Revolutionizing Metal-Cutting Technology
Insights from Sarah Pizzolato, Marketing Manager, AZ SPA
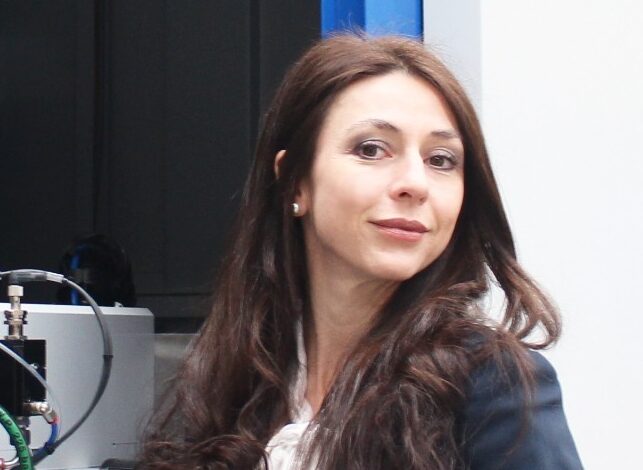
1) What recent advancements in metal-cutting technology have had the most transformative impact on efficiency and precision?
Automation has revolutionized manufacturing processes. New fully automated machine control systems have made production cycles faster and more efficient, eliminating the need for manual intervention. This flexibility allows for customization of production processes and quick adaptation to new requirements. Furthermore, integrated monitoring systems optimize maintenance, reduce downtime, and ensure greater plant availability.
2) How is the industry adapting to sustainable manufacturing practices, and what specific initiatives are helping to reduce environmental impact?
AZ recognizes the importance of the environment for the well-being of the community and is committed to complying with environmental regulations, promoting a company approach focused on the responsible use of resources and respect for the environment.
- Energy Efficiency: We reduce energy consumption by making infrastructures more efficient and using eco-efficient technologies. Recently, we installed a photovoltaic system that alone covers 60% of the company’s energy needs.
- Employee Mobility: We implement solutions to reduce the impact of travel. With the introduction of new technologies for remote assistance, we have reduced the use of company and public transport, along with the number of trips.
- Waste Management: A waste sorting system is currently in place. This system involves all company areas, where differentiated bins have been provided to allow employees to separate waste into specific categories such as paper, plastic, glass, and general waste. AZ has implemented several initiatives aimed at reducing waste and promoting the responsible use of materials. One of the main actions has been the introduction of reusable water bottles and cups as alternatives to single-use plastic bottles.
- Circular Economy and Resource Efficiency: Retrofitting of used machines allows our machines to have an infinite life cycle. We refurbish used machines, giving them new life.
- Smart Service: Thanks to the use of Augmented Reality (AR), we enable customers worldwide to connect with AZ technical support. Using special vision devices called AZ-SmartGlasses, AZ technical support can see through the operator’s eyes and provide precise instructions in real time on the correct operations to be performed. This technology reduces human errors, the risk of identifying incorrect spare parts, and the delivery times of spare parts, as well as service costs and times.
- Smart Machines – Cloud, IoT & Security Service Revenues: With this new cloud-based software, AZ can continuously monitor the operation and performance of its machinery, including predictive maintenance, via PC or smartphone, ensuring optimal performance of the grinding machines. AZ technicians, for example, can modify the operating parameters of the machines directly from the platform, integrating a web page from the PLC into the dashboard. This allows for weekly, monthly, quarterly, and annual production performance reports. Furthermore, through data analysis, we can carry out predictive maintenance of machine components and generate notifications to the customer when a maintenance event is approaching, enabling prompt interventions. This drastically reduces emergency situations and unplanned production downtime.
3) With digitalization reshaping manufacturing, what new skills are essential for today’s workforce, and how is the industry addressing the skills gap?
Flexibility is one of the essential qualities we seek in our employees. The ability to adapt to customer needs and find immediate solutions is crucial. Customers increasingly demand not only the machine but also a comprehensive range of related services.
4) What trends are driving the current demand for metal-cutting solutions, and how do you foresee the industry adapting to these trends?
The growing demand for unique, customized products drives us to continuously invest in research and development, creating innovative and personalized solutions. We develop new technologies and materials to meet the needs for precision and flexibility, always with respect for the environment. We collaborate with the best partners to offer integrated and cutting-edge solutions. Our commitment is to support customers at every stage of their project, providing consulting, training, and after-sales support. The future of the industry is characterized by continuous evolution: those who can innovate and personalize their solutions will be the true winners.
5) What do you view as the most significant challenges facing the metal-cutting industry today, and what steps is your organization taking to stay competitive?
The most significant challenges are delivering a complete customer solution that extends beyond the product sale, incorporating service, maintenance, and post-sale support. To meet this need, we have established dedicated departments within our company for customer support and spare parts. We have also developed a remote assistance network that significantly reduces intervention costs and times. Furthermore, we integrate monitoring systems into our machines, enabling us to track consumption and maintenance needs.
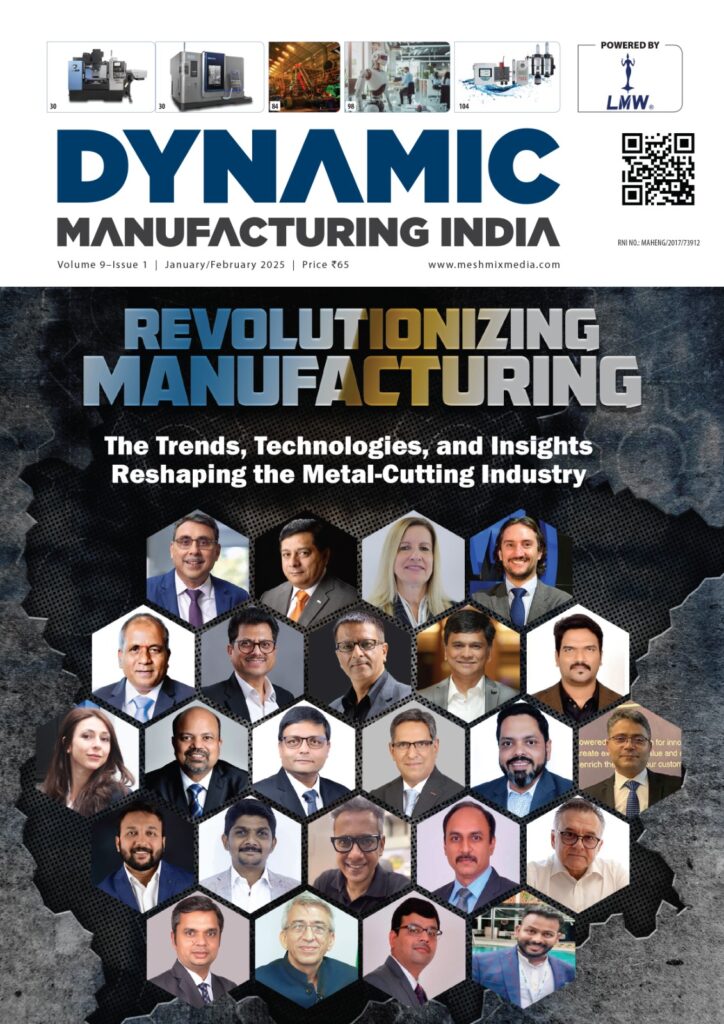
Link for the magazine – https://www.machineinsider.com/dynamic-manufacturing-india-jan-feb-2025-edition/