New cooperation established for plant technology to manufacture fuel cells on a large scale
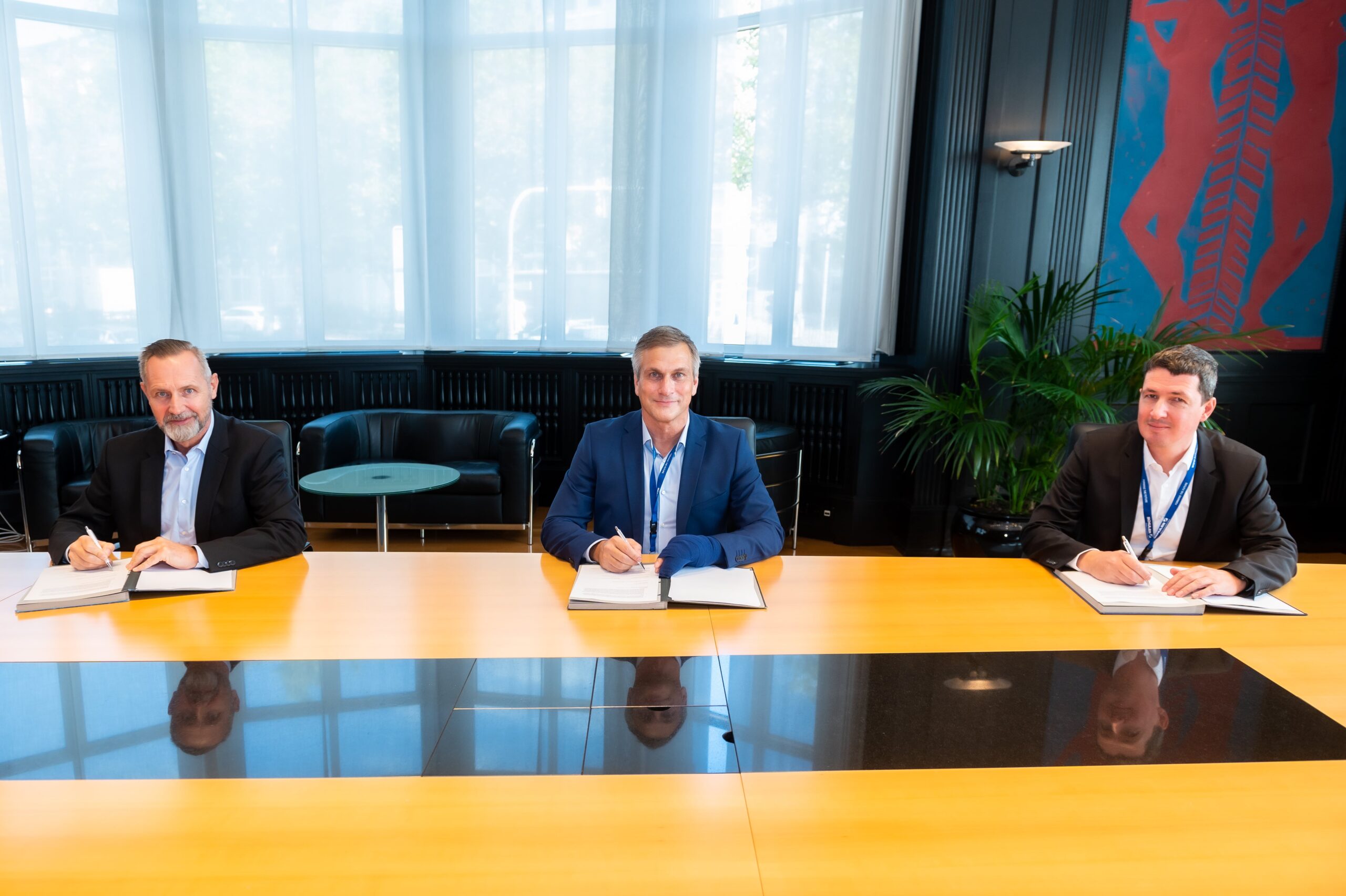
Thyssenkrupp Automation Engineering, Andritz Soutec and Schuler Pressen to supply integrated production systems for fuel cells
Bremen/Neftenbach/Göppingen, September 29, 2021–ThyssenKrupp Automation Engineering (as part of ThyssenKrupp System Engineering GmbH), Andritz Soutec and Schuler Pressen are joining forces and have signed a cooperation agreement to offer end-to-end production lines for the high-volume manufacture of metallic bipolar plates today. Customers will benefit from receiving everything from a single source. In addition, solutions for the production of the membrane electrode assembly (MEA) as well as for the stack and system assembly of fuel cells including testing technology can be supplied. This covers the entire value chain for manufacturing, assembling, and testing a fuel cell.
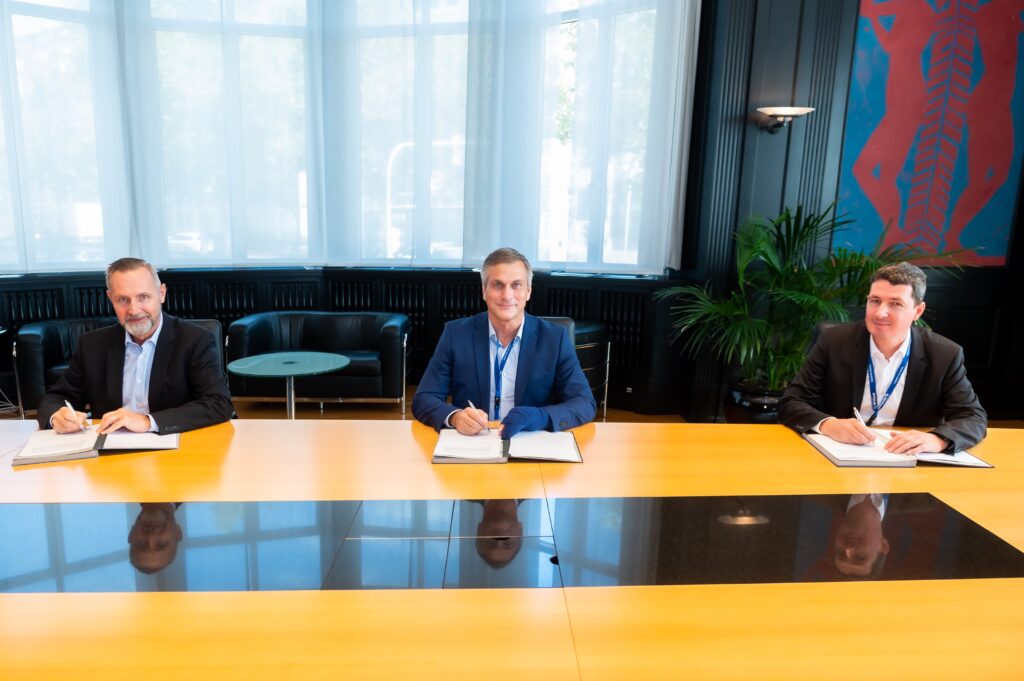
The bipolar plate production lines are scalable and designed for a capacity of up to 50,000 stacks per year, with around 300 to 400 bipolar plates being installed per stack. This requires an output rate of around one bipolar plate per second.
The first process steps on the production line are forming technology for coining and trimming bipolar plate halves made of stainless steel sheets with a thickness from 70 to 100 µm. Schuler offers mechanical and servomechanical knuckle-joint presses with press forces of up to 2,000 t for this purpose. The innovative “IntraTrans” transfer system enables simultaneous production of both bipolar plate halves – anode and cathode – in one press stroke. Material is fed from both sides of the press and transported through the individual die stations to the press center. In addition, the bipolar plate halves can be brought together in the press and pre-joined by means of a spot welding process so that the position of both halves relative to each other is fixed.
In the subsequent process step, the bipolar plates are precisely welded gas-tight by remote laser welding. Andritz Soutec offers continuously operating laser welding systems for this purpose, in which the bipolar plates are welded by means of several laser beam sources operating in parallel. A subsequent leak test of the bipolar plates guarantees constant quality.
A seal is then applied, dried, and visually checked for correct quality on both sides of the bipolar plates in equipment provided by ThyssenKrupp Automation Engineering using dispenser stations. In addition to an innovative system for transporting the bipolar plates between the plant sections, ThyssenKrupp offers equipment for producing the MEA and for stacking MEA and bipolar plates to form the final fuel cell stack, including testing technology. In addition, a comprehensive track & trace system enables traceability of the individual bipolar plates starting from the coil material as well as all other production data of a fuel cell assembly.
About the Schuler Group – www.schulergroup.com
Schuler offers customized cutting-edge technology in all areas of forming—from the networked press to press shop planning. In addition to presses, our products include automation and software solutions, dies, process know-how, and service for the entire metalworking industry. Our customers include automobile manufacturers and automotive suppliers, as well as companies in the forging, household appliance, and electrical engineering industries. Presses from the Schuler Group mint coins for more than 180 countries. When it comes to the digital transformation of forming technology, we support our customers worldwide as a supplier of innovative system solutions. Founded in 1839 at our headquarters in Göppingen, Germany, Schuler AG has approx. 5,000 employees at production sites in Europe, China, and the Americas, as well as service companies in more than 40 countries. The company is part of the international technology group ANDRITZ.
About ANDRITZ Soutec – www.andritz.com/soutec
ANDRITZ Soutecis the leader in the area of high-quality laser welding systems for flat and round parts and a specialist for laser and roll seam welding systems for a wide array of applications. More than 130 fully automated systems produce more than 200 million parts per year globally for the automotive industry. Furthermore, ANDRITZ Soutec is the leading company for resistance welding systems, in particular for the heating, ventilation, and air conditioning industry. The global activities are based on more than 60 years of experience and future development with high efficiency for industries of the highest standards and quality. Soutec concentrates its activities mainly on the automotive industry for which the company produces equipment for the production of tailored blanks, tubular blanks, steel fuel tanks, and exhaust systems.
About ThyssenKrupp Automation Engineering –
www.thyssenkrupp-automation-engineering.com
ThyssenKrupp Automation Engineering as part of ThyssenKrupp System Engineering GmbH is an internationally operating business unit of the Multi Tracks segment of ThyssenKrupp AG. The company bundles all activities in the field of powertrain and battery assembly with a major focus on the transformation towards electromobility. More than 1,400 employees work in ten countries worldwide.