Optimized recycling in waste incineration plants
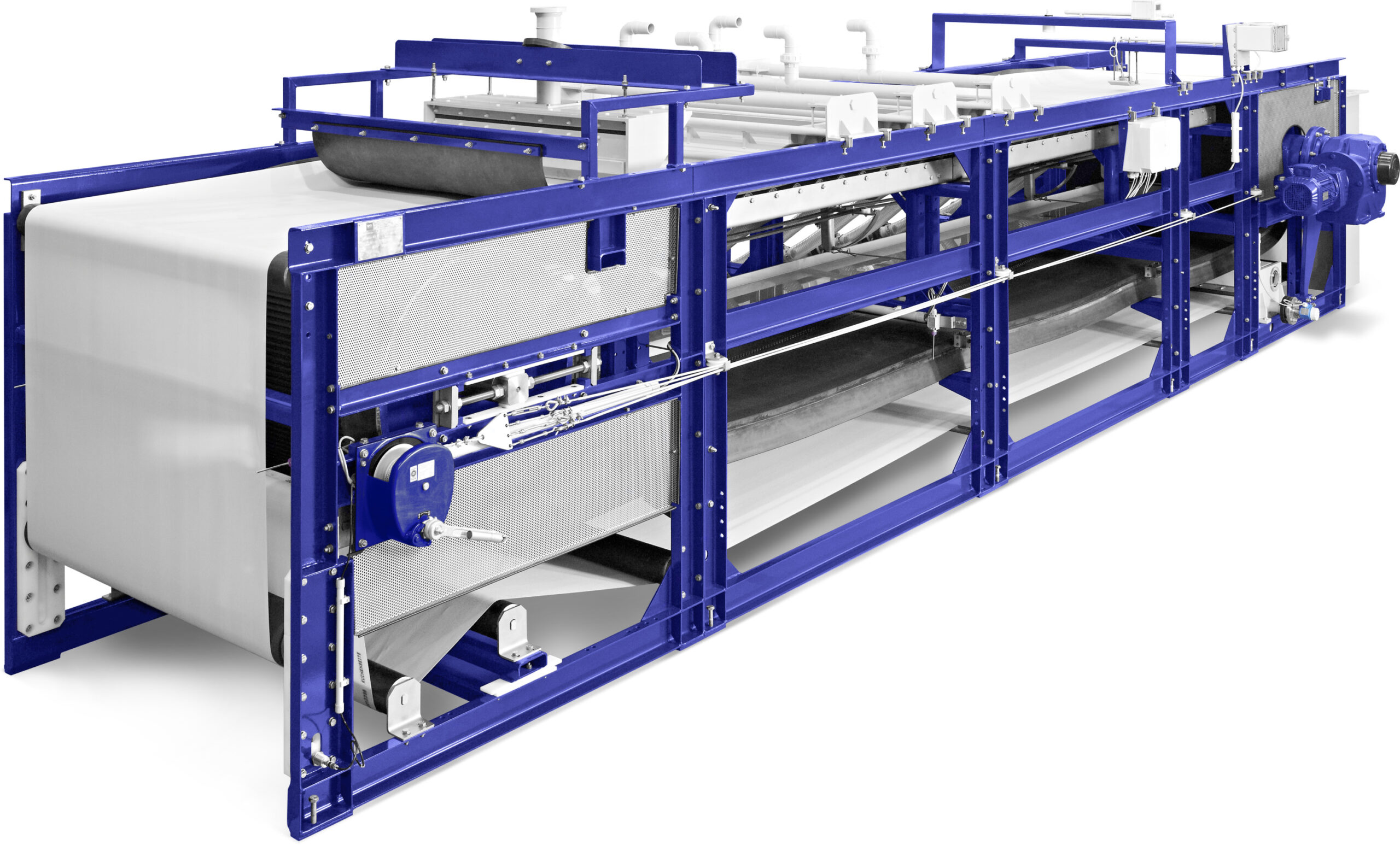
Vestforbraending relies on technology from BHS-Sonthofen for a new type of fly ash treatment process
Sonthofen, Germany, 10 February 2022. BHS-Sonthofenhas supplied two different technologies to assist an innovative recycling process in waste incineration: Since2021, a rubber belt filter especially suited to the requirements of the new process and a belt filter have ensured fly ash at the Danish power plant operator Vestforbraending is treated efficiently.
This brings two benefits: Recyclable materials can now be recovered from the ash and the ash previously declared as hazardous waste can be disposed of as normal waste. Extensive preliminary filtration tests on a laboratory scale were performed before the order was placed to obtain an optimum process result immediately upon commissioning.
The EU wants at least 50percent of household waste to be recycled and the rest to be used as a source of energy in waste incineration plants. However, the operators of these plants face a number of challenges along the way. Waste incineration produces ash contaminated with salts and heavy metals, which is considered hazardous waste and must be disposed of in special landfills. This involves long transport routes and high costs.
Vestforbraending developed a new type of fly ash treatment process under the name HALOSEP in cooperation with the Swedish recycling company Stena Recycling. The project, officially called LIFE HALOSEP, is supported by the EU through the LIFE financial instrument– a funding program for environmental protection measures.
Heavy metals and salts can now be recovered from the fly ash. This makes it possible to store the ash residue in normal landfills for non-hazardous waste, unlike the input material. The new process is therefore a win-win in two respects: It makes it possible to market recovered recyclables and reduces disposal costs.
The pilot plant in Copenhagen, equipped with technology from BHS-Sonthofen Process Technology, started operation in 2021. Samuel Moore, project manager at Vestforbraending, is convinced: “BHS-Sonthofen sets itself apart with its special expertise in the field of filtration. Having such a strong process engineering partner is essential for pilot plants in particular.”
Process efficiency thanks to the perfect technology
Treating fly ash produced during waste incineration is a multi-step process. First, it is mixed with the flue gas cleaning washing water, which leads to metals and salts being released from the ash. A BHS belt filter then filters the resulting suspension. After a further wash, the solid that remains is purified ash.
The process water used in the first step is treated further to recover both salts and metals. After the saltwater has been separated, a BHS rubber belt filter with continuous vacuum filtration filters the suspension; the metals are left behind as solids. The process water can now be returned to the process. “Salts and heavy metals are highly corrosive.
That is why a robust and corrosion-resistant design was crucial for this project,” says Simone Ahlert, Technical Sales Manager at BHS-Sonthofen Process Technology, summarizing the customer’s main requirements. “BHS-Sonthofen has extensive experience with problematic input materials. All of the machines can also be tested in advance with the respective material.”
Preliminary tests provide all the facts
Each process is unique. For that reason, all of the process parameters and design principles used to select the appropriate filter size must be determined on a case-by-case basis. BHS, therefore, carried out on-site tests on a laboratory scale directly at the customer’s site, using the exact material that will be used in the final process.
“A constant throughput is crucial in a continuous process– thanks to the laboratory tests, we were able to determine the best way to adapt the rubber belt filter used as well as the belt filter to the process in advance. This means it can be integrated into the overall plant much more efficiently, even with completely new processes such as HALOSEP– or related processes such as FLUWA,” says Ahlert, explaining the proven procedure.

15,000 tons of fly ash will be treated at the plant annually. Moore is confident that he will be able to further optimize the process with the help of strong partners such as BHS-Sonthofen. “Up until now, fly ash could only be deposited as hazardous waste in a mine or mountain, which involves long transportation routes. The aim of the HALOSEP process is to reduce the load on the ash so that it can be deposited locally. If we’re successful, we’ll look at the possibility of using the ash as a building material.”
About BHS-Sonthofen GmbH
BHS-Sonthofen is an owner-operated group of companies specializing in machinery and plant engineering with headquarters in Sonthofen, Germany. In keeping with our mission “Transforming Materials into Value,” we offer innovative process solutions, technologies, and consulting services in the business areas of Process Technology, Building Material Machinery, as well as Recycling & Environment. Our experts in the field of mechanical and thermal process technology with a focus on filtration, drying, mixing, crushing, and recycling form the basis for our success. Our company has a global presence, with 500 employees, three production facilities and nine subsidiaries.
The Process Technology division is one of the world’s leading providers for components and systems related to the solid-liquid separation, drying, mixing, and reaction process steps. We offer our customers more than just our comprehensive product range. In fact, working together with the customer to select the perfect solution for each case and implement it is at the heart of what we do. Increasing efficiency and process optimization are crucial elements in this process. Our customers operate in the chemical and pharmaceutical industries, power plant technology, the oil and gas sectors as well as the food and feed industries.