The Path Forward
Mahesh Bagdi, Founder & CEO of Goodwill Associates, Discusses Innovations, Sustainability, and the Future of Manufacturing
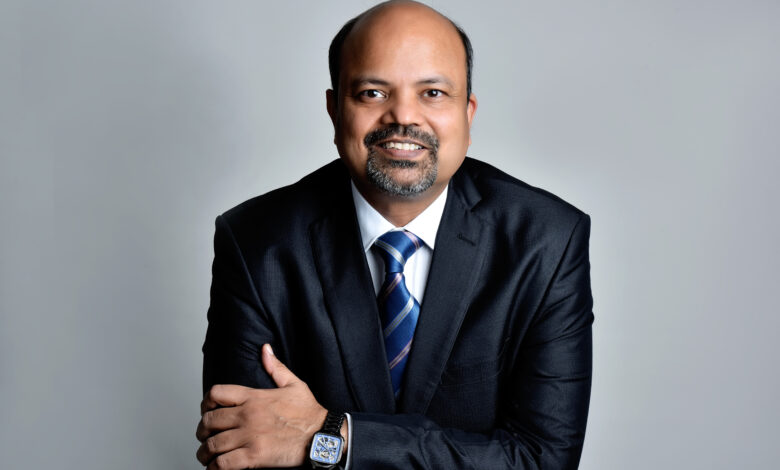
1) What recent advancements in metal-cutting technology have had the most transformative impact on efficiency and precision?
Recent advancements in metal-cutting technology have significantly transformed efficiency and precision in manufacturing processes. Some key developments include:
- Additive Manufacturing (3D Printing for Metal)
- Impact on Efficiency: 3D printing of metal parts enables the creation of complex and optimized geometries that were previously difficult or impossible to achieve with traditional cutting methods. This reduces the need for additional processes, saving time and minimizing material waste.
- Impact on Precision: Metal 3D printing ensures high precision, maintaining intricate details throughout the production process, offering tighter tolerances and reducing the need for post-processing.
- High-Speed Machining (HSM)
- Impact on Efficiency: High-speed machining uses specialized tools and advanced CNC machines to perform metal cutting faster and more efficiently. This reduces cycle times and enables the production of higher volumes of parts without compromising quality.
- Impact on Precision: HSM technology ensures high precision even at high cutting speeds by maintaining consistent tool performance and minimizing wear. This results in better surface finishes and tighter tolerances.
- Intelligent CNC Machines and AI Integration
- Impact on Efficiency: The integration of artificial intelligence and machine learning into CNC (Computer Numerical Control) machines has led to smarter production processes. AI algorithms optimize cutting paths, reduce unnecessary movements, and even predict tool wear, minimizing downtime.
- Impact on Precision: AI-driven adjustments maintain precision by compensating for tool wear and environmental factors, ensuring consistent quality throughout the production process.
- Cryogenic Machining
- Impact on Efficiency: Cryogenic machining uses liquid nitrogen to cool the cutting area, significantly reducing heat buildup. This allows for higher cutting speeds and extends tool life.
- Impact on Precision: By minimizing thermal distortion, cryogenic machining enhances cutting precision and improves the overall surface quality of workpieces.
- Advanced Coatings for Cutting Tools
- Impact on Efficiency: New tool coatings, such as diamond-like carbon (DLC) or titanium nitride (TiN), increase the longevity of cutting tools and improve their ability to cut through harder materials without premature wear. This reduces the frequency of tool changes and extends machinery life.
- Impact on Precision: Coated tools maintain sharper edges for longer, ensuring consistent precision throughout extended machining processes.
2) How is the industry adapting to sustainable manufacturing practices, and what specific initiatives are helping to reduce environmental impact?
- Energy-Efficient Machining Technologies
- Initiative: Metal-cutting companies are investing in advanced machinery designed for higher energy efficiency. This includes CNC machines with energy-saving features, such as automatic power shutdowns, optimized energy consumption during idle times, and advanced control systems that improve overall energy use.
- Impact: These machines consume less power during production, leading to lower energy costs and a reduced carbon footprint. By improving energy efficiency, companies can also reduce reliance on non-renewable energy sources.
- Use of Sustainable Materials
- Initiative: The industry is increasingly shifting towards using recycled metals, such as scrap steel and aluminum, which require less energy to process compared to virgin materials. Companies are also exploring more eco-friendly cutting fluids to reduce the environmental impact of the cutting process.
- Impact: Recycling metals reduces the need for mining new raw materials, conserving natural resources and minimizing environmental degradation. The use of sustainable cutting fluids, such as biodegradable or water-soluble alternatives, helps reduce harmful chemical waste generated during machining.
- Waste Reduction and Recycling
- Initiative: Metal-cutting operations are focusing on reducing scrap and optimizing material use. Techniques like near-net shape manufacturing, where parts are designed to closely match the desired final shape, help minimize material waste. Additionally, metal chips and other by-products are being recycled and reused in other processes.
- Impact: These practices reduce waste and improve material efficiency, decreasing the amount of waste sent to landfills. Recycling metal chips also reduces the cost of raw materials and the energy required to create new components.
- Advanced Cutting Tools and Coatings
- Initiative: The development of high-performance cutting tools with advanced coatings, such as DLC or TiN, increases tool life and reduces wear. Longer-lasting tools result in fewer replacements and reduce raw material consumption associated with tool production.
- Impact: Extended tool life lowers the frequency of tool replacement, reducing waste from discarded tools. This helps reduce environmental impact and improves efficiency by minimizing downtime and the need for retooling.
- Coolant and Lubricant Optimization
- Initiative: The metal-cutting industry is adopting more sustainable and efficient coolant and lubricant systems. These systems use less fluid while improving cooling and lubrication effectiveness during the cutting process. The use of non-toxic, biodegradable coolants and oils is also increasing.
- Impact: By optimizing the amount of coolant and lubricant used and selecting environmentally friendly options, companies can reduce harmful chemical waste and improve the sustainability of the production process.

3) With digitalization reshaping manufacturing, what new skills are essential for today’s workforce, and how is the industry addressing the skills gap?
As digitalization reshapes manufacturing, essential skills for today’s workforce include proficiency in advanced technologies like IoT, AI, robotics, and data analytics. Employees must also be skilled in programming, automation, and cybersecurity to operate and secure smart factories. Additionally, understanding digital twin technology, machine learning, and cloud computing is crucial. To address the skills gap, the industry is investing in training programs, certifications, and partnerships with educational institutions. Companies are also promoting upskilling initiatives and on-the-job learning to ensure workers can adapt to new technologies. Industry 4.0-driven initiatives and government-backed apprenticeship programs are further helping bridge the gap by equipping the workforce with the competencies required to thrive in a digitally advanced manufacturing environment.
4) What trends are driving the current demand for metal-cutting solutions, and how do you foresee the industry adapting to these trends?
The current demand for metal-cutting solutions is driven by several key trends, including:
- Increased Automation and Industry 4.0
- The shift toward smart manufacturing, with integrated automation, IoT, and AI-driven systems, is increasing the need for precise and efficient metal-cutting solutions. Manufacturers require machines that can operate autonomously, optimize cutting paths, and handle complex designs.
- Adaptation: The industry will focus on developing smarter machines with enhanced connectivity, predictive maintenance capabilities, and real-time monitoring to ensure smoother operations and improved productivity.
- Customization and Complex Geometries
- The demand for customized products and parts with complex geometries (especially in industries like aerospace, automotive, and medical devices) is driving the evolution of metal-cutting solutions.
- Adaptation: Metal-cutting technologies will evolve to offer more precise, flexible, and versatile machining capabilities, including hybrid technologies that combine 3D printing with traditional cutting methods.
- Sustainability and Waste Reduction
- As manufacturers prioritize sustainability, there is a growing emphasis on reducing waste, recycling materials, and minimizing energy consumption during metal cutting.
- Adaptation: The industry will adopt greener cutting fluids, optimize machine energy efficiency, and invest in waste recycling systems to meet sustainability goals while maintaining performance.
- Demand for High-Performance Materials
- The rise of high-strength materials, such as titanium, high-performance alloys, and composites, used in industries like aerospace and energy, is driving the demand for advanced cutting solutions.
- Adaptation: The industry will develop specialized tools, coatings, and machining techniques to handle these tougher materials, ensuring efficient and precise cutting with reduced tool wear.
5) What do you view as the most significant challenges facing the metal-cutting industry today, and what steps is your organization taking to stay competitive?
- Rising Material Costs
- Challenge: The cost of raw materials, especially high-performance metals and alloys, is rising, putting pressure on manufacturers’ profit margins.
- Response: Companies are adopting strategies like material optimization, recycling metal scraps, and investing in new cutting technologies that minimize waste and maximize material efficiency.
- Skilled Labor Shortage
- Challenge: There’s a growing skills gap as new technologies like automation and AI require a workforce proficient in digital tools and advanced manufacturing techniques.
- Response: Many companies are focusing on upskilling their current workforce through training programs, collaborating with educational institutions, and offering apprenticeships to cultivate a skilled workforce.
- Technological Integration
- Challenge: Rapid advancements in technologies such as automation, IoT, and AI require manufacturers to constantly adapt to maintain efficiency and competitiveness.
- Response: Organizations are investing in smart manufacturing technologies, digital twins, predictive maintenance, and AI-driven solutions to enhance productivity, reduce downtime, and improve precision.
- Sustainability Pressures
- Challenge: Environmental regulations and the growing demand for sustainable practices are pushing companies to reduce their carbon footprint and waste production.
- Response: Companies are shifting towards energy-efficient machines, using eco-friendly cutting fluids, optimizing waste recycling, and adopting sustainable manufacturing processes to align with both regulatory requirements and market demands.
About us
Goodwill Associates was founded by Mahesh Bagdi in 2002 with an initial capital of Rs. 40,000/= operating out of a 144 Sqft office space, has grown multifold since then and today we are Authorised Distributors of 4 MNC companies, who all are pioneers in their respective industries, namely
NTN Corporation – Bearings (Since 2005), Total Energies – Lubricants & Greases (Since 2016) MR Widia – Metal Cutting Tools (Since 2023) & Lubrilog – Speciality Oils & Greases (Since 2024)
With an experience of over 31+ years in this industry we have seen many changes of trends, but the only thing that still remains constant is the customers seek for Genuine Products with quality service, which Goodwill Associates has been fulfilling for the last 23 Years successfully. Our customers under both OEM & MRO category rely on us for proper planning & on time delivery of the correct product at the right prices.
NTN Corporation is a leading world class Japanese Bearing manufacturer established in 1918, which commands a 50% market share in the Machine Tool Market of JAPAN & this high penetration is due to their ability to focus on delivering a superior product with high standards of precision.
Total Energies is the world number 2 Oil & Gas company and was established in 1924. Total has one of the widest range of products to offer for all segment including Metal Working Fluids which is both Made in India & Imported from France with exuberant quality
MR Widia is again from the house of Kennametal Widia who are the original inventors of Metal Cutting Carbide Inserts. Our pedigree is very strong and MR Widia has the advantage of coming from a rock solid base. We have a wide range of ISO Turning ,Milling & Grooving Inserts, End Mills, TC & NTC Drills, Holders & Face mills
Lubrilog is completely into specialty Lubricants & Grease with a specific focus on perfluorinated lubricants, Whatever may be the application requirements, Lubrilog offers to develop customized high performance premium quality lubricants. Today Lubrilog’s solutions can be found in diverse industrial segments such as Automobile, Aerospace, Nuclear, Pharma, Food etc
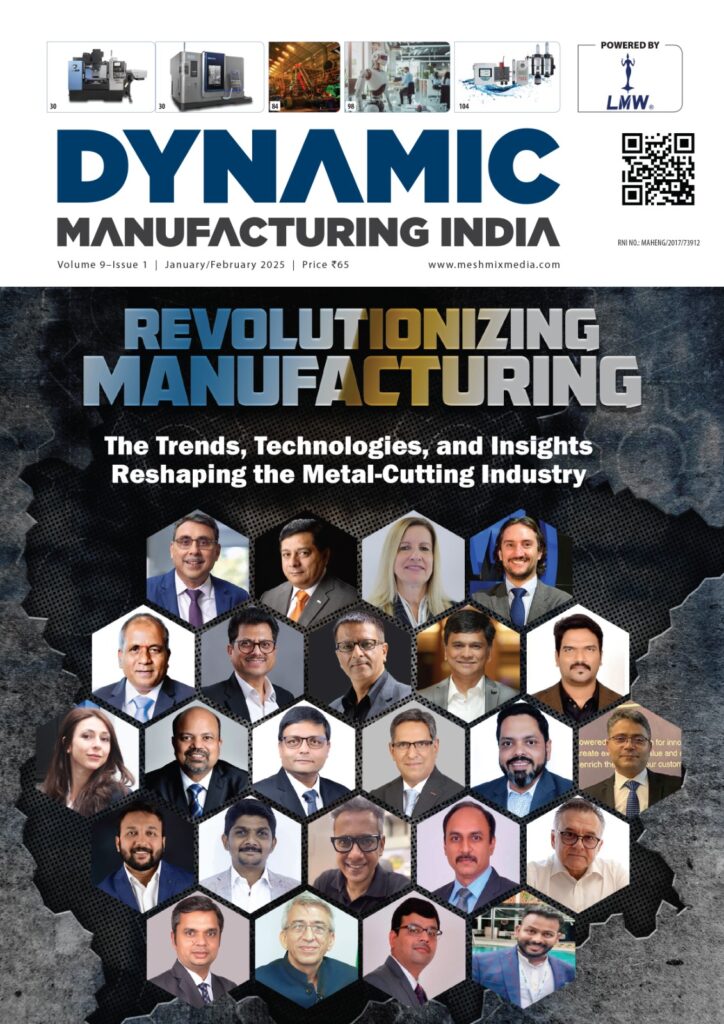
E copy of the magazine – https://www.machineinsider.com/dynamic-manufacturing-india-jan-feb-2025-edition/