotive and aerospace industries in India?
The AHX Series Milling Cutter with 14 Cutting Edge inserts is one of the most appreciated products by our Automotive Customers. This product is available in various designs and can offer multiple solutions to various customer needs. Together with this our wide range of Drilling Solutions is very popular with Automotive Customers.
ʹSmart Miracle Endmillʹ is the revolutionary addition to our product range which is specially designed for ʺdifficult-to-cutʺ materials such as CoCr and Titanium alloys. It guarantees improved chip discharge, longer tool life, and unbelievable precision in machined surfaces. This is especially effective for aerospace component machining. I can name another few cutting-edge products such as our new chip-breaker system series, our new ASPX series cutter for milling, expansion of the iMX Series.
Which sectors are the best performers for your business in India and what products and solutions do you have for them?
Going by the conventional wisdom, the Automotive Sector and component manufacturing sector are known to be the best performers for us. In recent times, other sectors like aerospace, energy, die & mold, general engineering, and medical are also providing us good opportunities.
We also offer complete technical support for MTB projects and productivity improvement solutions to different sectors named above. Our range of services includes vibration and noise analysis, chip form analysis, and structural analysis for improved working.
How do your solutions provide an extended tool life thus reducing the cost-per-hole in a manufacturer’s process?
MMC has improved its drilling technology by implementing of following new techniques:
The new TRI-CoolingTechnologysubstantiallyincreases the coolant discharge compared to conventional drills. This significantly improves chip evacuation and eliminates heat in the cutting zone, resulting in longer tool life. This prevents chip jamming and assures longer tool life as well as high-efficiency drilling from shallow to deep hole drilling applications.
Fracture resistance is improved by connecting the straight main cutting edge and the web thinning with a smooth arc shape. In addition, by providing land on the rake face, crater wear resistance and chip breakability is improved. It prevents chip jamming by breaking the chip generated into small pieces. The XR web-thinning curls chips and controls the chip flow in the proper direction, thereby reducing cutting force and increasing chip breaking performance.
DP1120 is a PVD coated grade containing fine cemented carbide grains. The ultra-smoothened surface is formed by our layer formation technology, suppressing chip jamming and preventing drill breakage. In addition, the high crater wear and fracture resistance maintain good cutting edge condition even during long machining cycles.
The short drill is designed for high rigidity and good chip evacuation by minimizing the neck length. A chip discharge area is provided over the taper part, increasing the tool rigidity by @20% more than the conventional model as well as improving the hole position accuracy.
How do carbide-based tools compete with solid-ceramic end mills when it came to the milling of superalloys?
Superalloy such as Inconel is one of the difficult-to-cut materials which is machined at cutting speed of 20-100m/min with carbide end mills which results in low machining efficiency and short tool life, especially in a roughing with large stock removal. Ceramic has a property that its material strength doesn’t sharply decrease under high temperatures like a cemented carbide.MMC’s newly developed ceramic end mill achieves high-efficiency milling with longer tool life by increasing cutting speed by more than 300m/min and lowering the strength of the work-piece. Ceramic end mill series are solid end mills adopting ceramic substrate. These are designed to perform high-speed and high-efficiency milling of Ni-base heat resistant alloy by adopting the special cutting edge geometry as well as utilizing the property of ceramic, such as heat resistance, high-temperature strength, and fracture resistance.
Do you expect an increase in demand for Polycrystalline Diamond (PCD) and carbide drills with automakers and particularly the aerospace industry shifting more materials to composites?
CFRP is one of the composite materials and the application of high-strength CFRP is generally considered by the aerospace industry, in the manufacturing important structural components of large commercial aircraft. Machining such materials is extremely challenging and critical because of their mechanical and physical properties.
PCDtools are largely used in the industry because of their astonishing physical properties. But their ultra-high hardness limits the machining efficiency of conventional abrasive grinding processes. Nonetheless, I believe, with extensive research, this drawback can be removed.
As regards Carbide tools, the pandemic outbreak has hindered the growth of the global carbide tools market for the last couple of years. However, with positive demand prospects from the automotive, transportation, and heavy engineering sector, this market is expected to pick up and it is expected to witness steady growth in the years to come.
How do you plan to innovate your solutions to productively machine materials like new alloys and hybrid materials coming into the market?
“Smart Miracle” Endmills with (Al, Cr)N base coating have greatly improved wear resistance. Target materials are difficult-to-cut materials, such as stainless steel, Titanium alloys, Inconel718, etc. The “Impact Miracle” series can be effectively used for high-speed machining of a variety of hardened steels.
An aircraft body and jet engine use advanced materials which are extremely difficult to cut. When cutting such materials, the removal amount during machining becomes very large, particularly in large components. Since most aircraft manufacturers focus on not only the quality of the product but also productivity, they request high-efficiency machining, and it is indispensable to use high-efficiency tools dedicated to machining difficult-to-cut materials. Our new ASPX Series is designed to achieve high-efficiency milling of titanium alloys and it can contribute to improving customers’ productivity by achieving machining with large depth of cuts.
http://www.mitsubishicarbide.com/