Understanding Different Types of Blasting and What’s Right for You
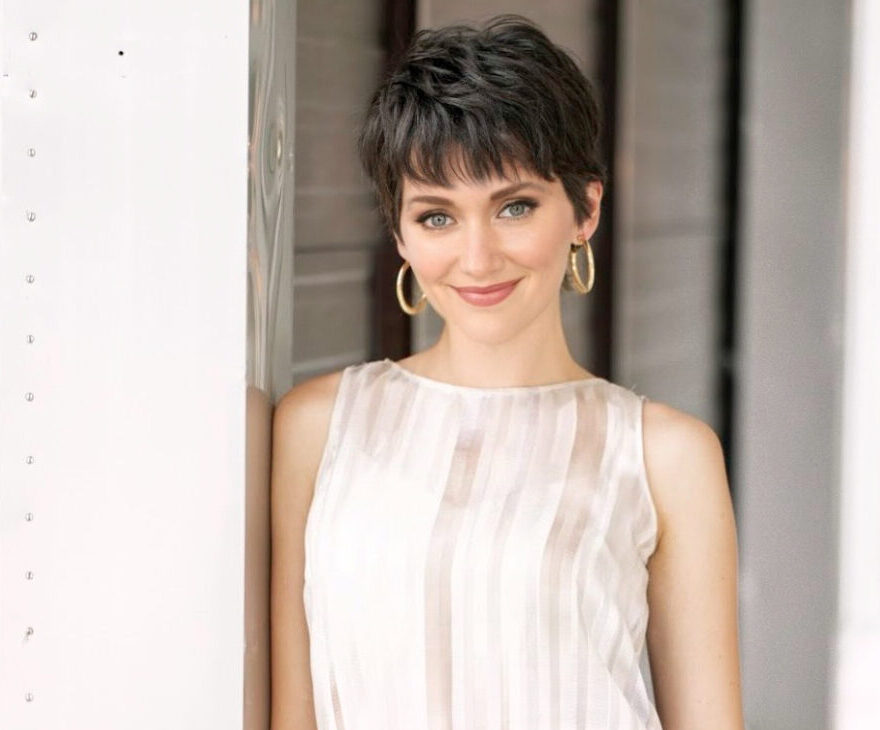
sandblasting” remains the term of choice for many manufacturers
While “sandblasting” remains the term of choice for many manufacturers, you’re not limited to sand as your abrasive media. Glass beads, aluminum oxide, and plastic abrasives are all good alternatives to sand — and, in many cases, they’re likely to be a better fit.
These are the most common materials used in abrasive blasting and the applications they will work best in.
1. Sand
Sand has historically been one of the most common types of abrasive media, but it’s fallen out of use in recent years due to the presence of silica.
Silica dust, produced by the blasting process, is bad for the lungs and can cause a condition called silicosis. This is similar to other occupational lung diseases, like black lung, dust pneumonia, and asbestosis.
It’s possible to safely use abrasive materials that contain silica. However, necessary safety measures are expensive and may render the use of sand impractical in some cases.
Advantages of Sandblasting
- Sand is cheap, readily available and easy to source.
- The sharp edges and uniform size of sand grains make it an effective abrasive material.
Disadvantages of Sandblasting
- Silica dust presents a major occupational hazard.
- Safety controls for silica dust exist — for example, improved site ventilation and the use of respiratory protection — but they are often expensive, impractical or ineffective.
- In some countries — including the United Kingdom and much of the EU — using sand in abrasive blasting is prohibited.
- While still legal in the U.S., the use of sand is increasingly regulated.
For these reasons, sand has mostly fallen out of favor.
2. Aluminum Oxide
Aluminum oxide is a popular alternative to sand. The material is tough, making it a good fit for removing stains, dirt and rust from equally strong metals.
Advantages of Aluminum Oxide
- It’s tougher than many other blasting media and is a good fit for blasting stronger materials.
- Most spent aluminum oxide can be reclaimed and used for future blasting jobs.
- It’s rust-resistant and can be used in wet blasting.
Disadvantages of Aluminum Oxide
- It may be too strong for certain materials.
- Aluminum oxide’s toughness can be hard on blasting equipment.
If you need a tough material that’s suitable for blasting with water rather than air, aluminum oxide is one of the better options available. Its recyclability also makes it a good fit for lean and green manufacturers wanting to cut down on waste or improve business sustainability.
3. Plastic Media
Plastic media is a sandblasting material made from angular pieces of plastic. It’s free of silica and fairly durable but isn’t as aggressive as options like aluminum oxide.
Advantages of Plastic Media
- It’s less aggressive than other blasting media, making it suitable for key abrasive blasting tasks like removing flash from plastic casts and cleaning fiberglass.
- It features high durability.
- Plastic media is available in a wide range of shapes and sizes.
- It produces little dust.
Disadvantages of Plastic Media
- It may be too gentle for some tasks — like finishing metal objects or stripping hard materials.
- It’s slower than other, tougher materials for tasks like cleaning.
4. Glass Beads
You can also use fine glass beads as blasting media.
Advantages of Glass Beads
- They are reusable and may last for as many as six cycles before being replaced.
- Glass beads can be used in suction feed-blasting cabinets.
- They don’t produce silica dust.
Disadvantages of Glass Beads
- Like plastic, they may be slower than other blast media.
- They don’t leave a profile on blasted surfaces, which may make paint less adhesive.
- They’re not as reusable as media like steel grit or aluminum oxide.
Glass is a good fit for facilities that want to use more affordable suction feed-blasting cabinets or only need materials for softer substrates.
5. Steel Grit and Steel Shot
Steel grit or shot is often the go-to media for heavy-duty jobs that require a tough and durable blasting material. Steel grit is angular and irregular in shape, while steel shot is round.
Advantages of Steel Grit/Shot
- Like aluminum oxide, steel grit is durable and reusable.
- It’s a good fit for tougher substrates and more intensive polishing and finishing.
- Steel grit breaks down less than other materials upon striking a surface, leading to less waste and dust generation.
Disadvantages of Steel Grit/Shot
- It may be too hard for softer substrates.
- It’s not as strong as aluminum oxide.
The Best Blast Media Available
The best blasting media will depend on the particular task — although the sand is generally not the best option. For tougher substrates, hard materials like steel and aluminum oxide will be a good fit. Gentler options like plastic media and glass beads may be useful for softer substrates, so long as slow blasting progress isn’t an issue.
Once you understand the pros and cons of different materials, the right choice for your operation should become clear.
Jane Marsh
Jane Marsh is the Editor-in-Chief of Environment.co. She covers topics related to climate policy, sustainability, renewable energy and more.