Micro Forming and Machine Tools: Challenges and Opportunities
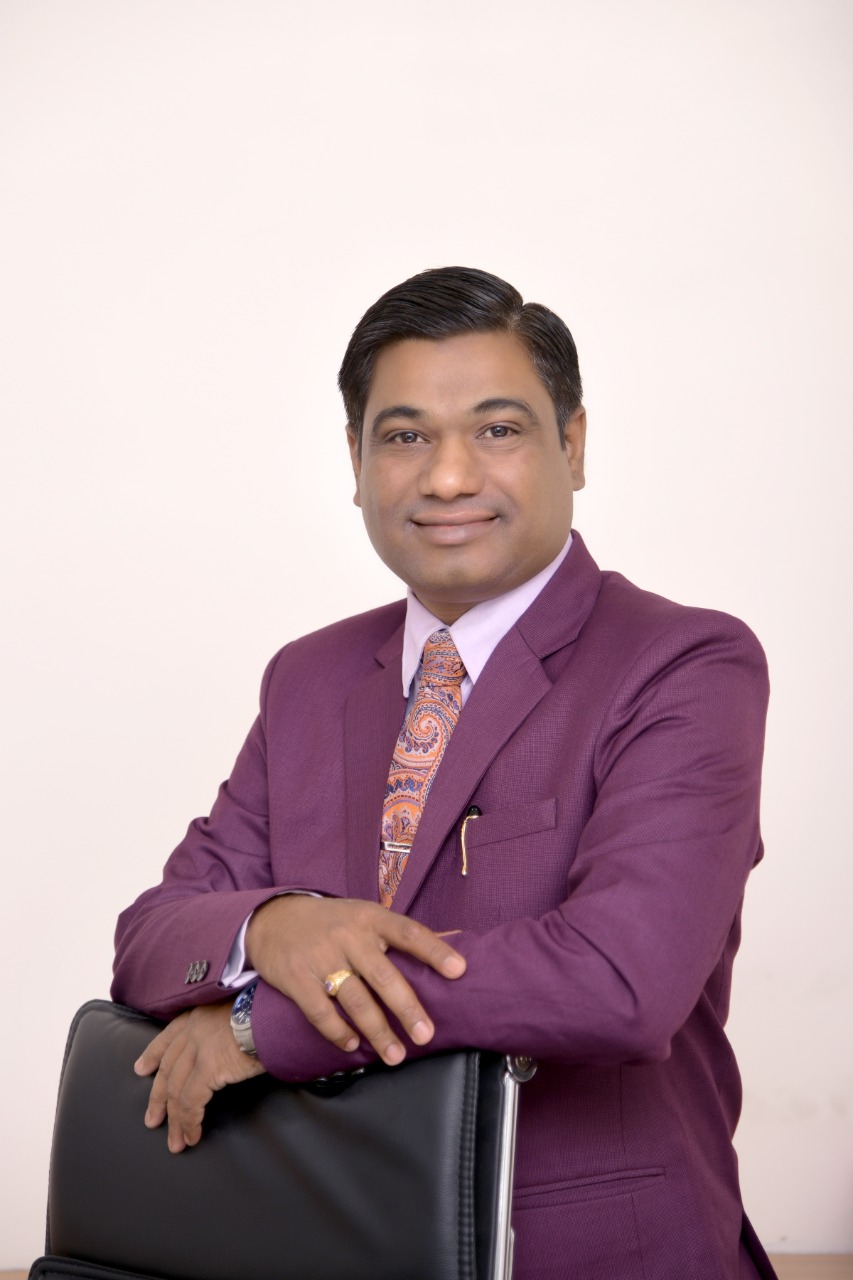
Introduction to Micro Forming
The term micro metal forming, generally coined as micro forming refers to the production of parts or structures with at least two dimensions in the sub-millimeter range. Micro forming is a well-suited technology to manufacture very small metallic parts, in particular for mass production, as they are required in many industrial as well as domestic products. Micro-metal forming can be broadly divided into bulk and sheet-metal forming. The trend of miniaturization is increasingly determining the development of various products ranging from Automotive, Aeronautics, Healthcare to Electronics and Communication Applications. It is facilitating product usage, enabling unique product functions to be implemented in micro-scaled geometries and features, and further reducing product weight and volume. One of the major challenges facing the industry is the dynamic market which requires continuous improvements in design and fabrication techniques.
This means providing products with complex features while sustaining high functionality. Cellular phones become smaller with every new generation and with adaptive designs offering enhanced functions to customers. Besides electronic components, these devices also contain mechanical parts such as connector pins, miniature screws, contact springs, micro gears, chip lead frames IC-sockets, cups for the electron gun in color TV sets or shafts of small motors etc. Miniaturization has also gained importance in Micro Electro-Mechanical System (MEMS). Miniaturization has interdisciplinary approach, which brings together the know-how of electronics and mechanics, or in details, of physics, chemistry, material science, manufacturing technology and many others. Due to high demand of these components, forming processes play an important role in this sector, since they are unbeatable when large numbers of parts have to be produced. The processes typically employed are blanking, bending and stamping/forming. Wire bending is applied for production of filaments and springs as used in medical applications and the electronic industry.
Challenges in Micro Forming
The challenges appearing in Microforming which complicate the process are obviously strongly coupled with miniaturization itself. Two major issues in micro forming are most important. One is Size effect and other is Grain Size effect. As formability, flow stresses, deformation behaviour, damages, failure limit curve are functions of these. Plastic deformation is carried by the movement of so-called dislocations through the material on the so-called slip planes. Grain size effect on micro scale deformation is major issue that needs to be addressed in greater depth.
Ductility in turn formability is greatly influenced by grain size. When the sheet metal thickness is decreased to microscale, the number of grains involved in the deformation zone becomes critical to the quality of the parts. It is revealed that inhomogeneous deformation occurs with the increase of grain size. This is due to the fact that when there are only a few grains existing in the deformation zone, the deforming material cannot be considered a continuum due to the strong anisotropic properties of grains Basic research is needed to reveal the nature and mechanism of size effects with scaled-down experiments according to similarity theory. Because the variation of the mechanical properties is interesting when down sized. Micro forming system can be split into four groups Material, Process, Tools and areas-specific effects of miniaturization. The process is of course strongly coupled with the material used for manufacturing. However, there are additional challenges concerning the forming forces, tribology and spring back, which has influence on the accuracy of the parts to be produced. Handling small parts is itself challenging
Opportunities in the Development of Machine Tools
The research and realization of micro forming processes in laboratories are very different when tested in mass production. Quality of product with speed and productivity of the system matters a lot. There is a need to design a proper process chain for Micro Forming. Although some of the parts are currently being produced by micro forming technology, still now the major numbers of these parts are produced using a conventional manufacturing process. The design of machine tools affects the performance of the micro-forming system and the quality of the micro-formed parts in terms of deformation load, stability of the forming system (scatter of process variables), defect formation, and dimensional accuracy, mechanical properties and surface finish of the formed microparts.
Designing and manufacturing complex inner geometries of the tools such as extrusion die, the alignment of punch, die, and knockout pin, and the overall precision of the machine is most important. Presently all the machine tools applied in manufacturing are those of macro forming, utilized with customized setups for micro forming. The high-capacity machines in terms of tonnage capacity are being utilized unnecessarily, at the cost of loss in productivity due to the non-availability of specially designed machines. Lightweight machines in the range of 20KN need to be developed, with high precision and high-speed production. The Actuator can be operated by a Linear motor/Piezoelectric/Servo motor.
Clearance or backlash between the die and punch become a primary problem when the total stroke to form the micro-part is in the range of several hundred micrometers. Machine automation also needs to be developed to meet the industrial capability requirement. Since the part size is extremely scaled-down and part weight is much lighter, handling and holding of micro-parts will be extremely difficult because of adhesive forces. Hence, special handling and part-holding equipment need to be developed to address these difficulties. There is a greater opportunity for machine tool manufacturers to design and develop modular micro-forming machines which can be utilized for various micro-forming operations enhancing productivity.
Authored By – Prof. Dr. Ganesh M. Kakandikar –School of Mechanical Engineering,Dr. Vishwanath Karad MIT World Peace University, Pune.